How Technological Advancements Are Changing Modern Manufacturing
Manufacturing in 2015 looks nothing like it did just 20 years ago. Technological advancements in automation and robotics have transformed the shop floor from “dark, dirty and dangerous” to clean, high-tech centers of efficiency offering challenging and highly skilled jobs. With the economy improving, manufacturers are taking advantage of the opportunity to invest more in technologies that have proven to increase throughputs and impact the bottom line.
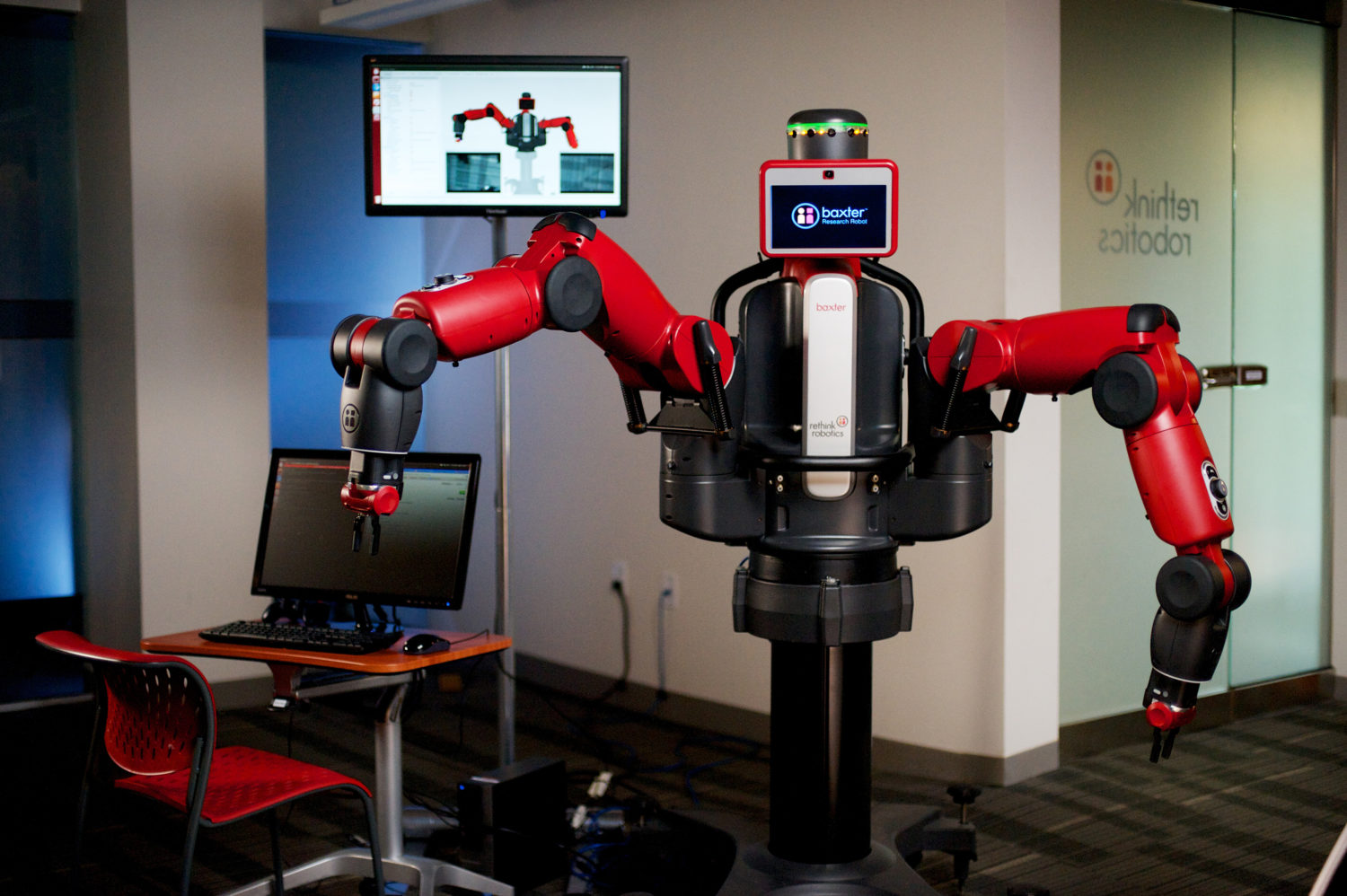
One technological area experiencing rapid growth is advanced robotics. While robots have been integrated into many large manufacturing environments, new, smaller, more sophisticated robots are proving to be a wise investment for manufacturers of all sizes.
