Manufacturing Industry Launching Initiatives to Bolster Perception of Manufacturing Jobs
Manufacturing organizations are addressing image problems with new initiatives to move the public’s perception to a more accurate understanding of the manufacturing industry.
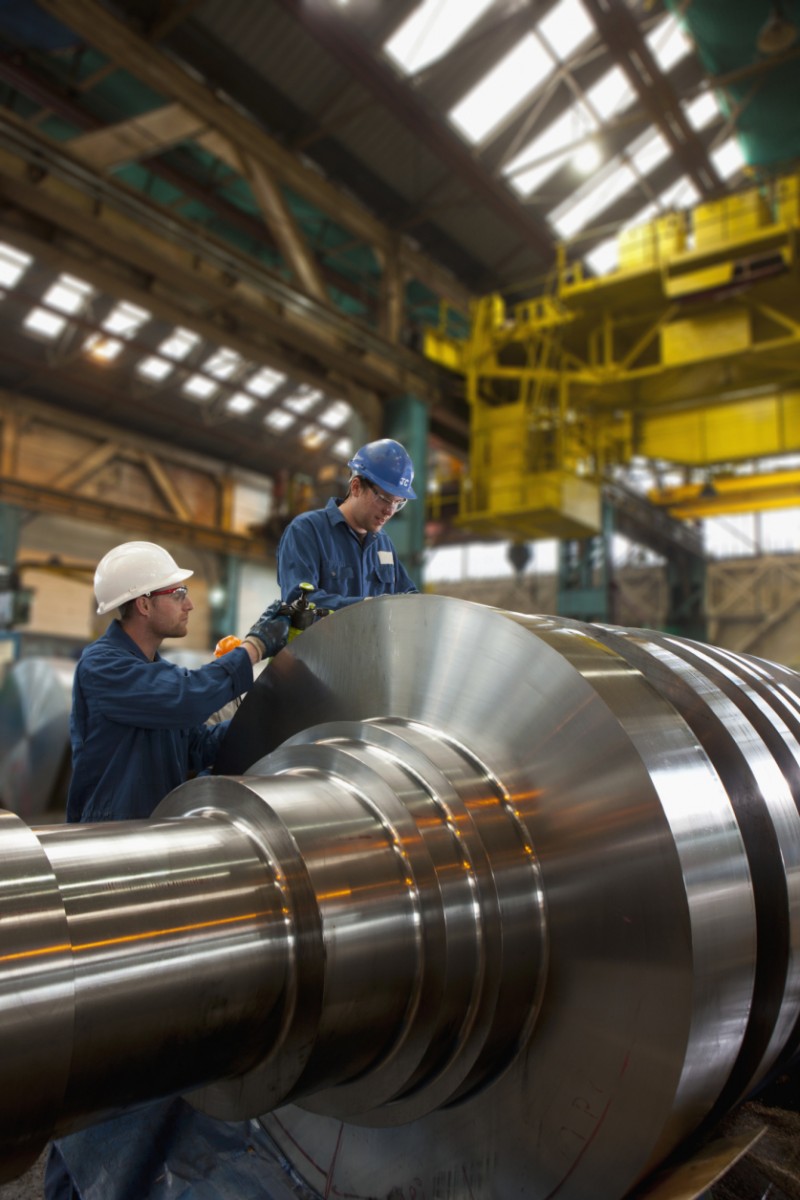
Several decades ago, boys and girls in high school were not only encouraged to sign up for vocational classes, they viewed these classes as essential to getting a job upon graduation. Ask a teenager today how important vocational studies are to employment after high school and his response might be, “Huh?”
Since then, society has become convinced that the only way to find good-paying, stable employment is by having a four-year college degree, and jobs in manufacturing have all but lost their appeal. In fact, a study conducted by Deloitte and The Manufacturing Institute found that among 18 to 24 year olds, manufacturing ranks dead last among industries in which they would choose to start careers—a startling finding for manufacturers desperately trying to fill jobs.
