Shining a Light on the Lack of Fully Automated "Dark Factories"
For decades, we’ve been hearing about robots taking jobs and the boundless potential of fully automated facilities. An Automation World article mentioned an IBM lights-out keyboard assembly factory in Texas in 2003. Yet more than 20 years later, North America hasn’t been transformed by fully lights-out manufacturing, even with the labor shortages and push to work from home spurred by the COVID-19 pandemic.
Why not? In this article, we’ll look at some factors affecting the gap between theory and practical implementation.
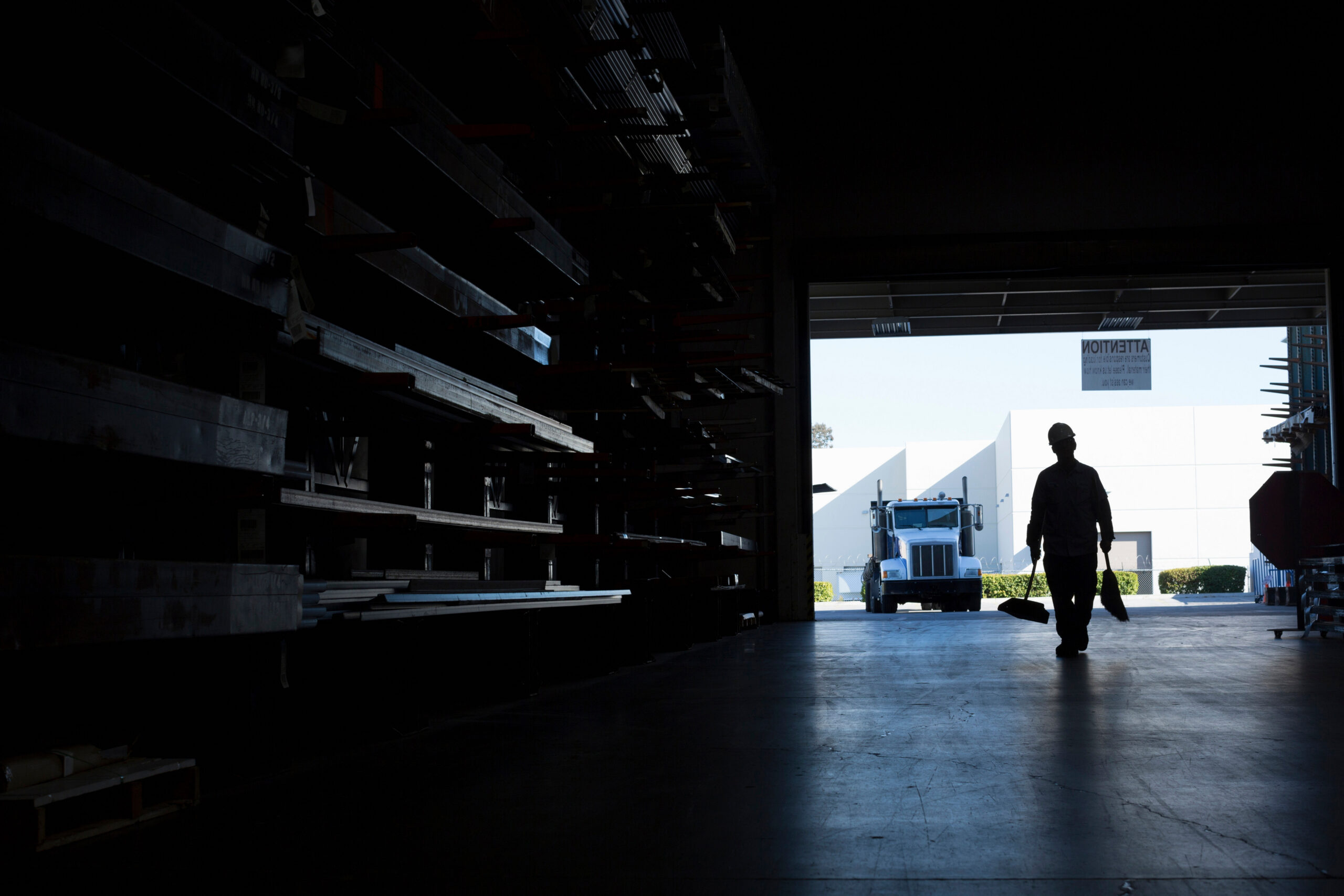
What Is a Dark Factory?
