How IT Can Be Applied Intelligently to Support People
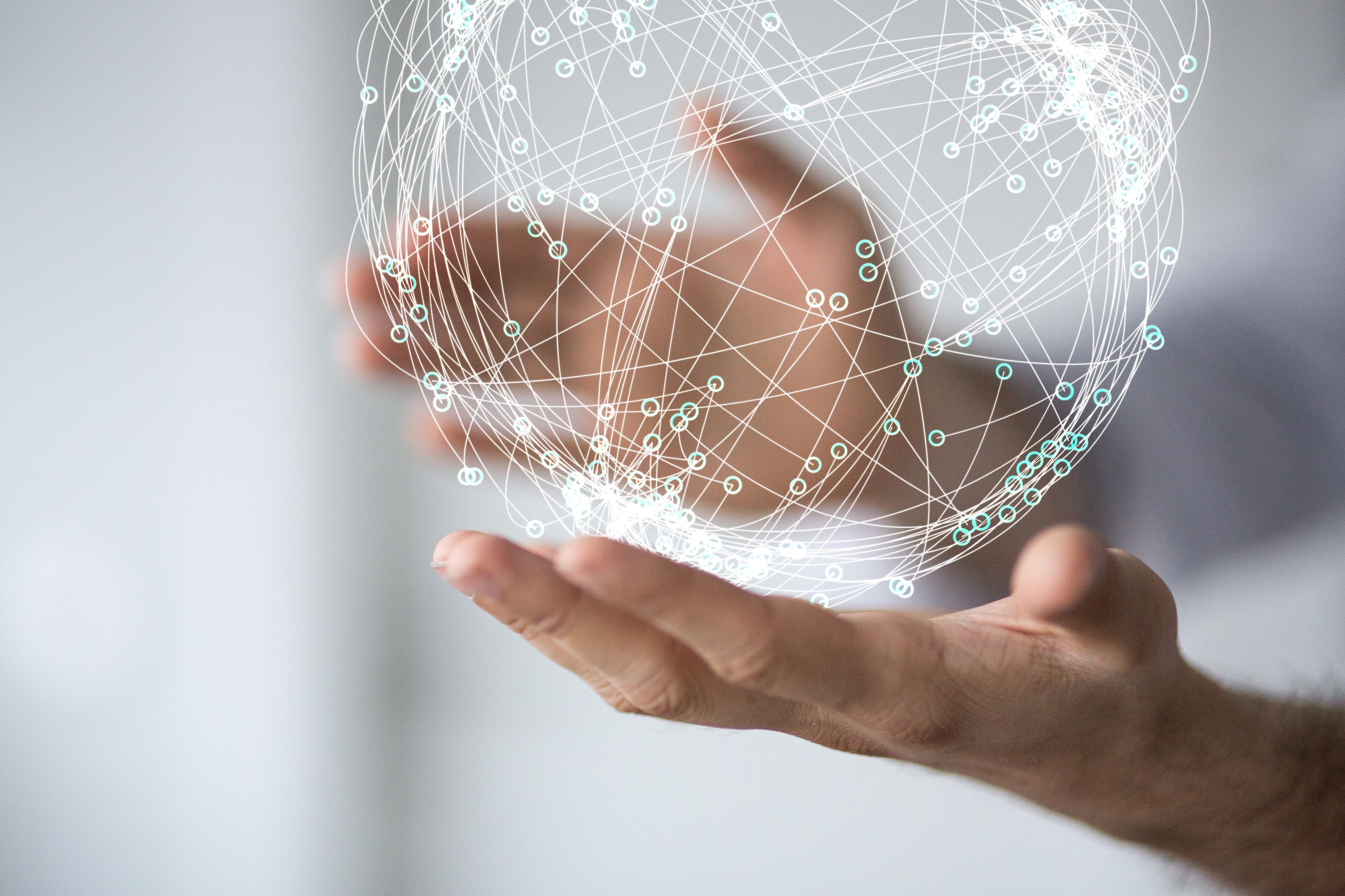
There seems to be a consensus in public dialogue that automation and computer technology are the key driver of macro-level productivity. For example, President Obama promised to reduce out of control health care costs. A centerpiece of his policy is encouraging the use of technology, such as electronic health records and other forms of healthcare information technology (IT). The estimated cost, including government subsidies, to implement electronic health record (EHR) systems nation-wide over 10 years was close to $100 billion. While it is appealing to think that digitizing all records in U.S. hospitals and investing in sophisticated hardware, facilities, and medical equipment will gain efficiencies over the current system and infrastructure, current data indicate otherwise. The United States already has the most advanced healthcare technology in the world, but spends more than any other country in per capita healthcare spending, as well as spending about 16 percent of its gross domestic product (GDP) on healthcare. This challenges the common assumption that new technology has a simple and direct effect on cost reduction in health care.
Let’s consider an example of poor implementation of the type of technology President Obama advocates. During an EHR implementation at Healthcare, Inc. (pseudonym), the medication reconciliation module had not yet been implemented. Technical training was done on the new module, and it was then implemented. The intention was to improve patient safety and quality related to the medication reconciliation process. In addition, the intention was to meet federal regulations and decrease vulnerability to malpractice law suits. This process was deployed mechanistically, with very little input from the staff. Shortly after implementation, there was a sudden drop in inpatient satisfaction related to the discharge process. Staff members were very unhappy with the process, and found the medication reconciliation process to be cumbersome and time-consuming, and thought the previous process was more effective and efficient. Patients were unhappy with the lengthy process that delayed their return home.
