How Data Collection, Analysis and Automation are Improving Food Safety and Quality in the U.S.
Today’s demanding consumer is challenging food safety and quality standards like never before. The growing demand for food and beverages that are free of allergens, gluten, pesticides and GMOs are pushing food and beverage producers to redesign their quality and safety programs. And, today’s consumer not only demands the foods they consume to be free of certain ingredients or contaminants—they want proof.
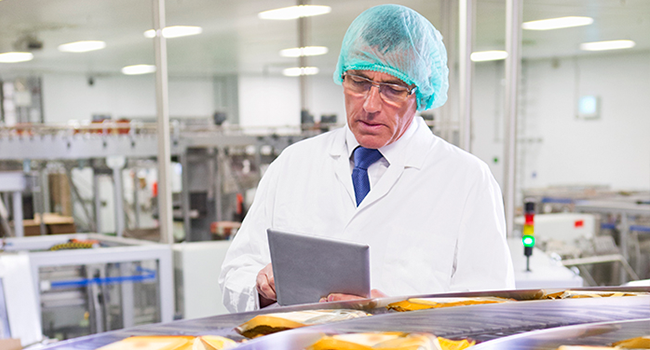
Add to that increasingly stringent regulatory standards required by the Global Food Safety Initiative (GFSI) and the Food Safety Modernization Act (FSMA), it’s never been a more challenging time to be in the food and beverage business. Transparency and traceability of ingredients are simply a must for producers that want to maintain customer satisfaction while meeting increasingly stringent regulatory standards.
The USDA recalled over 21 million pounds of meat and egg foods in 2015. Undeclared allergens were the leading cause, accounting for nearly half of these recalls.
Delivering the highest-quality foods that are safe for customers to consume continues to be priority number one for U.S. food and beverage producers, and the focus is on preventing quality and safety breaches rather than reacting to them.
As one might expect, the U.S. food and beverage industry is rising to the occasion, tackling the increasing regulatory challenges and rising consumer demands head on. One key way they are doing so is by improving the way safety and quality data is collected and analyzed during the manufacturing process.
Barry Maxon is founder and president of Safety Chain—a company that provides software solutions to help food and beverage producers automate and collect data from the continuum of their food safety and quality programs. According to Maxon, the move from manual collection of data on food and beverage production lines to automated data collection has been the most significant and impactful change in food safety and quality over the last two decades. He says that, historically, food quality and safety information was checked and collected using pens, paper and spreadsheets, and then stored in filing cabinets to be accessed at a later date for audits or in case of a recall.
“It was very difficult to measure the effectiveness of food safety and quality because, fundamentally, the data of all of these different processes were locked up in paper files and spreadsheets that didn’t have any ability to connect the dots,” said Maxon. “When you’re managing a manual process on paper, things fall through the cracks. Trends aren’t seen soon enough, and so you wind up being very reactionary as opposed to preventative, which is the whole thrust of GFSI standards and the Food Safety Modernization Act—to make your food safety programs much more preventative versus reactionary.”
Maxon says most of today’s food and beverage producers have transitioned from a manual approach to an automated one, using advanced operating systems to collect, analyze and store massive amounts of data from automated equipment across food production lines. But today’s food and beverage producers have taken it a step further and want what he calls “harmonization” in their data collection processes, across all of their facilities.
“Harmonization is more than just doing things the same way,” said Maxon. “Harmonization is the ability to actually monitor that data collection is being done and being done correctly. Harmonization is going a step beyond a standard. It’s ensuring closed-loop management to make sure your programs are actually being implemented effectively in the proper way.”
Now, with more data at their fingertips, food and beverage producers can extract and analyze data like never before. Maxon says his company’s operating system allows producers to capture every food and safety quality event, expose that data through a variety of views, and analyze the data in real-time.
“Was the metal detector check done on time? Was there a third-party laboratory analysis of a sample that indicated a positive for E-coli, or any other microbiological contaminant? Was a net-weight sample taken and was it within parameters, or not?” said Maxon of some of the questions that can now be answered, and answered quickly.
Food and beverage producers that have been resistant to change might say integrating sophisticated data collection operating systems is cost-prohibitive, but experts in the industry disagree.
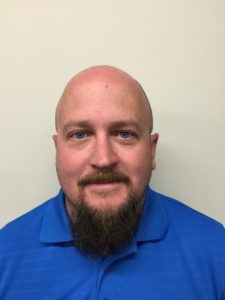
Dan Schuster is a senior process control engineer for Schenck Process, a global market leader in measuring and process technologies in industrial weighing, feeding, screening and automation equipment. He says the cost of even the most sophisticated data collection system has followed advances in computer technology, like desktop computers and cell phones. As the availability of technology increases, the cost of these systems decreases.
“A couple of decades ago, it might cost hundreds of thousands of dollars to implement such a system, but now, it can be done for under $10,000,” he said. “And what used to fill a room is now sitting on your desk.”
Maxon concurs, and added that it’s important to look at the cost of adopting automation software in the context of a return on investment.
“It’s really not an operating expense when you look at a return on investment model,” he said. “I would encourage companies to take a practical look at it because, if they’re not doing it today, they’re running a significant risk in liability by not adding preventative controls.”
- Category:
- GrayWay
- Food & Beverage
- Manufacturing
Some opinions expressed in this article may be those of a contributing author and not necessarily Gray.
Related News & Insights
Food & Beverage
4 Benefits of Virtual Reality to Food and Beverage Processing
Industry
Food & Beverage, Construction
Food Processing on the Rise, Thanks to Technology & Innovation
Industry
Food & Beverage
Where Technology & Organic Food Processing Intersect
Industry
October 24, 2013