Earlier this year, the Robotics Industries Association (RIA) reported that 2014 was a record-setting year in robot orders.
According to the RIA, “a total of 27,685 robots valued at $1.6 billion were ordered from North American companies during 2014, an increase of 28 percent in units and 19 percent in dollars over 2013. Robot shipments also set new records, with 25,425 robots valued at $1.5 billion being shipped to North American customers in 2014. Shipments grew 13 percent in units and six percent in dollars over the previous records set in 2013.”
What’s behind this unprecedented growth?
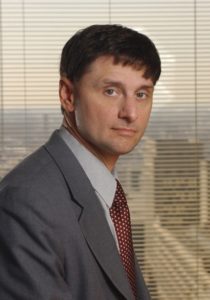
Boston Consulting Group’s (BCG) Hal Sirkin, who has observed the evolution and integration of robotics into modern manufacturing plants over the past couple of decades, says a big factor is decreasing cost.
“The historical issues were that robotics were basically only used in many heavy manufacturing situations like automotive plants because the economics of the labor costs were pretty high,” said Sirkin, senior partner and managing director of BCG. “What’s going on now is that the cost to use robotic labor is getting a lot lower than the cost to use human labor, and so we’re watching substitution not only on the very large machines that cost a half-million dollars, but on equipment that is much smaller.”
While the automotive industry continues to be the primary driver of growth in robotics with orders increasing 45 percent year over year, non-automotive industries are also gaining steam, growing seven percent over 2013. According to the RIA, other industries showing significant growth were plastics and rubber (25%), semiconductor and electronics (21%), and metals (16%). Most often, industrial robots are being used for arc welding, material handling and assembly applications.
Bob Doyle, director of communications for RIA, says another big reason for the spike in robot orders is due to technological advancements in robotics, like gripping and vision capabilities that allow robots to see and execute “pick-and-place” operations that were previously not possible. One of the hottest types of robots on the market today, he says, are those that work in collaborative environments, side-by-side with humans—a relatively new development in the industry.
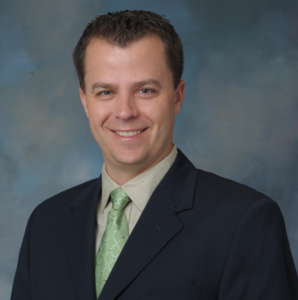
“When you think of industrial robots, you think of them behind big fences because they can be dangerous,” said Doyle. “But the new, collaborative robots include a lot of advances like being able to work closer to humans. They don’t take up as big of a footprint, which makes them easier to deploy in certain operations. They might be able to move from one operation to another, rather than like an industrial robot that’s just strictly performing one operation. They are cheaper, certainly, and that makes the return-on-investment faster.”
Sawyer by Rethink Robotics is one example of a collaborative robot that is getting a lot of attention in the manufacturing world. The robot is relatively inexpensive, with a base price beginning at $25,000 and has been touted as safe, flexible, and easily adaptable, with vision and touch sensors that allow it to adapt to a variety of situations, like when a part is dropped or is missing. Rather than traditional programming, the robot is manually “trainable” by internal staff and can be moved around and retrained to perform a variety of assembly and other production tasks.
Doyle says even the more traditional robotics manufacturers are introducing collaborative robots, like ABB, Kuka, Yaskawa Motoman and Fanuc.
But how is the integration of more robots into manufacturing environments impacting the number of jobs in the industry? RIA charts industrial robotics sales versus the unemployment rate versus the number of employees in manufacturing in the U.S. and has found no observable relationship between the three.
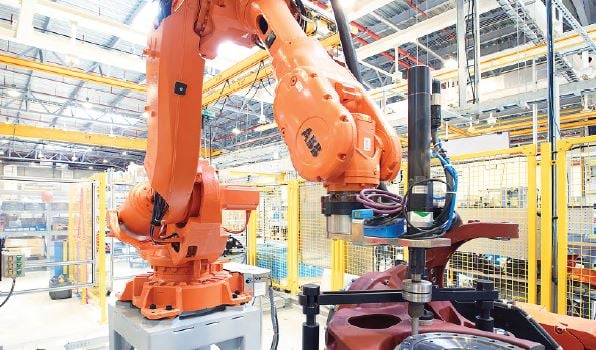
“People are buying more robots than ever and the unemployment rate keeps going down,” he said. “We firmly believe that the use of robotics actually grows jobs and creates better jobs, higher-paying jobs—the types of jobs that require training and make employees happier.”
