Solutions to Global Challenges Drive 2023 Manufacturing Trends
Manufacturers in 2023 will still be focused on improving supply chain relationships and maximizing production, quality, efficiency, throughput, and speed to market, all while reducing costs. Major challenges to these goals include inflation, labor shortages, supply chain delays, cost pressures, and cyber attacks.
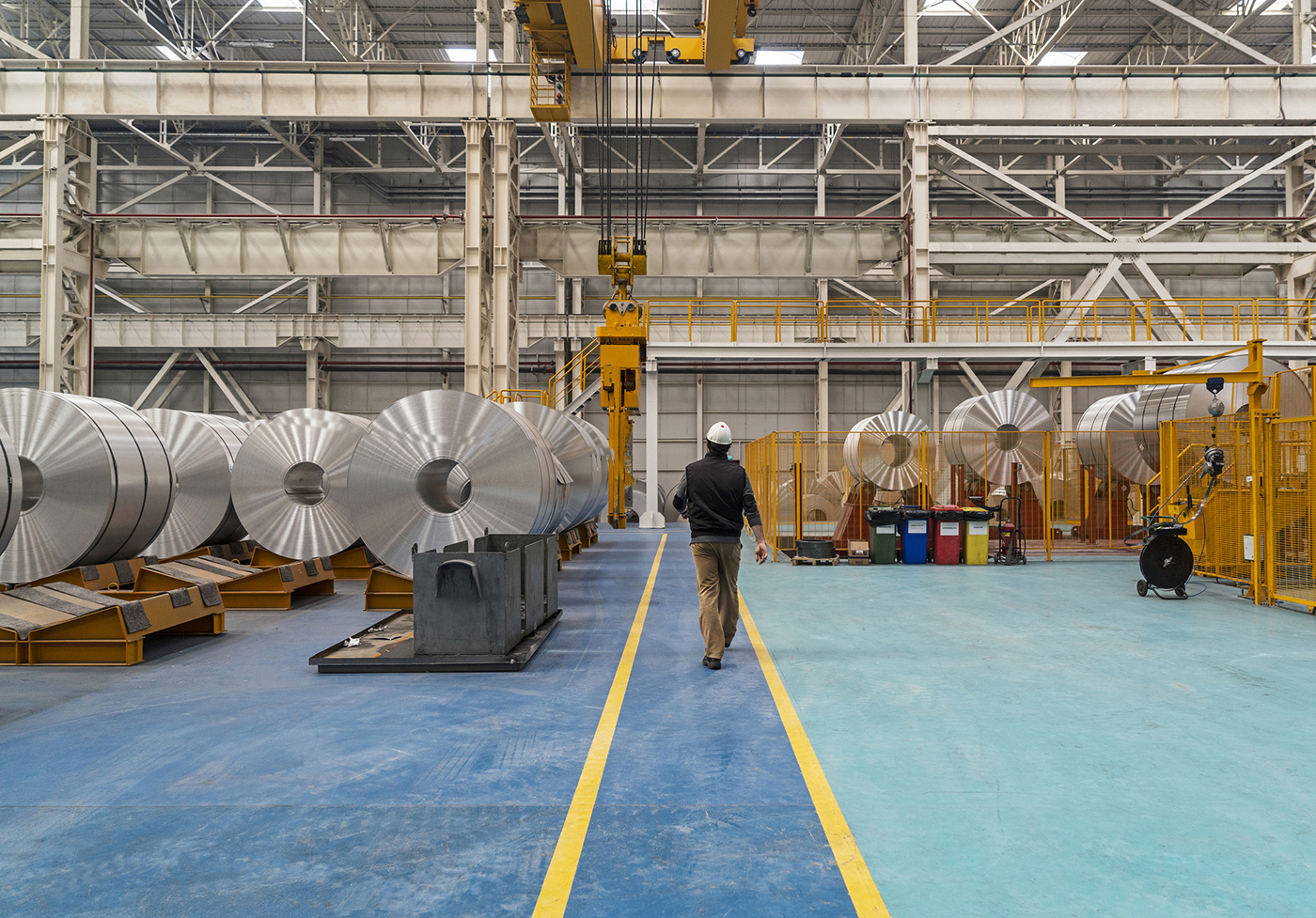
In this challenging business climate, the best way for manufacturers to win market share in a rapidly evolving industry is by embracing change. The value of being agile has never been more important, as demonstrated by how companies responded to the COVID-19 pandemic—especially dealing with supply chain disruptions and worker shortages.
