Why Consistent Near Miss Reporting is Crucial to Any Good Safety System
Drones flying into restricted airspace present a growing danger. The Federal Aviation Administration (FAA) announced on August 12 that there had been more than 650 pilot sightings of drones in the first half of 2015, compared to 238 during the previous year.
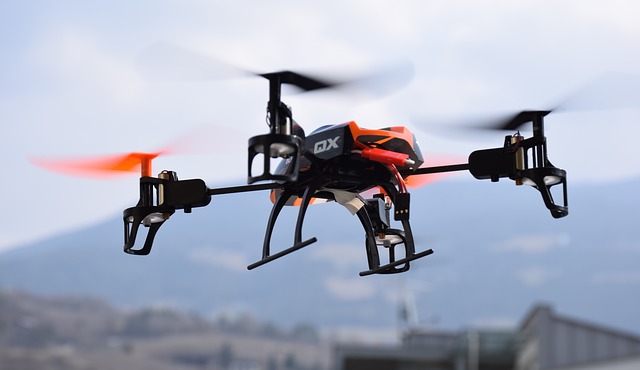
If you see a drone fly past your airplane window, do you want the pilot, flight crew, and other passengers to just shrug off the incident? I don’t think so. You want a near miss report filed, followed by an investigation.
In your company’s facilities, there are near misses too. Yet, near miss reporting at work, for many reasons, is often skipped. After all—nobody was hurt. But if your safety system doesn’t recognize the importance of these events, you’re running the risk of the next occurrence being a hit rather than a miss.
When near misses are not reported, prevention opportunities are lost. Just like a good quality system, a safety system is the foundation of eliminating problems and the key to becoming a stronger manufacturer. Consistent near miss reporting is at the heart of any good safety system.
What are the typical reasons (or excuses) for not reporting near misses?
When reporting systems are time-consuming or confusing, people don’t want to bother reporting something that didn’t actually happen. Likewise, when an employee who reports a near miss is blamed or humiliated, others are more likely to not report near misses. No one readily volunteers to being treated badly.
In addition, the leadership reactions can affect the likelihood of near miss reporting by employees. If it appears that leadership isn’t concerned, not only will it seem pointless to make reports, employees may feel that management doesn’t care about them, which affects morale. Management may also suppress near miss reporting to hide problems from insurers, OSHA, or the press.
How can organizations increase the likelihood of near miss reporting?
To improve the chances of employees reporting near misses, leaders must value information about mistakes or malfunctions and be clear that they do. They must establish a culture of reporting where every near miss report is an opportunity to identify hazards and eliminate them. Everyone needs to be involved in making facilities safer. They need to investigate incidents, find root causes, keep good data and analyze it for patterns.
In the case of drones, pilots are trained to report sightings and the FAA does keep detailed records. The data reveals a different root cause than most people may assume. In fact, the Academy of Model Aeronautics (AMA) found that reckless hobbyists are not flying hundreds of dangerous drones near airplanes. When the AMA dug deeper into the FAA reports, they discovered that only 27 of the 700 were actual close calls with actual stray drones. A significant number of them were flown by the military, organizations like the police, wildfire fighters and commercial operators. Many sightings were drones flying well below the allowed maximum altitude. And many were not drones at all. They were balloons, model rockets and birds.
Similarly, analyzing manufacturing safety records usually reveals that it’s not careless employees at fault. The National Safety Council says that a faulty process or management system is “invariably” the root cause of a near miss.
People are the key to the solution, however. The FAA and AMA are educating drone operators with the new Know Before You Fly campaign. Manufacturing leaders also need to establish a climate of education and communication about safety at work. Pilot reporting allows the FAA to collect detailed data, which the AMA is able to use for good root cause analysis. Manufacturing safety reporting and response policies should be written, explicit, reviewed regularly and updated periodically. Regular safety talks remind everyone of the rules and reasons behind them. Open discussion of near misses, as well as accidents, are opportunities for learning and continuous improvement.
Near misses, whether drones or flying machine parts in the plant, are not to be taken lightly. Understanding and correcting root causes is a serious business.
Karen Wilhelm has worked in the manufacturing industry for 25 years, and blogs at Lean Reflections, which has been named as one of the top ten lean blogs on the web.
- Category:
- Industry
- Manufacturing
Some opinions expressed in this article may be those of a contributing author and not necessarily Gray.
Related News & Insights
Manufacturing
How Drones, VR and BIM are Improving Construction Jobsite Safety
Industry
Advanced Technology
The Opportunities and Challenges of a Second Trump Presidency
Opinion
Advanced Technology, Automation & Controls
Four Use Cases for AI's Growing Role in Manufacturing
Industry
November 25, 2024