My student, Brock Husby, was brought in as a lean coach to try to understand the problem and help them improve the process. After going to several nursing units that experienced this drop in satisfaction and meeting with staff, data showed that the process time to complete medication reconciliation had increased two to three times above the previous process, and with no accompanying staffing model changes (used for maintaining patient to staff ratios). This resulted in nurses being pulled away from the patient’s bedside at the time of discharge (a critical time for closure in the relationship with the patient and a significant driver of patient satisfaction).
As I have written in The Toyota Way, Toyota is certainly at the cutting edge of computer technology both in their vehicles, like the Prius, and as the backbone of their infrastructure for product development, manufacturing, scheduling and logistics, sales processes, warehouse management and more. Yet their philosophy of technology is to use it selectively as an enabler of processes that have been greatly simplified for human use. They will often say that technology does not make processes better, but makes already well-designed processes faster, acting as a catalyst.
The general approach that Toyota uses (that was not used by Healthcare, Inc.) is:
- Have a clearly defined need/problem.
- Think carefully about the current process and how waste can be eliminated without the technology, prior to introducing new technology.
- Consider the skills required and develop a plan for training people and involve them in the introduction.
- Introduce the technology first on a pilot basis to prove its capability, and work out the bugs and the process of introducing it.
- In a step-by-step way, bring the technology into other locations over time with local management taking ownership of planning and leading the introduction and building on lessons learned from other sites.
- Continuously improve the technology and its processes through ideas by the people who directly use it.
The perceived need for technology in Healthcare, Inc. was to have a way to ensure that any new medications that were given in the hospital (or had been removed) were reconciled with their medications that they were taking at home. Before the EHR, this need was met by a paper process. The paper version of the process had been developed over a number of years and the staff had a deep understanding of the process, but the electronic version was significantly different, with little resemblance in form or logic. There was minimal consideration for customizing this module to mirror the current process or to better understand the interaction with the nurses. There was no pilot for learning and little training of the nurses.
Therefore, they viewed the technology as routine and standalone with no regard for how it affects the way nurses work or the accompanying social system. The nurse’s job is highly complex and dynamic, and entering data is a very minor part, yet the technology made this a disproportionately time consuming job. This complex process distracted the nurses pulling them away from the patient. As a result of the approach taken to selection and deployment, it wasn’t accepted by the staff (a social failure), it inhibited workflow and patient care (a technical failure), and threatened patients returning to the hospital due to dissatisfaction (a business failure).
The approach Brock provided guidance on was more like the Toyota model. First, on a pilot basis, work closely with the nurses to understand the entire process and how the technology could best support that process. Then redesign the technology so it is integrated and adds value, without additional burden. The actual reprogramming of the technology turned out to be simple once the actual process was understood and the technology designers worked closely with the nurses. It then became the enabler as was originally intended.
Brock concluded, after a series of consulting jobs in which he was asked to help clean up the mess after poor technology deployment, that organizations did not think about how to effectively integrate technology with people and processes. Technology was a thing onto itself assumed to fix all problems. He concludes:
“The overly mechanistic approach results in a lack of integration driven by an overly rigid timeframe and inflexibility that does not allow for iterative problem solving. They encounter surprising complexity and unanticipated interactions with the broader environment of the technology, resulting in a “crisis” and uncertainty about how to proceed … The application of deceptively complicated technology in an overly mechanistic way results in increased complexity. A more organic approach is required to untangle the complexity.
In other words, relatively simple, low-tech approaches to understanding can head off overcomplicating processes. These simple approaches include directly observing firsthand the process, talking to the people who will use the technology, trying to understand the fixes they have made informally which are key to making the process work, and then using pilots to iteratively experiment with different approaches in each case checking what was actually learned.
This is the approach used by an IT company, Menlo Logisitics. They even created a new role, the technical anthropologist, to live with the users and empathetically understand their needs and how technology can address those needs. Weekly meetings with the customer are used to evaluate the work of that week in developing the technology which leads to continuous improvement throughout the process. By the time the technology goes live it has been through hundreds of iterations and customer feedback. Menlo has not had a customer complaint in years. They call the process of creating software that is easy to use and helpful Joy, Inc., as described in their book by that name. You too can bring joy to your customers and employees by selecting and deploying technology in the right way.
This article is based on the doctoral dissertation of one of Dr. Jeffrey Liker’s former students, Brock Husby, “Integrating People, Process, and Technology in Lean Healthcare,” University of Michigan, 2012
Dr. Jeffrey Liker is professor of industrial and operations engineering at the University of Michigan and author of The Toyota Way. He leads Liker Lean Advisors, LLC and his latest book (with Gary Convis) is The Toyota Way to Lean Leadership.
- Category:
- Industry
- Manufacturing
Some opinions expressed in this article may be those of a contributing author and not necessarily Gray.
Related News & Insights
Manufacturing
Applying the Toyota Production System (TPS) to Automated Manufacturing Processes: Honsha Example
Industry
July 26, 2013Manufacturing
How Akio Toyoda Is Living Up to the True Toyota Way
Industry
October 09, 2014Manufacturing, Construction
The Toyota Way 2001 House: Lean for the 21st Century
Industry