How 3D Printing Revolutionizes Manufacturing Operations
3D printing is a truly groundbreaking, disruptive technology that is having a massive impact on the future of manufacturing. New announcements are made almost daily—larger sizes, faster speeds, and an increasing number of materials including polymers, metal and steel alloys, ceramics, and porcelains. Patterns of living cells can even be 3D-printed on biodegradable lattices.
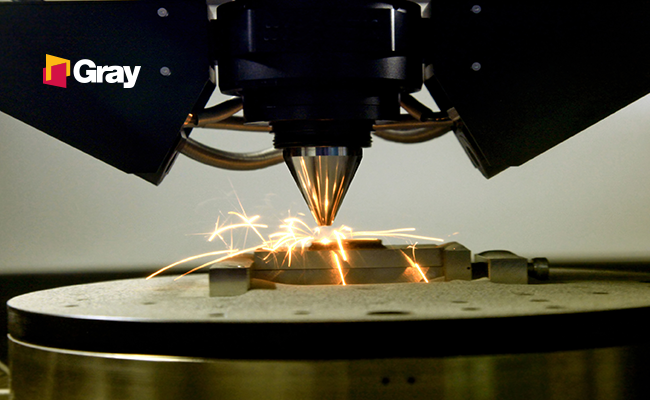
Companies that get the jump on 3D printing, and proactively invest in its potential, will reap the greatest rewards. They will stand out competitively and gain market share by finding ways to manufacture unique or innovative products, at lower cost, and quickly—sometimes in just a matter of days.
Take Caterpillar, for example. The heavy equipment company is investing in additive manufacturing (AM) and 3D printing through its unique AM Factory, a research facility that is packed with the latest AM equipment and tools, including 3D printing.
“Designing for AM is where we will see huge advances in manufacturing technology,” says Stacey DelVecchio, additive manufacturing product manager for Caterpillar in Mossville, Illinois. “Manufacturing companies have spent years training people to design for manufacturability. That means we have parts that are limited by how we traditionally manufacture them. At Caterpillar, we are removing these boundaries from our engineers. Having the capability to design what could never be made before, with features we didn’t think were feasible, is tremendously exciting.”
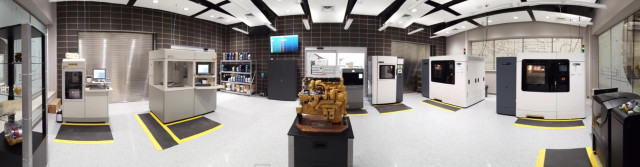
Improving supply chain management with 3D printing
However, the greatest potential for 3D printing is also the hardest to quantify—how this remarkable technology can open the mind to new applications beyond parts manufacturing. For example, when 3D printing is used in creative ways to manage the supply chain, it can have a big impact on operational costs and customer satisfaction.
Caterpillar recently shut down a transmission assembly plant until it could identify a problem with a transmission component, which was causing high warranty costs. It was decided the line could not be re-opened until a new tool was designed, ordered, and installed. “With traditional tool manufacturing, it would normally cost thousands of dollars and take weeks to get the line up again,” says DelVecchio. “Instead, the manufacturing engineer reached out to our AM team for ideas. We were able to print a two-piece plastic tool that night and drive it to the plant the next day. It worked immediately and the line was up and running again.”
“Tooling for manufacturing can be very expensive and time consuming,” agrees Mark Johnson, director of the Advanced Manufacturing Office (AMO) in the Office of Energy Efficiency and Renewable Energy. The AMO partners with private-sector companies, universities and research institutions to develop emerging technologies that have the potential to increase the global competitiveness of U.S. manufacturing and create high-quality manufacturing jobs at home—including 3D manufacturing.
“It can take up to 12 weeks to make a tool,” Johnson continues. “However, a 3D printer can turn out that tool in a single day. Printing parts on site is another way to shorten the supply chain and deliver the end product faster. Wind turbine blades, for example, are normally too big and expensive to ship. With 3D printing, they can potentially be made on site, saving time and money and speeding up construction.”
Moving forward
It can be difficult to get corporate buy-in for investing in a new technology. This is where decision-makers need to take the time to fully understand how the technology could impact the long-term future of the company (and the industry) and then, if the decision is to move forward, invest the necessary resources to be at the forefront of that technology.
“While this may sound simple, it can be incredibly difficult to do, especially in tough financial times or if a company has a lot of strict processes,” adds DelVecchio. “The key is investing in these technologies at the appropriate level for your company, and finding a leader who will champion the work.”
Mark Crawford is a Madison, Wisconsin-based freelance writer who specializes in business, science, technology, and manufacturing.
- Category:
- Industry
- Manufacturing
Some opinions expressed in this article may be those of a contributing author and not necessarily Gray.