As evidence, RIA’s website—a3automate.org—features a series of videos called “Why Automate,” highlighting small-to-medium-sized manufacturers that are thriving after introducing more automation and robotics into their plants.
Even so, Sirkin says there are still some manufacturing sectors that are not able to integrate robotics into their plant operations at this time, due to the nature of their business or the type of products they manufacture.
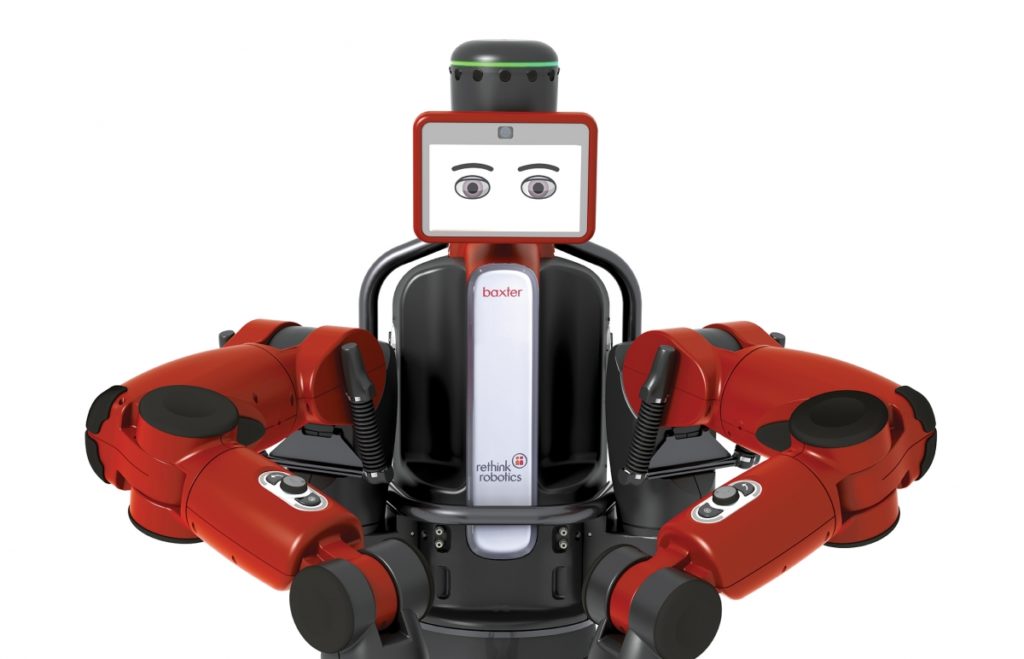
“There are some things that robots do better than humans, and there are some things that robots don’t do better, and so you have to make the distinction very clearly,” he said. “We have some real problems in the apparel area when we try to use robotics. As humans, we’ve learned how to pick up one very fine piece of cloth or denim, but it’s very hard to train robots to do this—they do not yet have the technology to perform that same tactile skill that humans do. This is holding back advances in robotics for the apparel industry.”
But, both Sirkin and Doyle agree it’s just a matter of time before issues likes these are overcome by innovators in the industry.
“I think the technology will continue to evolve,” said Doyle. “These collaborative-type robots that are designed to make manufacturing more efficient in electronics and other similar industries will continue to grow. We’re very bullish on the market. We see it continuing to grow as more and more manufacturers realize the benefits of robotics and automation. I think the technology will continue to improve and the prices of sensing technology will continue to go down, which allows more and more manufacturers to purchase automation systems. We see a really bright outlook for robotics and automation.”
- Category:
- GrayWay
- Manufacturing
Some opinions expressed in this article may be those of a contributing author and not necessarily Gray.
Related News & Insights
Manufacturing
To Print or Not to Print: Leading 3D Printing Expert Offers Practical Advice for Manufacturers
GrayWay
Manufacturing
The New Face of Manufacturing: A Q&A with Marlin Steel’s Nathan Myers
GrayWay
Manufacturing
Google Is Shopping for Robots in New Manufacturing Venture
Industry
March 14, 2014