The dark factory represents the peak of industrial automation, named so because it can conduct operations without humans, so there is no need for lights—or many other traditional design elements focused on human safety, comfort, or productivity. Examples of dark factories include Athena’s 3D parts-on-demand service in Arizona featuring a FANUC collaborative robot, and the FANUC dark manufacturing facility in Japan that produces more than 6,000 robots a month.
What Are the Potential Benefits of a Dark Facility?
A fully automated manufacturing or distribution facility offers multiple advantages:
- Overcoming labor shortages. Using automated systems to perform the dull, dirty, dangerous jobs that are less attractive to human workers, manufacturers can meet production targets without worrying about turnover or payroll expenses.
- Increasing productivity. Industrial robots can run at faster speeds without breaks for longer periods—all of which increase production without factoring in safety concerns such as fatigue or discomfort.
- Improving quality. Automated repetitive processes offer a higher degree of consistency and precision when compared to a human operator performing the same tasks manually.
- Satisfying end-customers. Automation allows customers to receive their goods faster and with higher order fulfillment accuracy. Fully automated manufacturing also offers a solution to increase productivity without exploiting human workers—another concern of socially-conscious end-users.
- Permanent energy savings. Without the need to maintain light levels and environmental conditions necessary for human workers, manufacturers can save on energy costs for the facility’s operational lifespan.
- Reducing facility design costs. This is perhaps the dark factory’s biggest advantage over a facility that merely adopts automated elements. When a facility is designed with intent at the outset to be lights-out, elements such as break rooms, locker rooms, dining areas, restrooms, parking lots, HVAC, and more can be greatly reduced in scope or eliminated entirely. This saves on material costs, shortens construction timelines, and conserves resources during the facility’s operation.
High-volume, repetitive processes, and operations that would pose a safety risk for humans are good candidates for full automation.
What Technology Makes Dark Factories Possible?
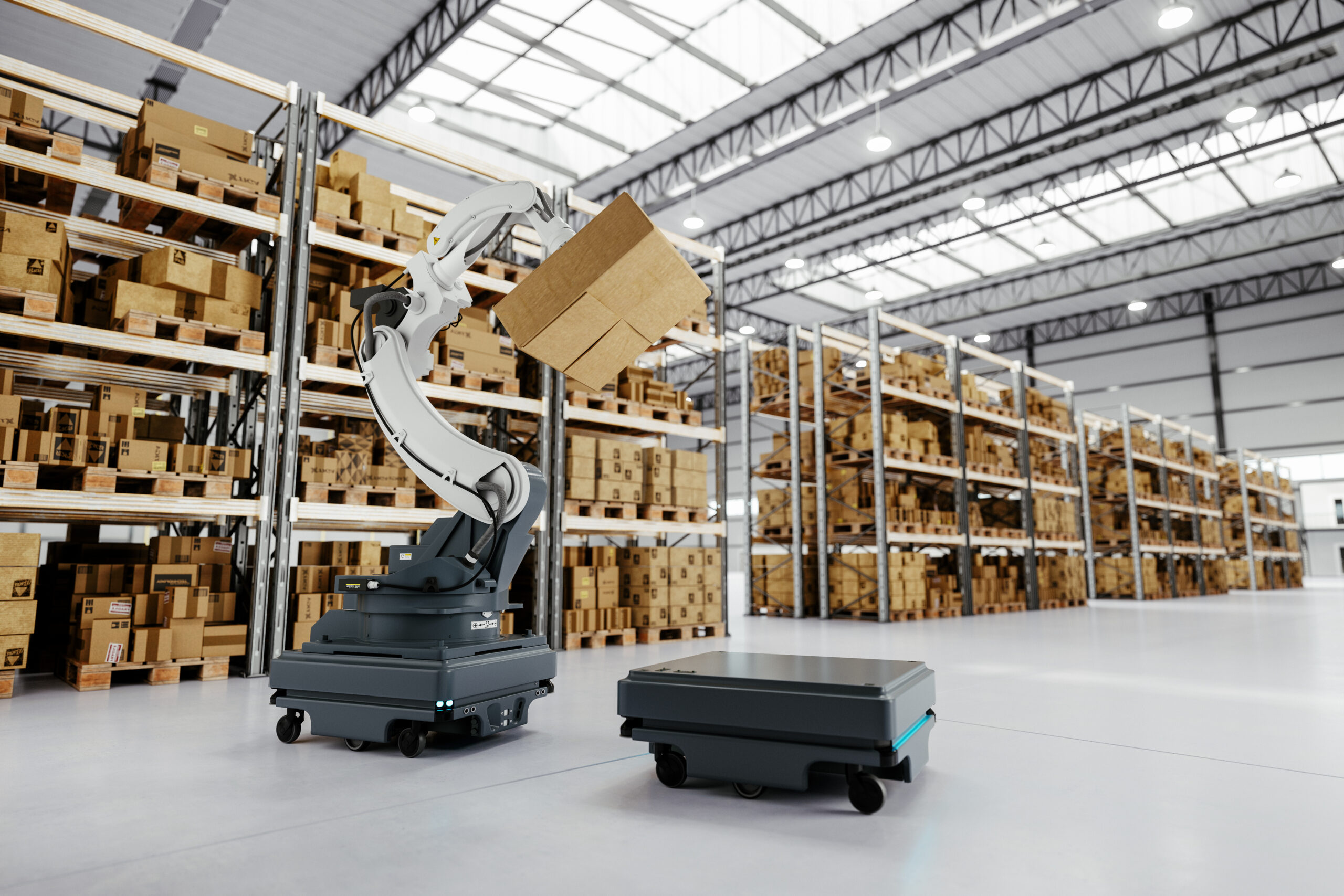
More than anything, running a dark factory depends upon technology that offers dynamic automated functions and the capacity to perform reliably with little maintenance. Depending on the needs of the manufacturing facility or distribution center, the systems required will vary, but generally could include the following:
