Robotics for Today's Food & Beverage - Top Technology Every Facility Needs
The food & beverage industry is under tight scrutiny from consumers, industry regulators, employees, and the general public. Meeting various demands successfully requires efficient use of resources.
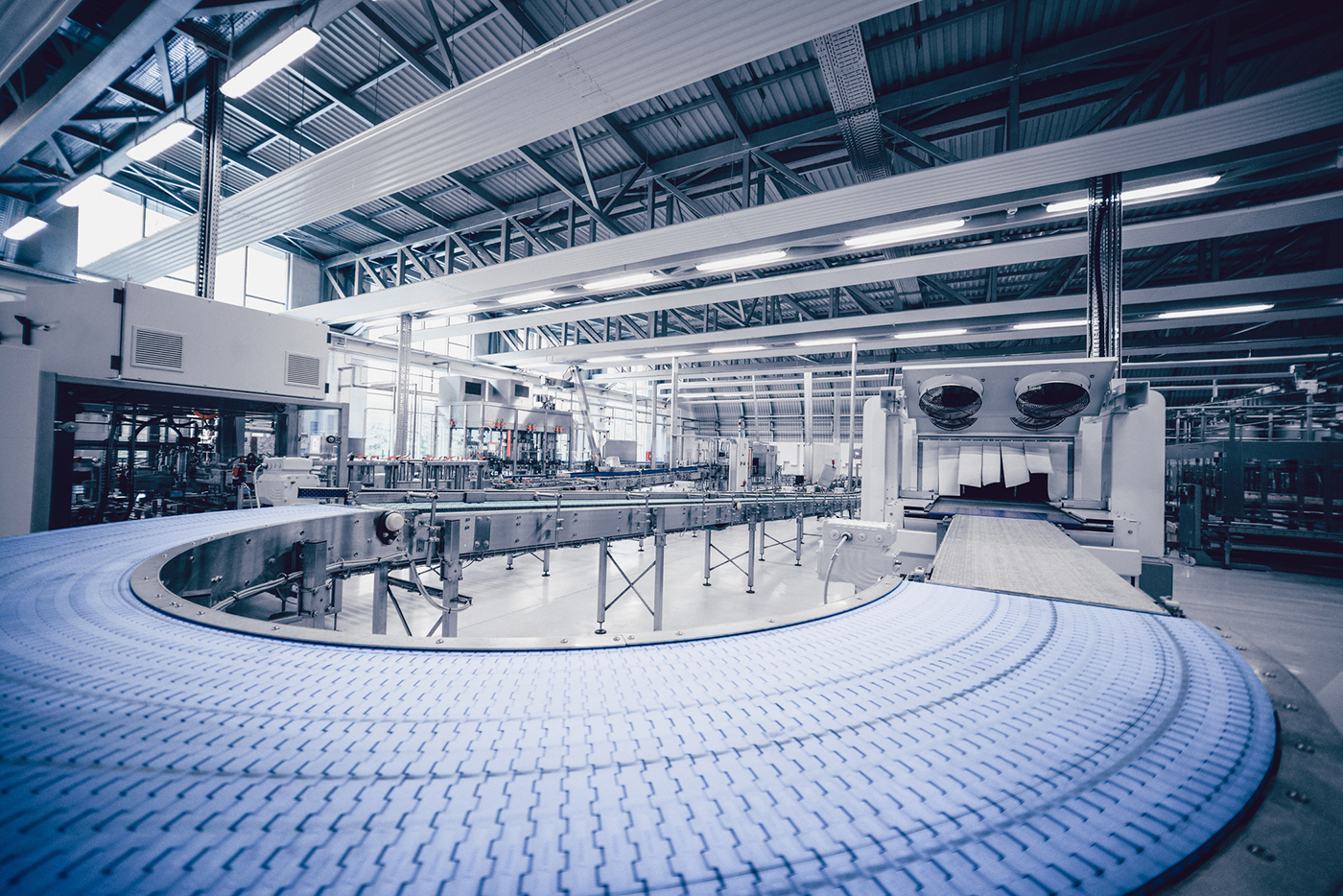
Automated systems can make a positive impact on multiple priorities such as the following:
- Minimizing food waste
- Improving traceability
- Enhancing food and workplace safety
- Overcoming a workforce shortage
- Increasing productivity and efficiency
Facilities that strategically implement robotic solutions can realize multiple benefits to maximize their return on investment. Along with the benefits of automation, advanced technologies such as machine learning and AI offer transformative change to companies that are in a position to take advantage of them. However, AI needs quality data to be effective, so a foundation of automation needs to be in place first in order to collect the required data.
