Top 5 Trends Redefining Manufacturing in 2019
New developments predict growth amid ongoing changes
Manufacturing once again remained a hot topic in 2018 with a lot of reasons for optimism going into 2019. Specific areas have emerged to reveal the top 5 trends impacting manufacturing for 2019.
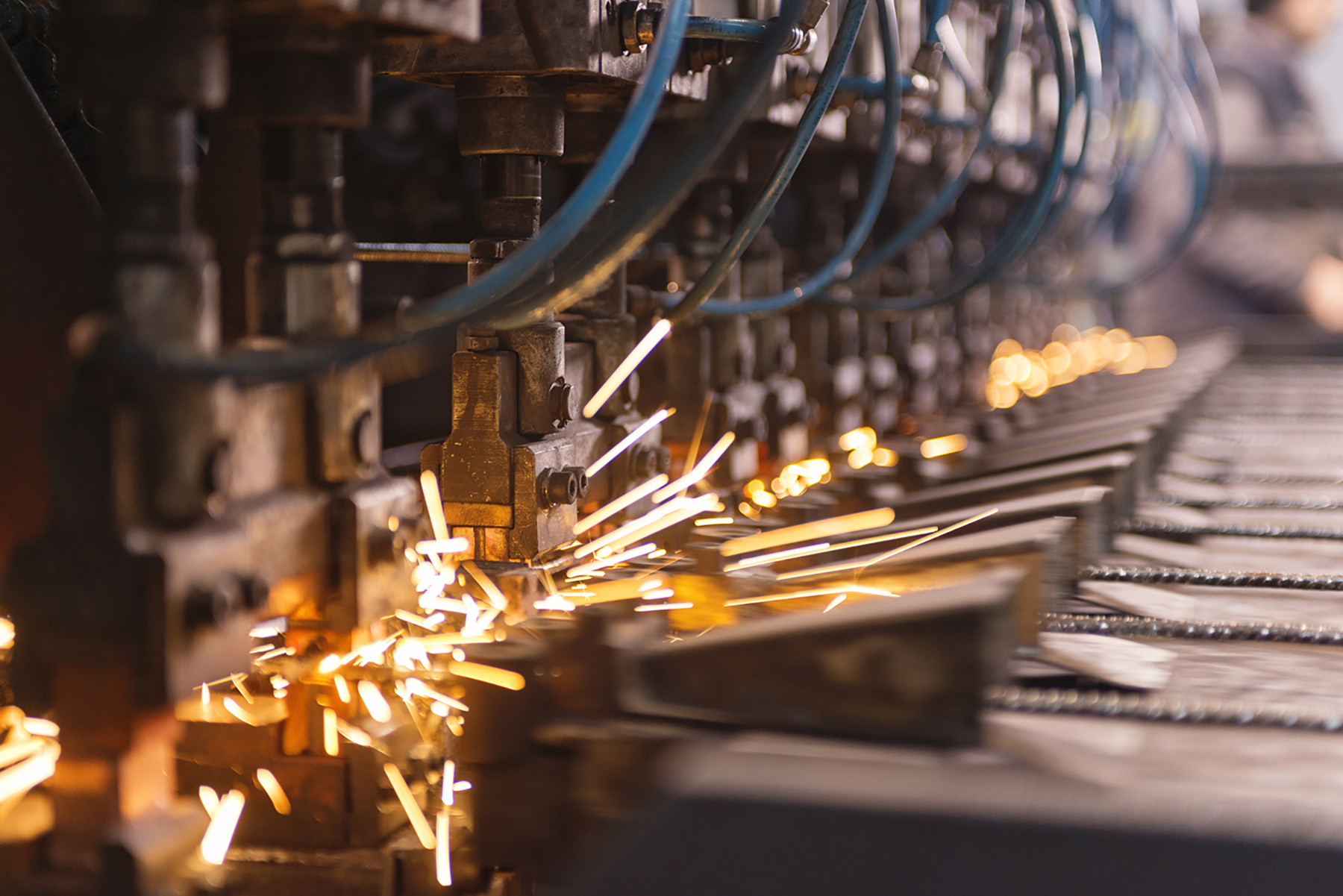
Projections Predict Growth
Manufacturing in the U.S. is successfully adapting to changes in customer needs and related shifts in the consumer marketplace, while still focusing on profit margins and revenue growth. Production in the U.S. is estimated to grow 2.8 percent from 2018-2021 (a faster increase than other segments of the general economy), and manufacturing continues to have an outsized influence on regional economies. Longstanding economic analysis has posited for every dollar invested in manufacturing, the result is $1.40 in additional economic activity.
