Lean and Sustainability: Where the Two Intersect
What is the relationship between lean and green? Let’s first consider what we mean. Lean can be narrowly defined as the elimination of waste. This is convenient if we view green as eliminating waste, defined as anything noxious to the environment. However, more recent thinking about lean, based on Toyota as a model, suggests a broader definition of lean. The Toyota Way aspires to continuous improvement and respect for people. Respect for people starts with contributing to society, which includes having a positive impact on the environment. How do you accomplish that? You do it through continuous improvement. What we are trying to accomplish with the green movement can be more broadly viewed as the constant struggle to have only positive impacts on the planet and the health of its life forms.
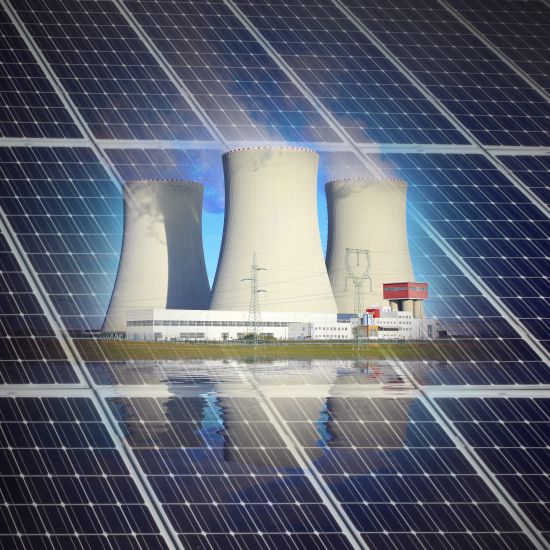
What is the relationship between lean and green? Let’s first consider what we mean. Lean can be narrowly defined as the elimination of waste. This is convenient if we view green as eliminating waste, defined as anything noxious to the environment. However, more recent thinking about lean, based on Toyota as a model, suggests a broader definition of lean. The Toyota Way aspires to continuous improvement and respect for people. Respect for people starts with contributing to society, which includes having a positive impact on the environment. How do you accomplish that? You do it through continuous improvement. What we are trying to accomplish with the green movement can be more broadly viewed as the constant struggle to have only positive impacts on the planet and the health of its life forms.
Let’s consider three examples. First, when Toyota Motor Sales in California decided they needed more space on their Torrance campus, they decided to aim for a LEED Gold award, which they achieved in 2004 (read more in Toyota Culture). They also decided their General Manager of facilities, with no background in environmentally-friendly buildings, would lead the project and that they would do a lot of the thinking themselves. To make the challenge interesting, he was asked to accomplish this without increasing the construction cost. He studied intensively and pulled together a team of people trained in Toyota-style problem solving. Through a systematic improvement process, they began to understand the targets and options as well as focus their efforts.

There were large breakthroughs in thinking. For example, to save costs, they realized it was possible to build the external structure out of concrete instead of traditional steel. They got the idea by observing that warehouses are made of concrete. This limited the number of floors they could build but greatly decreased the cost, allowing for many other improvements. They used concrete waste from the process to make various walkways and garden ornaments. The savings could then be used for solar panels, double-pane glass, efficient insulation, and a reflective cool roof.

In the construction process itself, 95 percent of all waste was recycled and reused. They also worked with local suppliers, such as the supplier of existing carpeting, which did not have experience with recyclable materials. Toyota convinced this company to learn to produce environmentally-friendly carpet which matched their existing furnishings and panels. Interestingly enough, this new methodology became the new highly successful business model for this supplier. For Toyota’s campus in California, the result of all their efforts was a brighter, more open, more comfortable building, which was associated with lower absenteeism and higher productivity. Another benefit was growth and awareness among Toyota team members, who through their involvement learned enhanced teamwork, problem solving, and partnership.
Second, throughout their global operations, Toyota has set goals for being environmentally-friendly, such as zero landfill use or 100 percent water reuse. They have used the culture of respect for people and continuous improvement to drive these efforts. About a decade ago at the Georgetown, Kentucky plant, every department began to track how much trash was thrown away. This led to major recycling efforts including reusable plastic containers for auto parts and materials, elimination of conventional trash cans in favor of color-coded recycle bins, and composting food which is used in a greenhouse to grow seedlings that grow into vegetables and then donated to a food bank. In one year, the garden produced 2500 pounds or 1570 meals (see Toyota Culture for more). There were many other improvements, such as developing a new type of bio filter in paint that reduced volatile organic compounds potentially harmful to humans.
Third, Toyota was one of the first automakers to make a major push into environmentally-friendly vehicles. It started in the early 1990s, when business was booming and chairman Eiji Toyoda challenged the company to think beyond the boom and work on new technology for the 21st century. An executive think tank group concluded they would need environmentally-friendly transport with high fuel economy that also felt spacious for the family. This led to the relatively crude first generation Prius in 1997. GM concluded that it was only a stopgap solution and they would leapfrog hybrids and go to an all-electric car. Toyota understood continuous improvement — get a practical first model into production and then learn like crazy.
They did as much as possible internally so they could learn. They learned about battery technology through their joint venture with Panasonic. They learned about making electric motors that power vehicles. They learned about computer systems to govern the use of different power sources. They learned about switching circuits, and so much more. Today, Toyota is preparing for its fourth generation Prius. It took about ten years to sell 1 million vehicles, and Toyota is approaching the point of selling 1 million hybrids each month. They have invested heavily in fuel cell technology, and guess what? It will be a hybrid of hydrogen fuel and electric motors driven by a battery. Their long-term journey of continuous improvement and learning provides core technology know-how needed for whatever direction environmentally-friendly vehicles go.
What can we learn from this? When I wrote The Toyota Way, I argued that long-term thinking is essential to becoming a lean learning organization. We also needed to have people developed in a way of thinking and the processes needed for continuous improvement. Certainly the underlying principles of lean and sustainability have much in common. It is our old friend the scientific method of Plan-Do-Check-Act in a culture of continuous improvement and respect for people. Meeting the challenge can mean treating our planet well at no additional cost. Sometimes it helps if we do the hard thinking and learning ourselves so we can become a more adaptable organization.
Dr. Jeffrey Liker is professor of industrial and operations engineering at the University of Michigan and author of The Toyota Way. He leads Liker Lean Advisors, LLC and his latest book (with Gary Convis) is The Toyota Way to Lean Leadership.
Some opinions expressed in this article may be those of a contributing author and not necessarily Gray Construction.
- Category:
- Industry
- Manufacturing
Some opinions expressed in this article may be those of a contributing author and not necessarily Gray.
Related News & Insights
Distribution, Specialty Equipment
Equipment Manufacturing Trends for 2025
Industry, Opinion
Advanced Technology, Specialty Equipment
How an Equipment Design-Build Partner Benefits Your Business
Industry, Opinion
Manufacturing
Gray, UBE C1 Chemicals America, Inc., and Cornerstone Energy Park Celebrate Groundbreaking for New Manufacturing Facility
Corporate News
February 26, 2025