- Advanced automation. Examples include vision systems for quality control and automated guided vehicles that use sensors and navigation systems to transport materials.
- Robotics. Autonomous robotic arms equipped with specialized end-of-arm tooling can be used for a variety of tasks, such as picking for order fulfillment, placing items on a conveyor, or performing precise manufacturing operations.
- Internet of Things (IoT) technology. IoT sensors and monitoring devices can track key parameters such as temperature, humidity, and equipment status, which are vital to QA processes.
- Artificial intelligence (AI). One of the most useful functions of AI is predictive maintenance, which uses algorithms to analyze data and predict impending equipment failure to minimize downtime.
Best practice dictates that rather than implement any of these as a standalone solution, these systems are most effective when they work in concert, leveraging cross-stream data to ensure that productivity and efficiency are optimized.
What Challenges Do Dark Factories Pose?
Despite the potential benefits of lights-out factories, multiple challenges prevent companies from embracing the dark factory model:
- Full automation is complex. To keep production running smoothly and prevent downtime, detailed system networking and programming are necessary on the front end as well as effective troubleshooting and maintenance procedures on the back end. Human expertise is required to plan and implement advanced automation. Similarly, keeping automated systems running at peak efficiency requires people with specialized skills. However, the industry is facing a major shortage of skilled tech workers. A Korn Ferry report found that the U.S. could lose out on $162 billion worth of revenues annually unless it finds more high-tech workers.
- Automation isn’t well-suited to all processes.
- A 2023 Forbes article suggests that since human logic is still needed for non-standard processes, the dream of a global network of dark warehouses won’t be realized until higher levels of human reasoning can be automated.
- A 2022 Wall Street Journal article addressed some of the limitations that CIOs encountered that prevented companies from fully adopting warehouse technology. “While warehouse robotic technology is mature in some areas, such as transporting goods from point A to point B, it is less mature in terms of picking up and placing down goods,” the article states.
