Working Together: Integrating a Top-Line Food Safety and Quality Program Company-Wide
Modern food and beverage facilities around the world are integrating new technology to improve operations, but also provide new levels of safety and quality in their finished products. Food and beverage producers are introducing highly automated and innovative systems into their facilities for preparing and packaging foods, and distributing products to consumers.
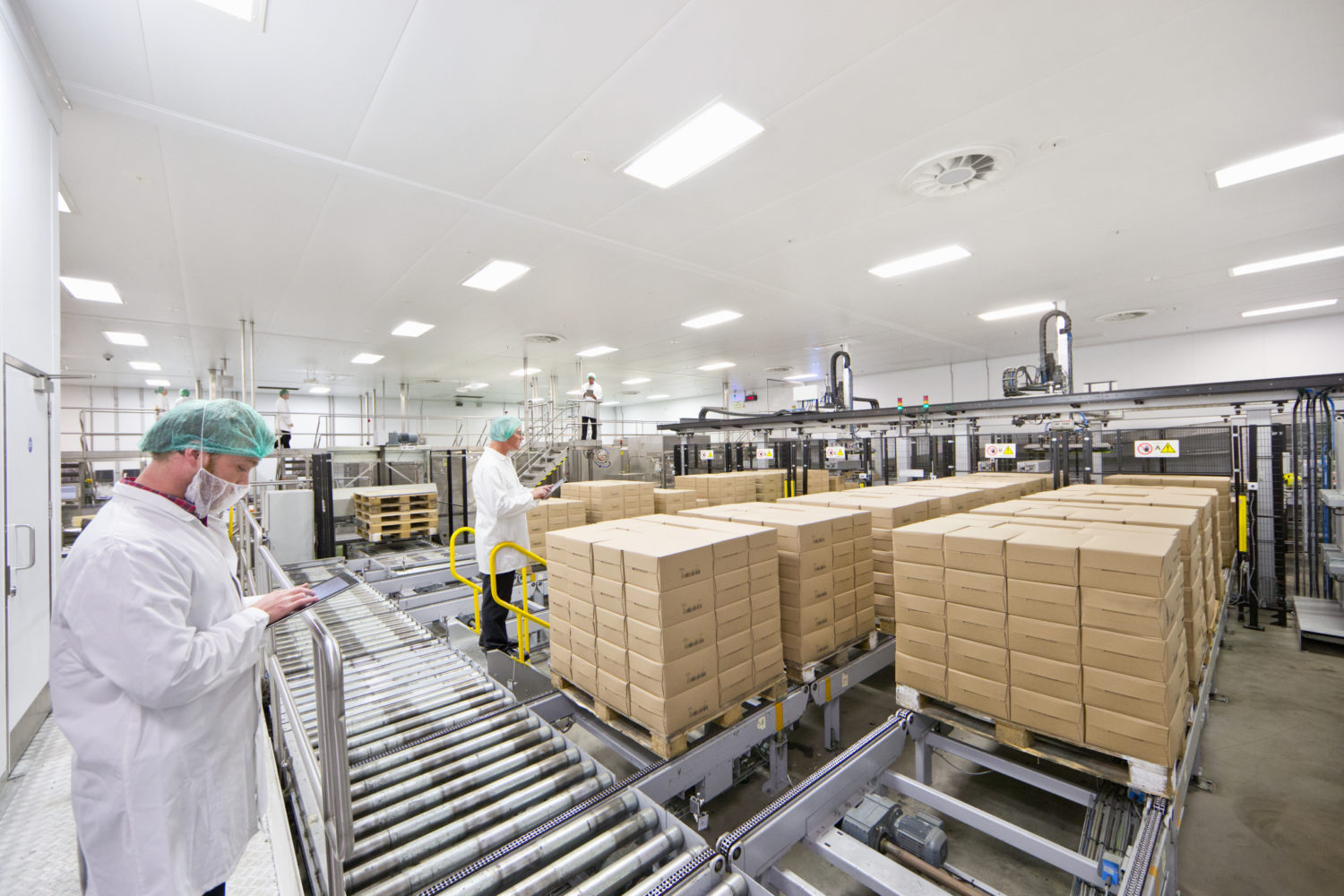
Walker Mattox is founder of Crow Street, a company that works with businesses to provide integrated technology solutions. He says it’s important to establish a clear foundation for communication and standardization at the beginning of each project.
