How Akio Toyoda Is Living Up to the True Toyota Way
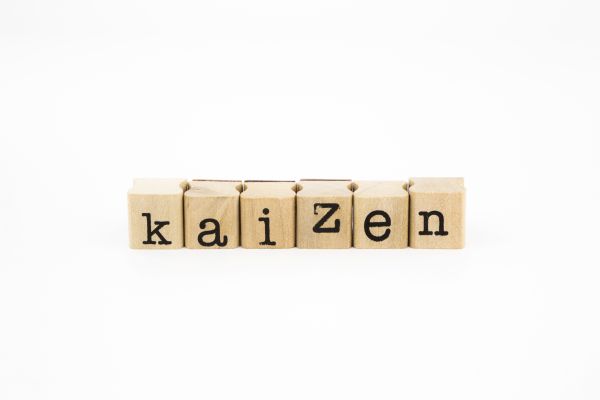
Before the Toyota recall crisis of 2009-2010, I was writing The Toyota Way to Lean Leadership with Gary Convis, former Managing Officer of Toyota Motor Corporation. For that book, I studied Akio Toyoda, who would become the newest president of Toyota. Gary knew him personally and told me great stories.
Gary met Akio at NUMMI (former Toyota-General Motors joint venture in California) when Akio was a relatively young manager. Akio was assigned to NUMMI to learn and to experience America. It was clear to everyone he was like a prince, a likely future president. It was also clear he did not act like it. He was humble, and his father was strict. Akio would not get special privileges; he would work his way from the bottom up. Still, Akio had strings he could pull.

His contacts came in handy when NUMMI experienced the breakdown of a stamping press the size of a small house. As Toyota does not keep much inventory or extra equipment, the crash of the press threatened to shut down production. NUMMI needed key components from Japan, which Akio got expedited using his network. However, he went further. Repair crews were working around the clock, and Akio wanted to support them however he could. He could not repair the press, but he could provide moral support. He stayed with the crew, even sleeping in a cot on the shop floor.
With this background, it is perhaps not surprising that in his first internal communication as president, he vowed to be the most active president at the gemba—where the work is taking place. After he became president, I began hearing stories about how he would appear unannounced at various Toyota locations, including the dealership in Ann Arbor, Michigan, where I live. No large entourage, no big announcement, and certainly no journalists–he was just there, and he went everywhere including climbing under cars to understand the dealership’s strengths and weaknesses.
The Toyota Production System is about doing more with less and constantly challenging people to reach higher levels of excellence. People are challenged to improve the process and themselves with the help of leaders, and in return, they become stronger, more confident and are provided with job security as well as a comfortable standard of living. In my most recent visit with Akio Toyoda in the fall of 2013, he said something interesting:
“I am in my fourth year as president. For three years there was a crisis every year—the recalls, the great earthquake of Japan, and the largest flood in Thailand history. This is the first year there is no crisis and it is my most challenging year as president.”
Crises make it easy to motivate people to do extraordinary things and reach new heights of performance. This is more difficult when the company is healthy and earning the most profit on the most sales in the history of the auto industry.
Often I read articles about Toyota by journalists who do not understand the somewhat peculiar philosophy of the Toyota Way. Why would Akio Toyoda come out with a pronouncement that Toyota will not build any new production facilities in one of the fastest growing markets in the history of auto? Is he afraid? Is it a strategic blunder?

The answer is in the twin concepts of challenge and kaizen, or continuous improvement. Without a challenge, kaizen will dwindle and people will find the easiest way to meet their objectives. According to some, building new factories is the simplest approach to increase capacity to meet demand, and also the best method to reduce costs for those who build new factories in low-wage countries. However, Akio Toyoda wants true kaizen, which is to find ways to do more with less.
This became clear when Akio Toyoda put on hold efforts to build a new production facility in Mexico. He asked whether “we have exhausted all the possibilities for improving capacity in North America with existing locations.” Now, the existing locations are in relatively high-wage countries—the U.S. and Canada. It is easier to build a plant in Mexico and reduce labor costs immediately, but that is not the Toyota Way. Through creatively increasing capacity in existing plants, Toyota will find an overall lower cost solution and maintain the commitment of job security to team members at the existing sites. When capacity is squeezed out of existing plants, Toyota will likely build a factory in Mexico to serve the Latin American market.
The basics of the Toyota Way come down to respect for people and continuous improvement. Akio Toyoda is passionately focusing on both.
Dr. Jeffrey Liker is professor of industrial and operations engineering at the University of Michigan and author of The Toyota Way. He leads Liker Lean Advisors, LLC and his latest book (with Gary Convis) is The Toyota Way to Lean Leadership.
Some opinions expressed in this article may be those of a contributing author and not necessarily Gray Construction.
- Category:
- Industry
- Manufacturing
Some opinions expressed in this article may be those of a contributing author and not necessarily Gray.
Related News & Insights
Distribution, Specialty Equipment
Equipment Manufacturing Trends for 2025
Industry, Opinion
Advanced Technology, Specialty Equipment
How an Equipment Design-Build Partner Benefits Your Business
Industry, Opinion
Manufacturing
Gray, UBE C1 Chemicals America, Inc., and Cornerstone Energy Park Celebrate Groundbreaking for New Manufacturing Facility
Corporate News
February 26, 2025