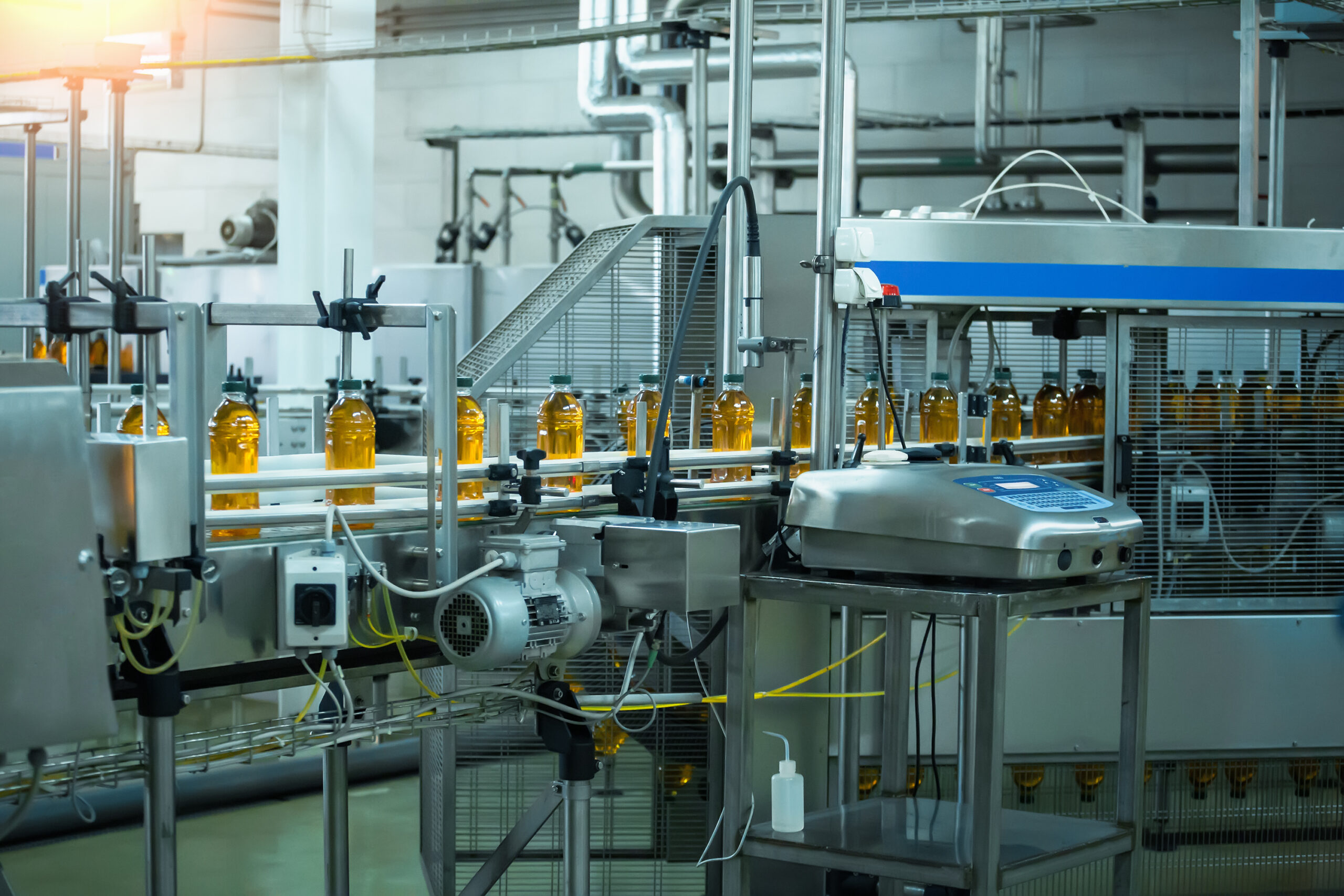
Hybrid Automation May Offer the Best of Both Worlds
A fully dark factory or distribution center may be too great of a leap for many companies; however, a hybrid approach to automation can still be extremely beneficial. Amazon is an excellent example of a company that has embraced automation without going fully lights out.
