Technical Skills in Short Supply
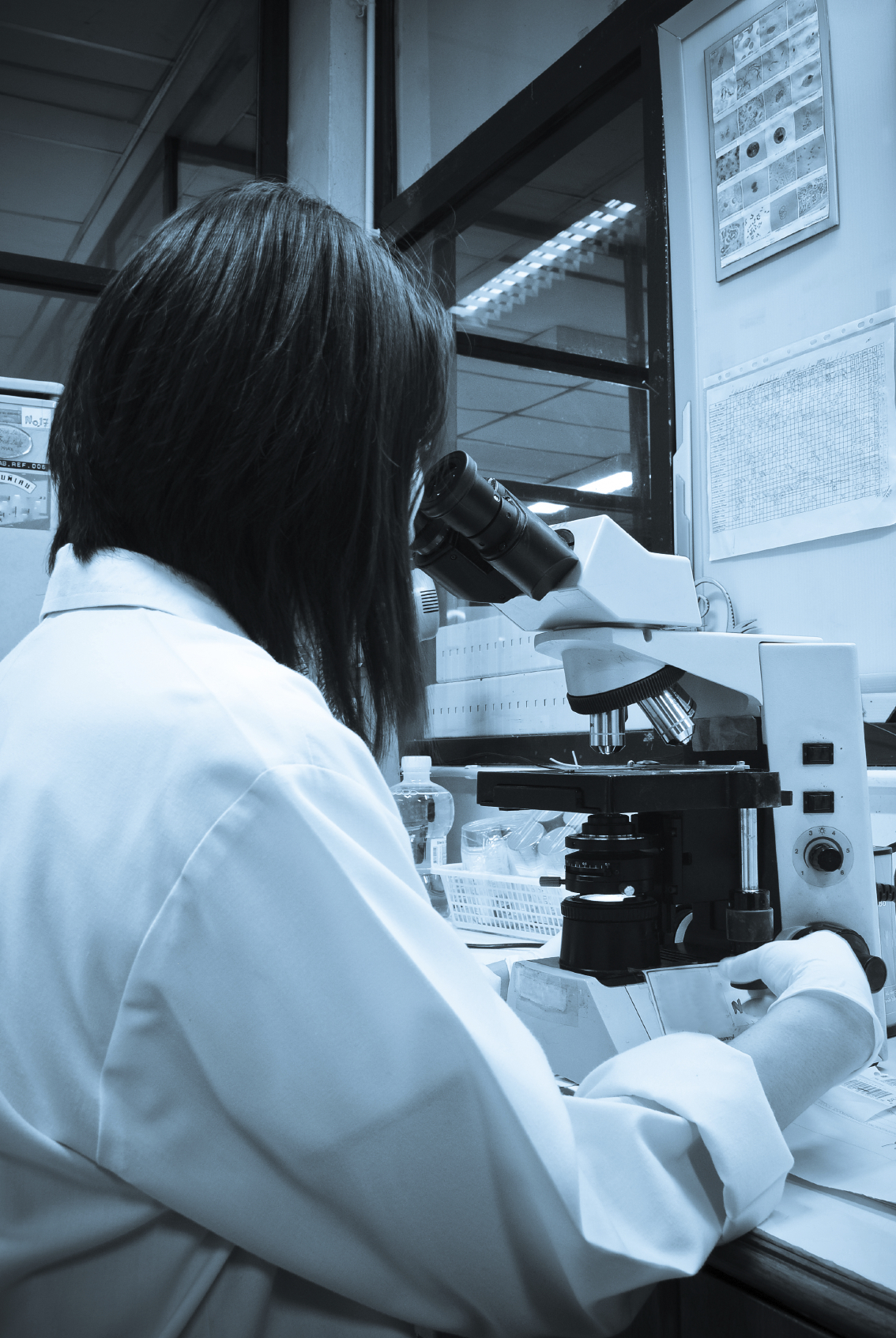
Finding the skilled people manufacturing companies need is surprisingly difficult, given the high unemployment rates we are experiencing. Hiring managers say there are a lot of people out there, just not the right people.
This is a global problem. The 2012 annual Manpower Talent Shortage Survey of 40,000 employers in 41 countries found that an average of 34% of them are having trouble filling open positions. In just about every part of the world, skilled trades and engineering positions are the toughest to fill. Even in China, almost a quarter of employers are having trouble finding technicians, engineers, skilled trades workers, and production operators.
With so many people looking for work, there must be some reason why there are not enough candidates for manufacturing jobs. When employers in the Manpower study reported on what they felt was lacking in the pool of available people, they most often mentioned technical skills and competencies (33%), experience (24%), or an interest in the available jobs—sometimes there are few, if any, applicants (33%).
To continuously place the right people in the right jobs now and in the future, manufacturers need real talent management strategies. To feed that pool of job-ready candidates, a company must consistently prepare employees with training and development opportunities. (Only a quarter of employers reported doing that.) Besides gaining job-related skills, these employees are also learning how to learn. Because companies have to rapidly adapt to change, having a flexible workforce is a competitive advantage.
Another source of flexibility is to use contingent workers* who can step in when business peaks, but can be released if business drops off. A strategic contingent employment partner is not just a temp agency. It helps find people with the right qualities for the company and provides some of their training. To offset the uncertainty of their employment status, contingent workers are usually considered for permanent jobs that become available where they work.
Some companies surveyed by Manpower are partnering with educational institutions to define needs, develop curriculum, and provide financial support to both students and schools. Others offer internships to both secondary school and college students. Having a student intern gives the company a chance to find and recruit promising employees.
Apprenticeship programs have languished in many countries. Like internships, apprenticeships bring in the talent needed for the next generation of workers, but in a more long-term methodical way. The German Dual Vocational Training System provides one model, and through the U.N., Germany is helping other countries set up similar apprenticeship systems. Also spreading apprenticeship practices are German companies like Siemens, which offers them at their operations worldwide.
Education costs and fees, as well as government tuition assistance, vary dramatically in countries around the world. In the U.S., university costs have escalated, while assistance has not, putting the burden of investment on students and their families. In some other countries, university education is more accessible. Manufacturers can show more leadership in helping students and working with universities to make education more attainable.
To expand the talent pool, some companies are changing work, providing better childcare and other accommodations to tap women’s talents. And much is said about the aging workforce. As today’s workers join the ranks of active retirees, many continue to be interested in working. They possess deep manufacturing knowledge they could share, but they want shorter hours and more time off.
Manufacturing has changed, and it needs a different workforce than in the past. While that workforce is in short supply, manufacturers can do much more to develop talent and manage it strategically. Of course, people are not just “talent.” Treated with respect and supported with learning opportunities and new work options, they are the answer to the manufacturing workforce shortage.
—-
*Although ManpowerGroup provides this type of resource, the Talent Shortage Survey report did not play up the use of temporary workers as a solution.
Karen Wilhelm has worked in the manufacturing industry for 25 years. She publishes the blog, Lean Reflections, which has been named as one of the top ten lean blogs on the web.