How Disruptive Digital Technology is Rebooting the Economics of Manufacturing
To maintain their competitive edge and keep up with low-cost countries, manufacturers in the U.S. must reduce operational costs. This means improving efficiency and productivity. Technology is the answer—especially the combined one-two punch of the Internet of Things (IoT) and automation. IoT refers to the use of hundreds or thousands of sensors that are embedded in equipment to capture production data, which are then analyzed to increase performance and eliminate potential mechanical problems before they occur. This capability, of course, also leads to better decision-making, in real time.
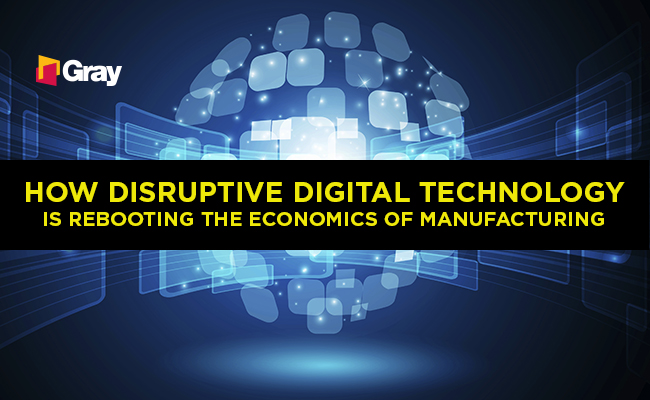
“Smart manufacturing is about creating an environment where all available information—from within the plant floor and from along the supply chain—is captured in real time, made visible, and turned into actionable insights,” states Kevin O’Marah, chief content officer for SCM World, on industryweek.com.
Proof that the age of IoT is well underway in manufacturing
Many manufacturers are too busy running their operations to pay much attention to IoT and data analysis, but this is starting to change. For example, recent surveys show that:
- About one-third of U.S. manufacturers are using data generated by smart sensors to enhance manufacturing/operating processes and believe it is “extremely critical” to adopt an IoT strategy
- Many companies indicate their IoT budgets will continue to increase year over year, to an average of about $103 million per year by 2018
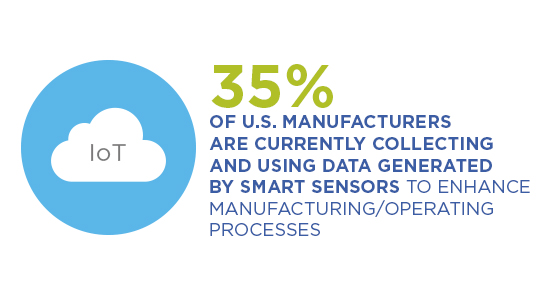
“The age of IoT is well underway,” says Natarajan Chandrasekaran, managing director and CEO for Tata Consulting Services. “The question is, however, are businesses ready to realize the full potential of this technology? Our latest global trend study found that leaders are using IoT technologies to completely re-imagine their businesses, ranging from business models and products to business processes and workplaces.”
Further, Tata Consulting Services indicates that 80 percent of the companies surveyed have increased their revenues by investing in IoT. In 2014, these companies enjoyed an average increase of 15.6 percent in revenue, with some as high as 30 percent.
Automation advances
In manufacturing, the greatest improvements often happen when IoT is coupled with automation. Automation technology is becoming more affordable, multifunctional, and programmable, with easier-to-use interfaces. It can be designed for almost any manufacturing application. Automation increases throughput, reduces mistakes, and minimizes waste. Automated processes also require fewer employees. This is especially important from the labor perspective, because manufacturers are struggling to find the qualified workers they need to run (or expand) their operations. Robots and automation can reduce production costs dramatically, making it more tempting for companies to reshore back to the U.S.
Return on investment (ROI) can be impressive with automation. According to the Robotic Industries Association, the positive impact the labor savings has on cash flow over the service life of a robotic system can be startling.
For a typical $250,000 turnkey installation, “the robot is about one-third of the cost of the total installation, which includes all of the design, tooling, safety guarding, conveyors, integration services, programming, and installation,” says Ron Potter, director of robotics technology for Factory Automation Systems in an article on robotics.org. “That’s all included and goes into the initial cost of the system. Once the initial cost is made, which takes two years or so for payback, that’s where you start to reap the benefits of low-cost labor from a robot. During years 3 through 10, the positive cash flow is almost exponential. By years 7 and 8, that $250,000 robotic investment turns out to be about $1.5 million of positive cash flow, and it keeps going up from there.”
Is your company ready for the next industrial revolution?
A Fortune 500 survey found that 72 percent of CEOs reported their biggest challenge was keeping up with changing technology—which is especially true for manufacturing. This creates heavy pressure on already-busy plant managers, who simply don’t have time to understand and implement new technologies such as IoT.
There is no better place to get a crash course in IoT and automation than Hannover Messe, being held this year April 25-29 in Hannover, Germany. The focus is Industry 4.0—essentially the integration of IoT, automation, and other disruptive technologies to maximize efficiency and productivity.
The U.S. Department of Commerce will lead the largest-ever U.S. delegation to this industry trade event, where about 180 U.S. companies and research institutions will present their latest solutions for advanced manufacturing. In addition, the U.S.-based Industrial Internet Consortium will be there to promote the establishment of the industrial IoT.
“Our Department of Commerce team is consulting with each U.S. exhibitor and we believe their unique products, innovations, and investment opportunities are well suited for the global industrial technology market,” says John B. Emerson, U.S. ambassador to Germany. “Foreign attendees and exhibitors will have the chance to connect with some of the leading American companies and organizations at the event.”
Mark Crawford is a Madison, Wisconsin-based freelance writer who specializes in business, science, technology, and manufacturing.
- Category:
- Industry
- Manufacturing
Some opinions expressed in this article may be those of a contributing author and not necessarily Gray.