The Benefits of Data Collection in Equipment Manufacturing
Increasing demand for smarter facilities and evolving customer needs are steering equipment manufacturers to incorporate more data into their equipment design and fabrication processes. This shift has led to increased productivity for equipment manufacturers and produced a host of benefits for end-users.
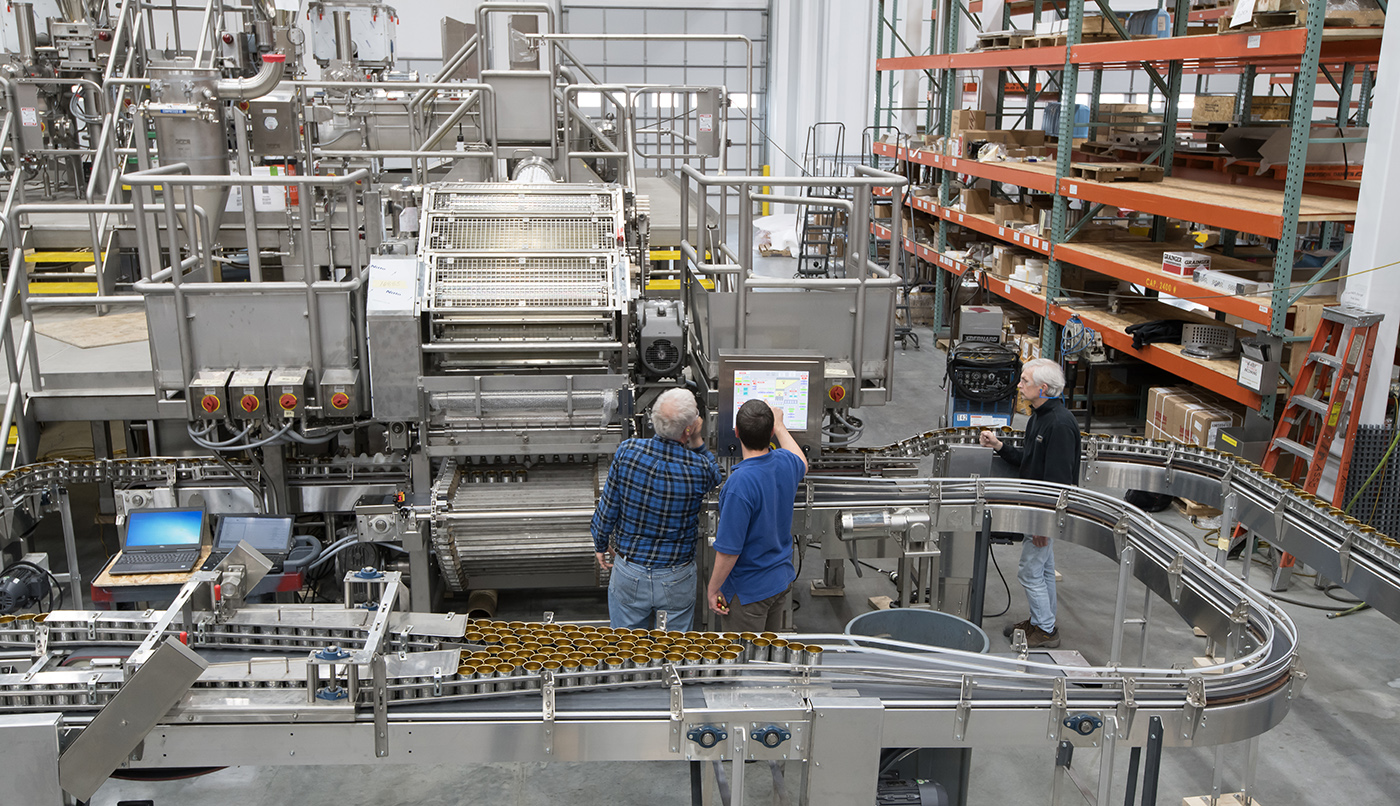
“Manufacturers have adapted—rather than depending on visual confirmation of system parameters, we’re increasingly integrating data from multiple source points,” says Thomas DeBoom, director of engineering at Anderson Dahlen Inc., a Gray company. DeBoom, whose background is in food process engineering and project engineering, sees data improving manufacturers’ precision.
“We’ve evolved from the art of visual interpretation of system conditions to an exponentially broader and data-driven view,” he says.
DeBoom partners with end-users to ensure new data instrumentation is expertly integrated into equipment to produce high-quality data with safe materials and applications.
Such instrumentation in equipment has significantly changed how data is collected and used for modern manufacturing facilities. For instance, load cells and flow metering provide flow control with weight intelligence, reducing cycle times by sensing exactly when a batch has emptied out of a mixer, DeBoom explains. Incorporation of data points also carries implications for product quality and safety. “Source points like precise position indicators on mix-proof valves can verify that cleaning fluids haven’t cross-contaminated the production stream,” he adds.
