What the Digital Thread Means for the Future of Design and Manufacturing
The Digital Thread – it’s a concept that sums up several lines of advancing manufacturing technology that have been tough to integrate. The potential of the digital thread is to unite product concepts, three dimensional (3D) modeling, parts libraries, simulation, verification and testing, and then computer controlled manufacturing and inspection.
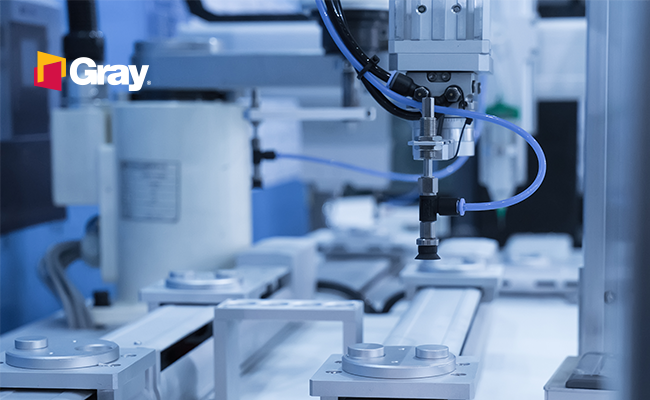
Today manufacturers struggle with disconnected pieces of digital design-to-production processes. They may still be converting 2D CAD drawings to 3D models. Their 3D CAD software isn’t always compatible with that of suppliers and customers. Then, depending on how the designed part is to be manufactured, the files must be converted again to G-Code for CNC machining or fabricating, to STL files for 3D printing, or to something else. Then there’s the problem of incompatibility with inspection tools that can automatically compare the actual part being made to what was intended in the design. These transitions are currently being made with file conversion methods that take a lot of human effort to troubleshoot.
Making the path from design to finished product seamless would result in giant steps in productivity and quality. That ideal is now coming into view with emerging technologies which would electronically connect standardized design data, manufacturing process plans, and other information as it moves through the product lifecycle. Collaborative projects and test beds for making the digital thread a reality have been springing up.
Here are a few examples:
- Smart Manufacturing Systems (SMS) Test Bed
The SMS Test Bed* is a new project at the National Institute of Standards and Technology (NIST) facilities in Gaithersburg, Maryland. It includes a laboratory to develop new ideas about the digital thread and a model factory to test them out. The SMS Test Bed will provide online data streaming, collection, storage and publication services, as well as the ability to use full manufacturing data packages for model products that have been built there. The model factory will include digitally driven CNC machine tools, inspection devices, and other equipment to facilitate the transition from research to realization. Participating manufacturers will be able to experiment with developing digital manufacturing process technologies before introducing them in their companies.
- International Organization for Standardization (ISO)
Standards form the foundation for interoperability of manufacturing systems and data. Since 1984, committees of the ISO members have been working to integrate varied formats for manufacturing design data that have emerged over the years. The latest of these standards, ISO 10303-242 (aka STEP AP 242), is for adding computer-readable product and manufacturing information (PMI) to 3D models. That can include material specifications, precise geometric dimensions, desired surface texture, finishing requirements, and process information.
- Design to Manufacturing and Inspection Project
Making use of this new version of STEP is another venture from NIST, the Design to Manufacturing and Inspection Project.In it, for example, Rockwell Collins will create enriched 3D designs of parts using its CAD system, then convert them to a STEP AP 242 format. Suppliers involved in the testing like Geater Machining and Manufacturing will import the standardized data into manufacturing software to create CNC instructions for machines that make the parts. At the same time, that STEP AP 242 model will drive the coordinate measuring machines that will inspect the parts to confirm that they match the original specs.
In mainstream manufacturing today, some segments of the digital thread are already connected. What remains is to spin them into a complete end-to-end thread that would run through the entire manufacturing value stream. These experiments, test beds, and evolving standards are just a few steps toward understanding the digital thread’s many implications for the future. It’s coming fast, so manufacturers have to keep up with the change in order to be competitive.
*Collaborators in the SMS Test Bed project include the Association for Manufacturing Technology (AMT); DP Technology Corp.; Mazak Corp.; Mitutoyo America Corp; the MTConnect Institute; and System Insights Inc.; Rensselaer Polytechnic Institute; Virginia Tech, the Commonwealth Center for Advanced Manufacturing (CCAM) in Virginia; the Digital Manufacturing & Design Innovation Institute (DMDII)
**Collaborators in the NIST-led Design to Manufacturing and Inspection Project include International TechneGroup Incorporated (ITI); Advanced Collaboration Consulting Resources; Rockwell Collins; and Geater Machining and Manufacturing; CNC Software; Mitutoyo America; and CoreTechnologie.
Karen Wilhelm has worked in the manufacturing industry for 25 years, and blogs at Lean Reflections, which has been named as one of the top ten lean blogs on the Web.
- Category:
- Industry
- Manufacturing
Some opinions expressed in this article may be those of a contributing author and not necessarily Gray.
Related News & Insights
Manufacturing
How Disruptive Digital Technology is Rebooting the Economics of Manufacturing
Industry
Manufacturing in the Digital World: Identifying & Mitigating Cyber Risks
GrayWay, Industry
July 30, 2014Food & Beverage
How Advanced Technologies and Robotics are Shaping the Future of Manufacturing
Industry