In response to Amazon’s disruptive business model, the U.S. Postal Service has implemented a range of automated technologies to perform high-volume repetitive processes and avoid falling into obsolescence in the logistics industry. These include the following:
- Machines using (OCR) technology to read over 95% of hand-addressed letters and machine-printed mail
- 365 automated guided vehicles (AGVs) in 25 facilities, which comprises one of the largest material-handling systems in the world for moving mail
- More than 200 miles of conveyors within postal facilities
- The largest gantry robotic fleet in the world with 165 robotics systems moving 300,000 mail trays per day
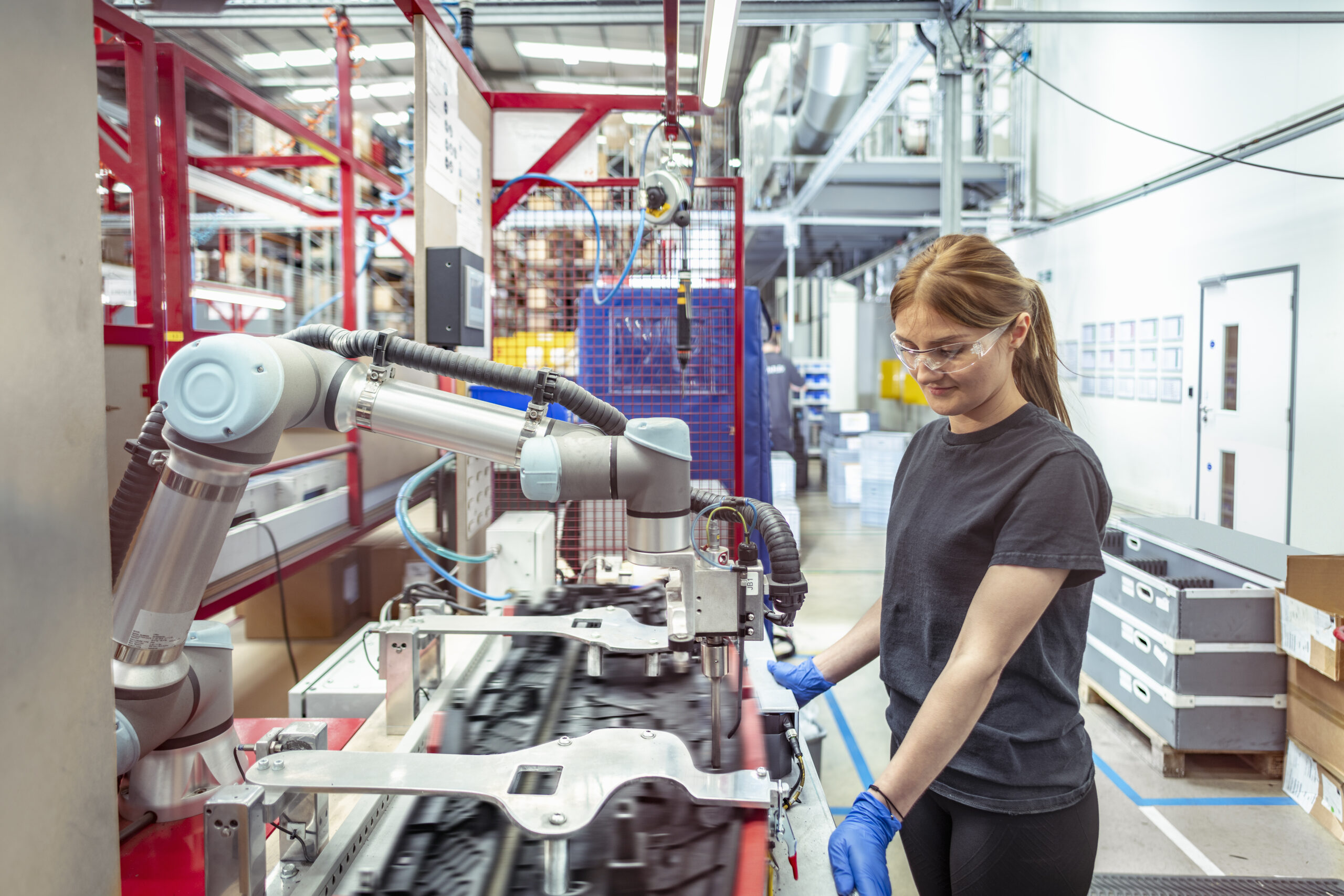
Even with that level of automation, U.S.P.S. facilities still aren’t completely lights out. Human workers are still needed to move pallets, drive forklifts, and replace full containers with empty ones for robotic sorting systems. For the U.S.P.S., automation isn’t a luxury, but a necessity to rapidly modernize to stay relevant amid the explosive growth of Amazon and other distribution giants.
Dim Facilities: Long-Term Shift or Stopgap Solution?
A fully automated, dark factory may be an overly ambitious step for many manufacturers to take all at once, but there are still benefits to investing in automation. A “dim” factory where humans, automation, and robotics work together is a more attainable and likely scenario.
Implementing automation in areas where it can have the greatest impact on efficiency, productivity, quality, and safety allows companies to reap many benefits and also sets the stage for adopting a dark factory model in the future.
Some opinions expressed in this article may be those of a contributing author and not necessarily Gray.
Related News & Insights
Distribution, Specialty Equipment
Equipment Manufacturing Trends for 2025
Industry, Opinion
Advanced Technology, Specialty Equipment
How an Equipment Design-Build Partner Benefits Your Business
Industry, Opinion
Manufacturing
Gray, UBE C1 Chemicals America, Inc., and Cornerstone Energy Park Celebrate Groundbreaking for New Manufacturing Facility
Corporate News
February 26, 2025