How an Equipment Design-Build Partner Benefits Your Business
For industrial businesses, equipment investments are no small matter. From complete processing skids to the smallest components, equipment represents the beating heart of industrial operations. Ensuring these critical systems are up to the rigors of continuous use is vital. Businesses commit substantial capital to acquire equipment that will meet their processing needs and promote long-lasting operational success. While equipment that’s widely produced and readily available may not demand as high a Capex investment and can serve adequately in some applications, many processes demand more tailored solutions.
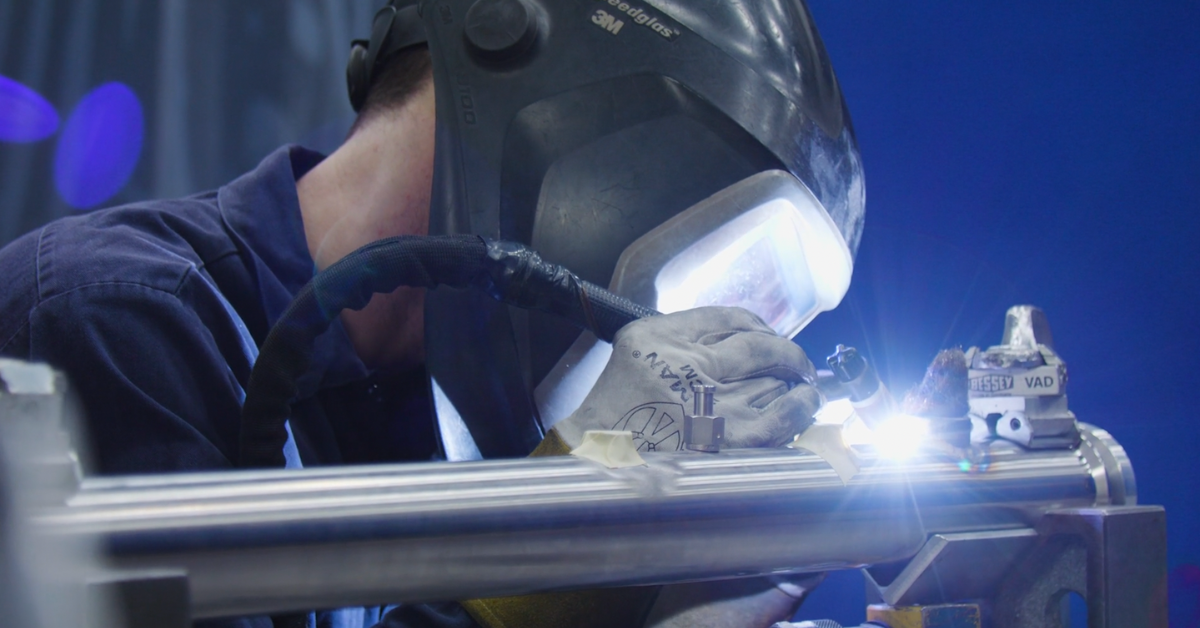
An equipment design-build partner manages the whole project on a single contract, providing specialized systems that are purpose-built for the customer’s application. Engaged at the project’s earliest stages, equipment design-builders leverage expertise from concept to commissioning. The design-builder takes responsibility for the entire scope, ensuring quality results with products that have been created with the customer’s specific processes in mind at every stage of development. Key benefits of choosing a design-builder for your equipment fabrication include:
- Extensive design and in-field experience
- Deep knowledge of industry requirements
- Reduced risks on cost and schedule
- Single contract for complete scope of work
- Higher quality and efficiency
- Longer lifespan with greater ease of maintenance
- Factory acceptance testing (FAT) to validate performance
- Documentation for industry compliance
- Continued technical support after commissioning
An equipment design-build partner that can verify the equipment will perform as needed is critical for project success. “By using a combination of computer simulations and physical testing, we ensure that the customer receives what they contracted us for,” says Frank Stenzel, business segment leader at Anderson Dahlen. This technology allows designers to customize performance parameters such as speed, ease of cleaning and servicing, and unit capacities for weight, temperature, pressure, etc.