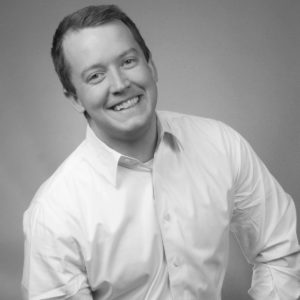
“Once technical standards have been set, the appropriate technology solutions can be brought together to create maximum flexibility,” said Mattox. “Developing an adaptable framework is the core foundation of any future ready project.”
A typical food and beverage plant will feature a variety of food processing equipment supplied by a number of vendors. While it’s important to select just the right piece of equipment for each step in the manufacturing process, incorporating equipment from a variety of vendors can present a unique challenge when it comes to successful integration of a food safety and quality program.
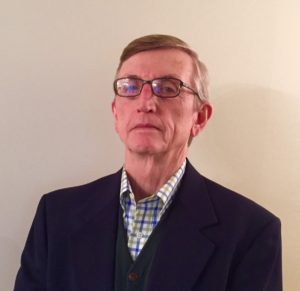
Lou Rives is president of VersaTech Automation, a company that specializes in integrating process controls for industrial customers. In this capacity, VersaTech ensures that the control systems of each piece of equipment in a food and beverage plant coordinates with the rest.
“In a given plant, there might be a dozen different pieces of equipment supplied by unique vendors,” said Rives. “We establish a standard platform across equipment lines so they speak the same language. This makes it much easier and more efficient to gather important data used in food safety and quality efforts.”
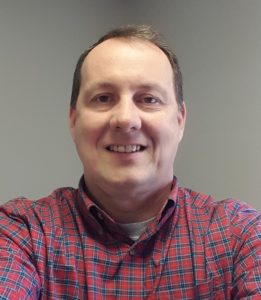
On a recent project for an international pet food company, Mattox and Rives worked with Gray Construction to set a standard using Rockwell Automation—the largest controls vendor in North America—to help integrate equipment and create a common controls platform. This allowed vendors and OEMs to operate in their own space but provided commonality to deliver an integrated platform. Consultant Dan Heatherly, who works with Rives, helped the company use Rockwell’s Vantage Point software to ensure access to data from multiple vendors, whether in the database or a process on the plant floor.
But what does that mean for food safety and quality? Heatherly says it all comes down to traceability.
“At one time, I was working for a tire manufacturer who, before this kind of technology was available, was not able to isolate information when quality of the rubber was compromised,” explained Heatherly. “They would have to get rid of 40,000 tires—or two days of production—because they couldn’t tell at what point in the production process the rubber was compromised. Once they implemented paper barcode tracking of each individual item, when they had a bad batch of rubber, they could isolate a certain number of tires and just get rid of those.”
“You see that same sort of thing in the food industry where at least in a lot of cases, you know the ingredients that went into a product, so when there’s a recall, you can narrow down which product it is, and then how to segregate it and make sure it’s safe.”
While food and beverage companies have been mining this data for some time now, the speed and efficiency at which they can do so has changed dramatically over the last decade or so.
“We’re seeing a demand for highly integrated and coordinated systems today,” said Mattox. “Companies want to be able to access metrics and traceability data from current production runs, and historical ones. Creating common data points allows financial and operational systems to have access to near-real-time information.”
It’s not just data from processing equipment that impacts food safety and quality that companies are analyzing. They can now extract data from the environment of a plant to identify problem areas.
“If a particular temperature has to be met in order to maintain quality, manufacturers need to be able to see that information to verify the temperature, for example,” said Rives.
A highly sophisticated controls system can track data virtually in real-time and offers other benefits beyond maintaining food quality and safety.
“Companies can now also track the status of their equipment,” explained Rives. “Every day, they can look back and see how they are utilizing production lines. Are they only utilizing a piece of equipment 50 percent of the time? Could this piece of equipment be utilized more often? From a future investment standpoint, they can make better decisions about investment in new equipment.”
- Category:
- GrayWay
- Food & Beverage
- Manufacturing
Some opinions expressed in this article may be those of a contributing author and not necessarily Gray.
Related News & Insights
Food & Beverage
4 Benefits of Virtual Reality to Food and Beverage Processing
Industry
Food & Beverage
How Data Collection, Analysis and Automation are Improving Food Safety and Quality in the U.S.
GrayWay
Food & Beverage
How Equipment Investments by Two U.S. Food & Beverage Producers are Paying Off
GrayWay, Industry