Below are 12 top trends that will impact manufacturing companies in 2023.
1. Safety First.
It is still important for manufacturers to take COVID-19 precautions, including social distancing and sanitization practices on the production floor. Internet of Things (IoT) sensor technologies can also track worker movements to confirm safety protocols and identify potential safety issues, especially regarding workflow and facility layout. “With an increase in cobot applications, where robots work alongside humans with no physical safety barrier, manufacturers will need to implement new forward-thinking safety policies in support,” says Drew Goodall, vice president of process integration with Gray Solutions, a Gray company.
2. Connectivity Is Key.
Manufacturers are becoming more comfortable with investing in and implementing IoT solutions. According to MarketWatch, smart manufacturing (IoT) will grow at a rate of 12.7% through 2029. Further, MPI Group reports that 31% of production processes now utilize smart devices, sensors, and embedded intelligence to improve efficiency and reduce costs. “There is a transition happening within the manufacturing space,” says Goodall. “All new and most existing facilities are moving to wireless industrial networks, which will continue to support the rapid addition of transmitters to everything.”
Investing in more IoT also boosts quality and reduces risk. “Companies with higher digital maturity have shown greater resilience, as did those that accelerated digitalization during the pandemic,” states Paul Wellener, vice chair for U.S. industrial products and construction leader for Deloitte LLP. “Continued investments in advanced manufacturing technologies can help develop the required agility.”
3. Waste Not.
Manufacturers are working toward greater sustainability across their operations by reducing negative environmental impacts, conserving energy, reducing consumption of natural resources, and utilizing more renewable energy. “The rising cost of energy and its impact on the environment have made energy efficiency one of the primary objectives of Industry 4.0,” states IoT Times. Sustainability is also keenly important to customers and prospective customers.
4. An Ounce of Prevention.
Breakdown of critical equipment can cost hundreds of thousands of dollars in downtime and repairs. Total Predictive Maintenance (TPM) uses 24/7 sensor data and cloud-based analytics to track performance in real time and identify potential problems or defects in the manufacturing process, which can then be repaired immediately before they fail, saving money on labor, parts, and inventory. “Emulations of production systems also allow for virtual failure predictions to be completed in digital twin models,” says Goodall. “We can now see, virtually, when equipment might be strained to the point of requiring maintenance and use that data to support predictive maintenance in the real world.”
5. Man(ufacturing)’s Best Friend.
Robotic technology is advancing rapidly while costs continue to decline, especially the use of collaborative robots (cobots) that can work safely alongside humans. Artificial intelligence (AI)-enabled cobots can continuously refine how they perform their tasks by using optical systems and sensor data. “Automation, machine learning, and AI-powered digital transformation helps manufacturers to better predict future trends and improve quality governance, deliver products faster, lower costs, and reduce waste,” states Intech Systems.
Years ago, initial inceptions for robot and cobot applications were basic in nature; today, the integration of sensors and other advanced technologies such as artificial intelligence (AI) drive the scope and scale of robotic applications. “Advances in robot/cobot arm-end effector tools are allowing robots to complete ever-increasing complex tasks, where human hand dexterity or pressure control was previously required,” says Goodall.
6. Data Is Power.
Applications for big data continue to expand as sensor technologies connect more equipment on the manufacturing floor. “We can likely expect almost every surface to be transformed into a sensor for data collection in order to generate real-time insights for manufacturers,” states Hitachi Solutions. “The ability to collect data from a multiplicity of sources, combined with increasingly powerful cloud computing capabilities, makes it easier for manufacturers to re-evaluate their forecasting and planning models.” Goodall notes that manufacturers need to be thinking now about data overload and how to distill vast quantities of new information into actionable tasks.