This growth trajectory outlook is not without a few lingering questions. For instance, as a result of the projected growth of manufacturing, the need for skilled workers in areas like metal forming, fabricating, welding and finishing has also risen. Welding alone will need an estimated 90,000 welders around the country by 2024. A National Association of Manufacturers report highlights how many organizations are successfully partnering with community colleges and high school career programs to build a pipeline of future skilled workers. Other companies like GM are embracing new technologies and working to attract young engineers focusing on digital services.
Automation Also Advancing
It’s long been held that industrial automation is a job killer, but in reality it’s quite the opposite, according to Jeff Burnstein, president of the Association for Advancing Automation (A3). “Hysterical stories keep being printed in the media, but the robot we see doesn’t match the idea of robots being a job killer,” said Burnstein. “If it were true, then if robot sales were to rise, you’d expect unemployment to rise. We looked at a 20-year period of manufacturing jobs and overall employment in the U.S., and every time robot sales rose, unemployment fell. Every time robot sales fell, unemployment rose.”
In the past seven years 137,000 robots were delivered in the U.S., he continued. “Publicly available studies tell us that as robot use accelerates manufacturing jobs will decline, but guess what? Nearly 900,000 new manufacturing jobs were created during that period. That doesn’t sound like a job killer.”
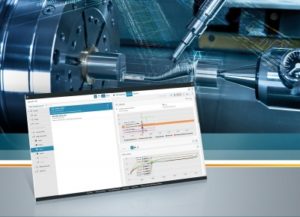
A3 approached customers like General Motors (GM), who despite investing heavily into industrial robots, added 25,000 more staff, he added. Amazon was also approached, having added 40,000 industrial robot units to their fleet, along with 100,000 new humans.
“The significant issue we should be worried about may be labor shortages, as manufacturers struggle to find skilled replacements for retiring baby boomers who are technologically savvy enough for modern machinery and automation. We have examples of companies who have invested in automation to solve the problem of dull, dirty and dangerous jobs, lowered their costs, won new business they wouldn’t have otherwise and since they’ve automated, they’ve hired more people,” Burnstein said.
New Methods of Production
Revolutionary new methods of making things will continue to advance in 2019. Call it 3D printing, additive manufacturing or rapid prototyping, there is no denying such “additive” technologies (compared to conventional milling, turning or other “subtractive” chipmaking) are coming on strong.
“The automotive industry has been using 3D printing since its infancy,” confirms Brandy Badami, business development manager at Roush, a leading automotive supplier. “Automotive OEM’s are truly embracing additive manufacturing more than we think. Although 3D printing is not yet suitable for their high-volume demands, they are constantly pushing the limits of the technology, allowing them to propel on innovation. Using 3D printing, engineers can design, print and test components designed with one of their biggest challenges in mind: weight reduction. This allows for quick-turn creativity that can provide a competitive edge with first-to-market product.”
More Computing Power and AI Connectivity
In addition to new methods of production, machine tools are exhibiting ever-growing levels of computerized operation and control. Not only does this result in increased precision and faster production, the volumes of data they create can be saved, uploaded to cloud computing centers and used to model even more efficient production processes.
Industry standards, such as MTConnect, are making such advances possible. Basically, MTConnect is an open, extensible, royalty-free standard – a communications protocol designed specifically for the shopfloor environment. By interfacing with different machine tools, cutting tools or any piece of equipment or data source, software applications can be built on MTConnect standard for the efficient gathering, reporting and use of a shop’s data.
With powerful computerized machine tools, the more industry keeps driving the standardization of shopfloor data, the simpler and more efficient a shop’s business becomes. Hours of setup and test cuttings could become a thing of the less efficient past.
Changing Attitudes
By 2025, up to 2 million manufacturing jobs are projected to be unfilled. Rather than continue to bemoan the problem, manufacturers are taking a multi-faceted approach to bridge the gap—not only for next year but also for 15 years down the road.
For example, Rockwell Automation is reaching out beyond millennials in a partnership with First Robotics supporting First Lego League programs for kids in grades four through eight. Some of those kids end up working at the company down the road. Over the past five years, Rockwell Automation’s interns have included young people with First Lego League experience.
“That’s very exciting to see, and it’s helping build our future pipeline of talent that’s coming in,” said a company spokesperson. “We view it as a recruiting tool. We view the students as they’ve got both the technical and the soft skills that we’re looking for that they gain from this experience. It’s more than just the robot.”
Disruption is a hallmark of all these manufacturing changes on tap for 2019: disruption in production methods, disruption in automation and collecting data and disruption in attitudes about manufacturing. Expect sharper clarity and further efficiency improvements as a result.
Some opinions expressed in this article may be those of a contributing author and not necessarily Gray.