As a starting point, it’s useful to look at automation solutions that are designed specifically to solve food & beverage challenges and have a track record of delivering value. In this article we’ll look at three robotic/automation solutions that food & beverage facility managers should seriously consider.
1. Automating food & beverage picking and packing.
Historically, industrial robotics have proven to be effective and reliable automating repetitive processes. At first, automated picking and packing was best for objects that weren’t too delicate and could easily be presented in an orderly fashion. However, several notable advancements have made picking and packing robots more versatile within food & beverage applications:
Collaborative robots: As an alternative to traditional high-volume industrial robots, collaborative robots allow picking and packing to be done for higher mix, lower volume operations with a smaller automation footprint. Collaborative robots do not always need to be caged for safety, depending on the application, and they can be moved and re-purposed for tasks that require the same fixed specifications such as payload and reach.
Specialized grippers: Soft, pressure-sensitive grippers can now handle delicate food products without causing damage. The wide variety of end-of arm tooling now available gives food & beverage facilities many options to automate food handling processes that previously required human hands.
Vision systems: Instead of requiring trays to provide robots with orderly product presentation, vision systems can pick and pack from disorganized piles and do not require that products be perfectly aligned. Vision systems are also immensely useful for eliminating human error to reach outstanding quality control and measurement standards. Industry Week cites an example of Heineken using a vision system to achieve a 0% failure rate inspecting bottles.
2. Cleaning food and beverage facilities with autonomous robots.
Food & beverage facilities must comply with food safety regulations from the FDA, USDA, and other regulatory bodies. Non-compliance can result in costly recalls, re-inspection fees, fines, and other penalties.
The U.S. FDA Code of Federal Regulations Title 21 stipulates that “buildings, fixtures, and other physical facilities of the plant shall be maintained in a sanitary condition and shall be kept in repair.” For food & beverage manufacturers, keeping a facility clean and in good repair and clean should be an obvious requirement. However, issues such as failure to maintain building and physical assets, and lack of sanitation monitoring accounted for about 50% of inspection citations as indicated by FDA data between 2009 and 2023, according to Food Safety Magazine.
Cleaning is an ideal task for robotic automation. Robots are able to perform floor scrubbing, pressure washing, ultraviolet (UV) disinfection, and other sanitization protocols. A robotic cleaning solution offers the added benefit of improving worker safety by not exposing humans to harsh cleaning solutions.
3. Tracking data with IoT-enhanced robotic solutions.
Companies that strategically collect, analyze, and use data can react much faster and make swifter course corrections than those that do not have easy access to reliable data streams. Internet of Things (IoT) solutions integrate different pieces of machinery and share real-time data. Food & beverage processors can use IoT data to meet new industry standards, such as complying with FDA food traceability requirements by January 2026.
IoT production line data reveals bottlenecks and equipment performance so that decision-makers can improve workflow efficiency. Whether it’s for compliance, efficiency, or another business imperative, leveraging actionable data needs to be a priority for food & beverage facilities. IoT solutions that monitor key systems provide many benefits, including:
- Preventing waste by maintaining a controlled environment and raising early alarms
- Reinforcing traceability
- Connecting systems for seamless communication
- Providing decision-makers with current information
- Feeding AI systems with relevant data, such as overall yield and factors that influence yield as described in the ERP Today story on AI in the food & beverage industry
The advantages of robotics go well beyond providing an option for labor-intensive repetitive tasks. Automated solutions that incorporate IoT and AI can be milestone change events that affect everything from the production line to C-Suite-level decision-making.
The range of available robotic solutions can quickly become overwhelming; however, an experienced system integrator and automation expert can identify pain points and develop a solution that optimizes specific food & beverage operations. A strategic implementation process is invaluable in prioritizing goals and developing an automation roadmap that delivers the necessary value and ROI.
Some opinions expressed in this article may be those of a contributing author and not necessarily Gray.
Related News & Insights
Food & Beverage
Gray and Maruchan Celebrate Groundbreaking for New Facility
Corporate News
December 18, 2024Food & Beverage
Gray Project Receives Manufacturing Innovation Award
Corporate News, Industry
December 04, 2024Advanced Technology, Automation & Controls
Four Use Cases for AI's Growing Role in Manufacturing
Industry
November 25, 2024