7. Be Direct.
Increasingly, manufacturers realize the benefits of shipping their products directly to the consumer. With a robust e-commerce platform, a B2C model increases profits, reduces costs, improves brand awareness, accelerates time to market, and gathers more customer data, which helps identify consumer trends that can lead to more personalized products. “On-demand” manufacturing also uses fewer resources and requires less warehouse space. Emulations of production systems designs can allow virtual testing of sizing for small batch or custom production runs in support of more direct B2C manufacturing requirements.
8. Keeping the Talent Happy.
Deloitte indicates that mitigating labor market challenges will remain a top priority for manufacturers throughout 2023. “Despite a record level of new hires, job openings in the industry are still hovering near all-time highs,” states Wellener. “Additionally, voluntary separations continue to outnumber layoffs and discharges, indicating substantial workforce churn.” Such a prevailing workforce shortage, he notes, elevated by supply chain limitations, is reducing operational efficiency and margins. As a result, manufacturers need to be innovative in their talent retention strategies.
9. Reality Check.
Augmented reality (AR) adds digital components to a live view—for example, glasses or a smartphone screen that show a live-view of an assembly with instructions that appear on the glasses to assist the worker (digital component). Virtual reality (VR) immerses the worker in a complete digital simulation (ideal for training or practicing). “AR and VR also make it possible for technicians to provide remote assistance by sending customers AR- and VR-enabled devices and walking them through basic troubleshooting and repairs,” says Hitachi Solutions.
10. Made Local.
Instead of using 3D printing to make production-ready parts or products, most manufacturers are now relying on this method for prototyping a product. Instead of waiting weeks or months to receive a machined prototype, manufacturers can 3D-print them on site in a matter of hours, speeding up the design process. Manufacturers also use 3D printing to create molds, jigs, and fixtures that support their operations and processes.
11. Virtually Identical.
A digital twin is an exact virtual copy of a product, process, or even a complete business ecosystem. Manipulating a digital twin can show how that object or process changes when variables are modified in real time and if those changes improve product quality or the efficiency of the process. This allows manufacturers to test potential changes prior to implementation. It is predicted that by 2025 89% of IoT platforms will contain some type of digital twin technology and that digital twin capabilities will be standard in all IoT offerings by 2027. “Coupled with AI, digital twins are able to test hundreds of production scenarios virtually—allowing for accurate sizing of production systems before final equipment selection is required,” says Goodall.
12. Sustainability.
The environmental, social, and governance (ESG) landscape continues to rapidly evolve, which increasingly requires dedicated personnel and resources. Many manufacturers see the value of meeting or exceeding the often-complex network of reporting requirements, ratings, and disclosures—including providing the ESG transparency their customers expect. “Regulators are also moving toward requiring more disclosures for nonfinancial metrics,” adds Wellener. “Manufacturers are progressing toward their ESG commitments by making operational changes across their value chains.”
Moving Forward
Manufacturers continue to add layers of technologies to their operations to boost efficiency, reduce defects, and build market share. As these companies move toward smart factory transformation, they will utilize new business models for production, such as the microfactory. “One in five manufacturers is already experimenting with underlying solutions or actively developing a metaverse platform for their products and services,” says Wellener.
And, just as manufacturers are beginning to embrace Industry 4.0, Industry 5.0 is already on the horizon.
“Where the fourth industrial revolution focused on using technology to optimize the means of production, the fifth is all about connecting man and machine—that is, the collaboration between humans and smart systems,” states Hitachi Solutions. “Industry 5.0 will leverage the creativity of human experts in collaboration with efficient, intelligent, and accurate machines, in order to obtain resource-efficient and user-preferred manufacturing solutions compared to Industry 4.0.”
- Category:
- GrayWay
- Manufacturing
Some opinions expressed in this article may be those of a contributing author and not necessarily Gray.
Related News & Insights
Advanced Technology
The Opportunities and Challenges of a Second Trump Presidency
Opinion
Advanced Technology, Automation & Controls
Four Use Cases for AI's Growing Role in Manufacturing
Industry
November 25, 2024Data Centers
Gray Expands Reach with Dallas Office
Corporate News
November 14, 2024