Faster Commissioning with Custom Builds
For specialized equipment, partnering with a design-build team significantly minimizes project risk. When a design-build partner makes a component, piece of equipment, or turnkey system, they implement strict controls to stay on schedule and mitigate any issues that arise during installation or startup. But before the equipment ever arrives on site, the equipment fabricator can test functionality at the build location to ensure that it holds pressure, maintains the required rate, and meets other requirements before delivery.
This comprehensive testing and minimized risk are beneficial to brownfield projects where existing operations can’t be disrupted, as well as greenfield projects where commissioning multiple process skids on site could delay the start of production.
“If it’s already built and tested, all they need to do is anchor it in place and bring in power or utility,” says Brad Vos, director of Design & Controls Engineering at AD Process Equipment. “With that high level of confidence that it’s going to work, you could get up and running in a day or two compared to a few weeks, which is a big advantage.”
Closer Collaboration with Design-Build Partners
With an equipment design-build partner, the design-builder takes responsibility for design and construction, working in collaboration with the project owner. Equipment design-build is a preferred option for various projects:
Unique requirements: In some instances, the desired equipment doesn’t exist from commercial equipment suppliers. An example of these unique requirements could be fitting into a tight space that won’t accommodate typical equipment or performance parameters that require non-standard equipment. The flexibility of design-build allows specialized features to be easily integrated to meet specific operational needs and integrate into the customer’s facility layout.
Proprietary processes: If a business has an innovative process that they don’t want competitors to have access to, an equipment design build partner will allow them to retain their intellectual property and protect confidentiality.
“We’ve had numerous occasions where the customer built a room for special equipment inside their facility to limit exposure because it’s the secret sauce of their process,” says Stenzel.
Many customers develop long-term partnerships with design-builders that understand their needs and deliver consistent, trustworthy results.
Capability needs: Start-ups and companies with process expertise but limited equipment design capabilities benefit significantly from access to seasoned design-build teams. The specialized engineering expertise that these teams bring to complex projects speeds prototype development and completion.
Greater Production Capacity for OEMs
For OEMs that have the design and configuration for turnkey equipment or components ready to be built, an equipment build partner widens their capabilities.
Specialized custom builds: For some specialized, made-to-order equipment, an OEM may not have the necessary cutting, welding, and machining capabilities. A contract manufacturer that provides fabrication, has experience building unique designs, delivers tight tolerance controls and offers quality certifications is an ideal partner.
Fast scalability for large projects: When demand for certain equipment quickly increases, a small shop may not be able to keep up with production demands. An equipment manufacturing partner that can dedicate an entire team to a project is in an ideal position to help OEMs complete large-scale projects.
Stronger process system engineering: Process systems also benefit from custom development. Liquid process skid systems are often customized due to the wide range of capacities and formulations that could be required. “The Kraft Mac & Cheese plant that we did uses 10 powder products and six liquid products that are batched and cooked together, then blended and spray-dried,” says Vos. “It’s a great example of our custom capabilities because it’s dry bulk material handling, liquid materials, and all the process systems in between.”
Learn more about this project.
Giving Processors a Leg Up, 365 Days a Year
By partnering with experienced design-build and process system fabricators, OEMs and businesses gain access to valuable engineering expertise and custom manufacturing and fabrication capabilities. Equipment and systems that work as promised, are up and running quickly, have comprehensive documentation, and are easily maintained can deliver results that translate directly to minimized risk and improved production efficiency—ongoing benefits that far outlast the lifespans of common commercial systems.
As market demands continue to evolve, the ability to quickly and successfully integrate customized equipment into large-scale industrial and manufacturing projects will prove to be a difference maker for expanding businesses seeking to maintain or gain market share.
Some opinions expressed in this article may be those of a contributing author and not necessarily Gray.
Related News & Insights
Distribution, Specialty Equipment
Equipment Manufacturing Trends for 2025
Industry, Opinion
Manufacturing
Gray, UBE C1 Chemicals America, Inc., and Cornerstone Energy Park Celebrate Groundbreaking for New Manufacturing Facility
Corporate News
February 26, 2025Manufacturing
Reverse, Revive, & Reshape: What Trump's Economic & Trade Policies Mean for Key U.S. Industries
Industry, Opinion