But while young folks today genuinely desire a college degree, getting one is easier said than done. According to the National Center for Education Statistics, for every 100 ninth graders in the U.S., only 68 graduate from high school on time. Of those, 40 enroll directly in some college program (associate’s, bachelor’s, or a trade school). Of those, only 27 are still enrolled the following year. Of those, 18 earn an associate’s degree within three years, or a BA in six years. A staggering 82 of the original 100 ninth graders do not succeed in obtaining any degree, and will have difficulty competing in a skilled labor force.
Beyond the diversion of young people in pursuit of a college degree, there are other reasons why it is difficult to fill manufacturing jobs. The survey also found that some 77 percent of Americans fear the loss of manufacturing jobs to other nations, fueling the idea that these jobs are unstable. Add to that the fact that most Americans (74 percent) believe that manufacturing jobs are difficult to get, and you have a perception problem bigger than anyone can comprehend.
![]() |
About 6,600 people work at Toyota Motor Manufacturing’s Georgetown, Ky. plant where the Camry, Camry Hybrid, Avalon and Venza are made. |
Wil James, president of Toyota Motor Manufacturing, Kentucky, Inc. is one person who can attest to the problem.
“The stigma that manufacturing jobs are among the least desired and/or least rewarding fields to enter for a career is an issue for our industry,” began James. “It’s misguided, and leads to a no-win situation all around. From my perspective, the solution begins with the manufacturing industry taking ownership and working to move the American public’s perception to a more accurate understanding of what we have to offer.”
James says there are initiatives that have emerged to fight this stigma, and his company is supporting them, like The Manufacturing Institute’s “Dream It. Do It.,” campaign. Jennifer McNelly is president of The Manufacturing Institute and directly oversees Dream It. Do It. She says while the impact of manufacturing continues to be great, the industry is not doing its part to spread the word.
“For every dollar invested in manufacturing, there’s a 1.3 multiplier. We have a great impact in building communities, but we’re really not very good at talking about it,” she said. “Dream It. Do It. helps to demystify manufacturing by portraying it as clean, high-tech and innovation-driven. Dream It. Do It. gives manufacturers an avenue to open their doors to their communities—having teachers, parents and students understand the real excitement and value in manufacturing careers. Dream It. Do It. also helps young people understand the kinds of skills that those jobs require. You don’t just show up—you need to have applied STEM (science, technology, engineering and math) skills and be ready to learn and adapt quickly with the innovations happening every day on the factory floor. Manufacturers are problem solvers and team players.”
McNelly says manufacturers have also missed the boat with regard to their human resource supply chain, placing more emphasis on internal referrals rather than targeting people in our educational system.
“Manufacturers inherently operate within systems and processes,” began McNelly. “We innovate and we figure out how we create efficiencies, and constantly improve our processes—that is the core of Lean and Six Sigma. However, we have cumbersome and outdated methods for attracting and managing the human capital supply chain. Most manufacturers today use word-of-mouth tactics, rather than work with the education and publicly funded workforce investment systems, which is where the workforce is being produced.”
McNelly and James both agree that changing the perception problem doesn’t begin and end with young people entering the workforce, but extends way beyond them.
“Overall, it’s essential that we find better and systemic ways to engage not only students, but parents—who influence the career directions of their children—and guidance counselors—who largely have a less-than-favorable view of manufacturing as a career option and often guide the best and brightest students away from it,” said James.
James named three reasons why people should consider a career in manufacturing:
- Great compensation and benefits.
- Rewarding, challenging work. Modern, advanced manufacturing makes real use of knowledge and skills, and we are always driven to improve and make things better. In this environment, an employee knows that their talents are valuable, that they’re being maximized and that they’re growing.
- The knowledge that your job is meaningful benefits others and society. By its very definition “manufacturing” implies that we make things, and by making things you help satisfy a need or desire of consumers across the globe.
- Category:
- Industry
Some opinions expressed in this article may be those of a contributing author and not necessarily Gray.