The New Face of Manufacturing: How APSCO is Addressing the Skills Gap in Oklahoma
It is no secret that manufacturing is suffering from a skills gap issue, making it difficult to find people with the right skills to fill vital roles at companies across the U.S. This can hit small-to-medium manufacturers—who are trying to do more with less resources—particularly hard. But manufacturers are inherently problem-solvers, and many are tackling this issue head-on.
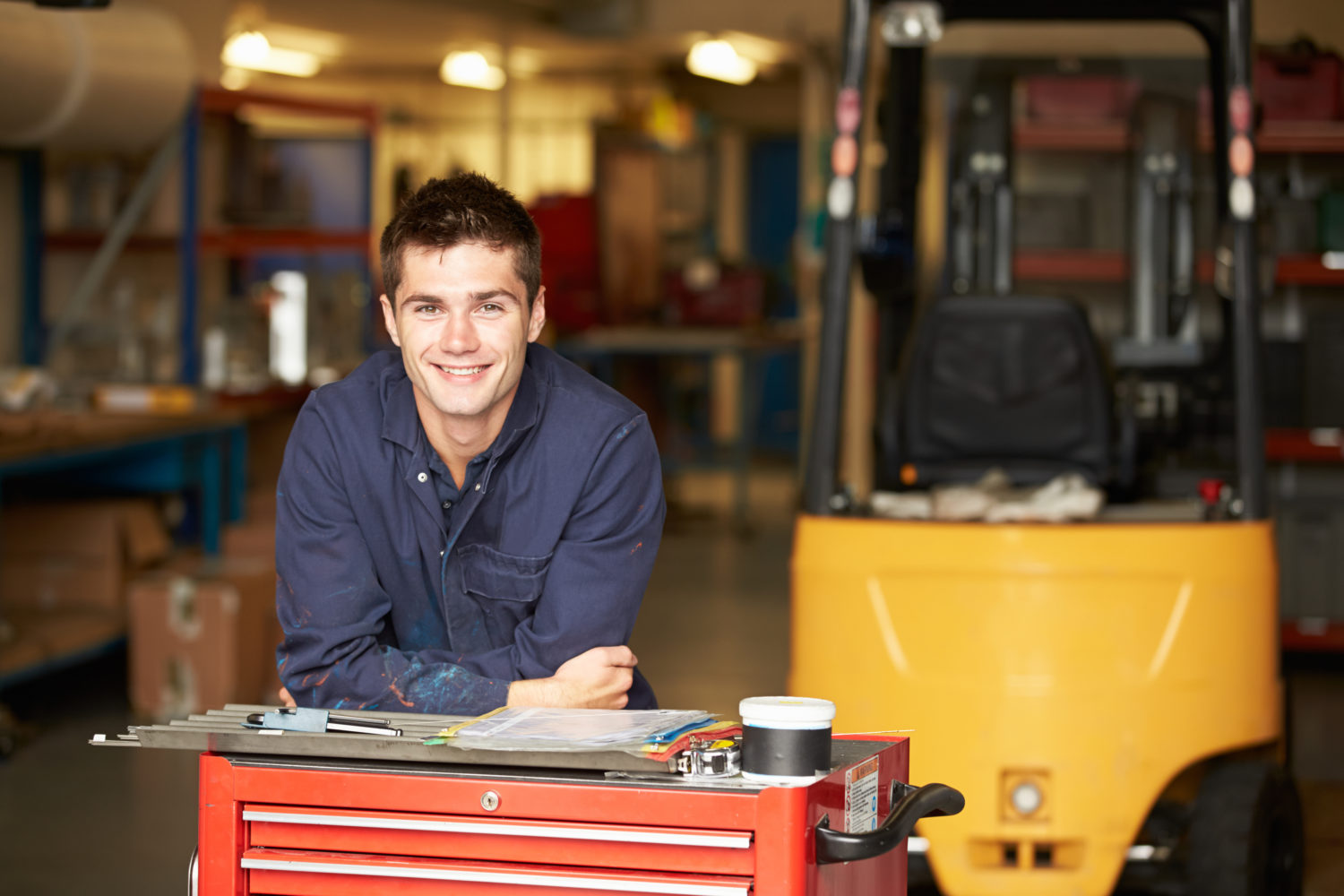
APSCO—an automotive parts manufacturer based in Tulsa, Oklahoma that employs some 80 people—is doing just that. Recognizing a shortage of talent available locally, the company created an internship program that not only helps to fill jobs within their own company, but within other area manufacturers as well.
Students from local high schools are introduced to the company’s internship program at the beginning of the fall semester. Interested students interview, and several dozen are chosen to train toward becoming certified production technicians.
Upon completion of the program, ASPCO hires at least two of these interns, and the remainder are hired by other partner companies in Tulsa.
“It benefits our company greatly to have relationships with the schools, and, likewise, for the schools to have relationships with area manufacturers,” said Stephanie Cameron, community affairs director for APSCO. “Being active in the community brings more awareness to not only our company, but to the manufacturing industry overall.”
- Category:
- GrayWay
- Food & Beverage
- Manufacturing
Some opinions expressed in this article may be those of a contributing author and not necessarily Gray.
Related News & Insights
Manufacturing
Manufacturers Must Take the Lead in Bridging the Skills Gap
Opinion
February 26, 2015Manufacturing
Great Expectations: Attracting Millennials to Careers in Manufacturing
GrayWay
Manufacturing
These Workforce Development Programs are Tackling the Manufacturing Skills Gap Head-on
Industry