Redefining Automation: Moving Manufacturing Jobs Forward
It doesn’t seem that long ago when a large hue and cry erupted over manufacturers installing robots for fear they would take away factory jobs. But, as reported in the recent blog post “Redefining Manufacturing,” manufacturing is turning around, and it is manufacturing technology that continues to play a growing role. In April, the Association for Manufacturing Technology (AMT) reported, “Many key economic indicators are showing strong, positive signs for our industry. The Purchasing Managers’ Index moved up for the sixth consecutive month, suggesting continued expansion of the manufacturing sector. February’s 57.7 is the highest level for the index since August 2014.”
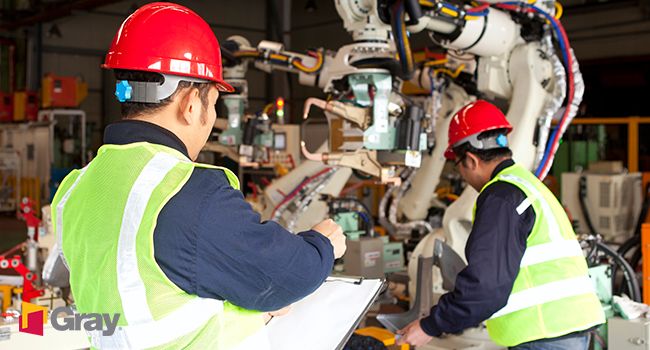
Feared as a jobs stealer, automation a jobs creator.
Albert Einstein once said, “We cannot solve problems on the same level of thinking that created them.” This famous saying applies very well to automation, doesn’t it?
It doesn’t seem that long ago when a large hue and cry erupted over manufacturers installing robots for fear they would take away factory jobs. But, as reported in the recent blog post “Redefining Manufacturing,” manufacturing is turning around, and it is manufacturing technology that continues to play a growing role. In April, the Association for Manufacturing Technology (AMT) reported, “Many key economic indicators are showing strong, positive signs for our industry. The Purchasing Managers’ Index moved up for the sixth consecutive month, suggesting continued expansion of the manufacturing sector. February’s 57.7 is the highest level for the index since August 2014.”
According to the Association for Advancing Automation (A3), over the seven-year period from 2010 to 2016, 136,748 robots were shipped to U.S. customers—the most in any seven-year period in the U.S. robotics industry. In that same time period, manufacturing employment increased by 894,000, and the U.S. unemployment rate decreased from 9.8 percent in 2010 to 4.7 percent in 2016.
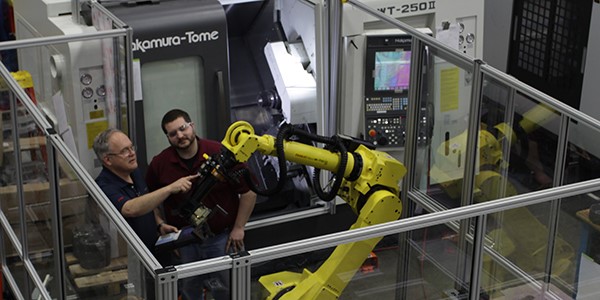
No industry has adopted automation as extensively as the automotive industry, A3 continues. At General Motors, Industry 4.0—which encompasses automation, sensors, Industrial Internet of Things (IIoT) connectivity and data analytics to drive productivity and innovation—is the mantra for continued profitability. During its recent period of increased profitability from 2012 to 2016, GM grew from 80,000 U.S. employees to 105,000, all while increasing the number of new U.S. robot applications by approximately 10,000.
A critical takeaway from these results is that certain manufacturing jobs are gone and not coming back, particularly those deemed the most unsafe, such as manual machine loading and unloading and other material-handling tasks. Just as critical is that this new manufacturing jobs’ expansion is reshaping education, training and the availability of apprenticeships, much like a traditional European model.
According to a recent Bloomberg column, local efforts are proving the concept. YouthForce NOLA, a partnership of political, business and education leaders in New Orleans, places 1,200 high-school seniors from local public high schools in paid internships in fields such as software development and advanced manufacturing. Businesses work with school administrators to ensure students receive practical, skills-based classroom instruction. The goal is to help students obtain professional credentials for high-wage jobs that don’t require bachelor’s degrees. (YouthForce NOLA was the recipient of $5 million in grants from Bloomberg Philanthropies.)