This collected data serves various primary uses such as system performance reporting, condition monitoring, predictive and preventive maintenance notifications, quality control analysis, production traceability and flexibility, and more.
The integration of data collection offers tangible benefits for manufacturers and end-users. One such example is large manufacturers’ need to precisely match product characteristics when operations are spread across different systems and facilities. “It is rare in the food industry to have two systems that are built with identical equipment and controls,” says DeBoom. “This presents challenges to simple copying of setpoints. Process data collection provides information to ensure critical parameters are applied across all transformations, no matter where or when they’re employed.”
Responding to Customer Needs
Compared with five years ago, DeBoom says the approach to data collection in equipment manufacturing has undergone significant changes, driven by the evolving needs of end-users. This has necessitated closer attention from suppliers and engineering system designers to align with manufacturing requirements. The pandemic further accelerated collaboration, revealing a greater need for remote access and information sharing from data sources.
Over the past decade, technological advancements have expanded the role of data in equipment manufacturing and project engineering. Notably, advancements in physical equipment design and critical information gathering have enabled equipment manufacturers to maximize capacity and minimize material and product waste.
“For years, suppliers have used data in packaging equipment to optimize the speed and yield of their product offerings,” DeBoom says. “With higher precision, machine tolerance, and smart capability, process equipment manufacturing can do the same.”
Just as mix-proof valves can process more dairy products with far less equipment, smaller, smarter controlled systems can improve process transformations using smaller vessels to increase capacity. This increase is enabled by advancements in physical process equipment design as well as critical information gathering and system software.
“Real-time monitoring and control of physical processes requires well-placed data gathering sensors. Automated inputs and the minimization or elimination of downstream upset conditions prevents high amounts of waste and unnecessary wait time and downtime,” says DeBoom.
Enabling Industry 4.0 and IoT integrations
The use of data in equipment manufacturing aligns with broader industry trends such as Industry 4.0 and the Internet of Things (IoT) by facilitating the creation of smarter systems and factories. Manufacturing and quality information systems with lower integration burdens can reduce the cost of Industry 4.0 opportunities.
“BIM (building information modeling) and project life cycle require a significant amount of data and have shifted from trends into fundamentals of project concepts, design, construction, and manufacturing operations,” he says.
Addressing Challenges
Adapting equipment to accommodate enhanced data collection capabilities has presented challenges related to network infrastructure and hardware costs—particularly with older facilities and equipment. Data collection also presents challenges with cybersecurity on the factory floor, as manufacturers must devote training and resources to protect intellectual property from hackers and ransomware.
However, these challenges can be offset by creative application of data in advanced technologies. “Data from laser scanning has completely changed how engineers design equipment and systems in 3D models, especially in retrofit situation,” DeBoom says. This has allowed for step-change reductions in design time, improved precision in fabrication, and prefabrication in even highly customized systems, notes DeBoom, adding that this lowers costs, improves quality, and shortens time to completion.
Simplifying the Worksite and Mitigating Hazards
Perhaps the most significant impact of advanced data collection is the improvement to safety. During project construction, prefabrication can remove a substantial amount of contracted labor from the worksite—especially the more hazardous work at elevation. “Prefab also lowers the intensity of the work, because when it arrives, it is typically fully engineered and fits into place better with lower associated rework.”
DeBoom adds that if a manufacturing system creates an upset condition that causes or could cause an injury, the system data collected can be analyzed and hazards mitigated with a much higher success rate than without data. “System monitoring can determine when something is operating out of specifications prior to a failure. When monitored and acted on, these insights from data can prevent safety incidents and reduce the prevalence of future hazards,” he says.
Looking Ahead
“Data collection and the application of new tools in the hands of talented people continues to smash the old paradigm that between cost, schedule, and quality, you can only have two,” says DeBoom. “All three are possible.
As the swelling tide of data collection continues to shape the industry, further technological refinements in equipment design and fabrication will lead to smarter systems and factories that set even higher standards for safety, productivity, and sustainability.
- Category:
- Industry
- Specialty Equipment
- Manufacturing
Some opinions expressed in this article may be those of a contributing author and not necessarily Gray.
Related News & Insights
Manufacturing
Reverse, Revive, & Reshape: What Trump's Economic & Trade Policies Mean for Key U.S. Industries
Industry, Opinion
Advanced Technology
The Opportunities and Challenges of a Second Trump Presidency
Opinion
Advanced Technology, Automation & Controls
Four Use Cases for AI's Growing Role in Manufacturing
Industry
November 25, 2024