Another successful model is the state-run Apprenticeship Carolina program in South Carolina, serving as an intermediary between businesses, workers and educational institutions. It matches employers with the state’s technical colleges, who tailor classes to meet the companies’ needs, and handles most of the paperwork (companies have to register their apprenticeship programs with the federal and state governments). Employers are responsible for paying apprentices’ wages and mentoring them on the job. Since 2007, more than 25,000 South Carolina workers have completed apprenticeships; the number of companies participating in the program has increased from 90 to 880.
Technology Suppliers Are In, Too
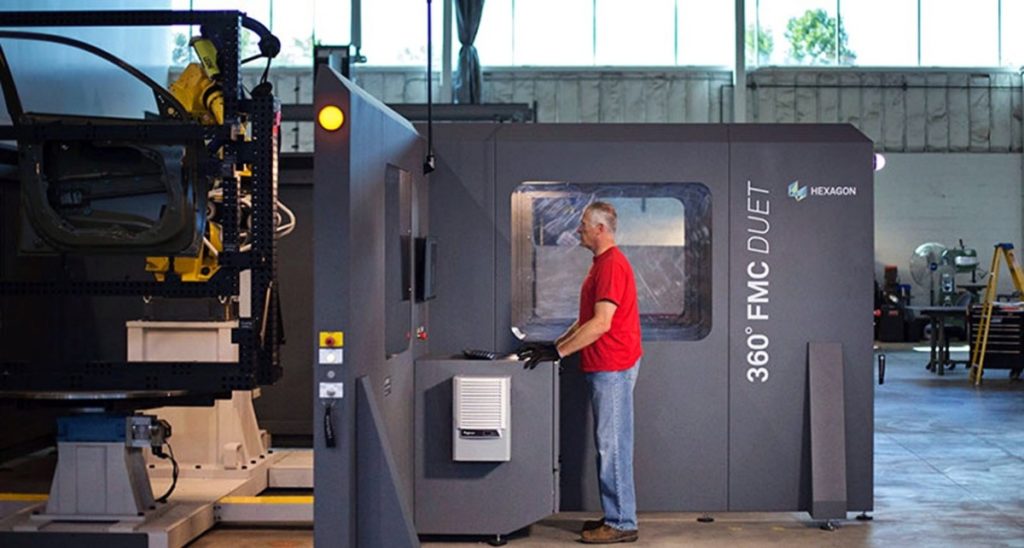
The manufacturing technology community also recognizes that automation is a thread tying safe and productive manufacturing facilities together. Methods Machine Tools Inc., a supplier of precision machine tools and 3D printing technology just announced a new Automation and Integration Center in its Charlotte, N.C., facility. It will showcase equipment and capabilities including building cells and performing runoffs to prove automation benefits.
Automation is not a new concept at Methods, says the company. “Manufacturers are increasingly realizing that incorporating automation and robotics is key to their productivity, profitability, and future,” says Bryon Deysher, Methods executive director of the board. “Our new Automation and Integration Center will provide expanded capabilities for all projects spanning the U.S. and enhance the value of our customer experience at every level.” With existing automation centers at Methods headquarters in Sudbury, Mass., and also in Wixom, Mich., the company has seen automation applications continue to grow, from small automated centers to large, complex multi-function machining cells. “I envision the future need for expanding this model in other regions of the U.S. as well,” Deysher adds.
Emerging companies not only see automation technologies as a given, they are creating pathways for hourly employees to retrain to take maximum advantage of them. Amazon offers an innovative benefit for its hourly employees called the Career
Choice program to help workers gain the skills needed for today’s most in-demand jobs, based on information from sources such as the U.S. Bureau of Labor Statistics.
The company pre-pays 95 percent of the cost of tuition for associates to go back to school and take courses related to in-demand fields—such as robotics, computer science, engineering and IT—regardless of whether those skills are related to jobs at Amazon. Onsite classrooms allow college and technical classes to be taught inside fulfillment centers to make participation as easy as possible.
Far from the job-stealing fears they originally inspired, automation technologies are taking thinking about manufacturing, education, economics and productivity to a whole new level. Let the problem-solving continue.
- Category:
- Industry
- Manufacturing
Some opinions expressed in this article may be those of a contributing author and not necessarily Gray.
Related News & Insights
Food & Beverage, Automation Solutions
The Impact of Tax Reform, from a Manufacturer’s Perspective
Projects
Manufacturing
Diversity in Manufacturing: How Women Can Help Shrink the Skills Gap
GrayWay
Manufacturing
Building Manufacturing Careers: Discover How Manufacturers Are Engaging Women to Fill the Workforce
GrayWay