Five Technologies that Will Transform Manufacturing in 2016
Globally, what are the most promising, attractive and impactful technologies to watch next year? Chief technology officers (CTOs), chief research officers (CROs), chief executive officers (CEOs) and company presidents from various manufacturing sectors, shared their views as part of the Manufacturing Competitiveness Initiative led by Deloitte Touche Tohmatsu Limited and the Council on Competitiveness. Leaders interviewed came from firms such as ABB, Kraft, Deere & Company, Dow Chemical Company, PepsiCo, Ford Motor Company, General Electric, IBM and Lockheed Martin Corporation.
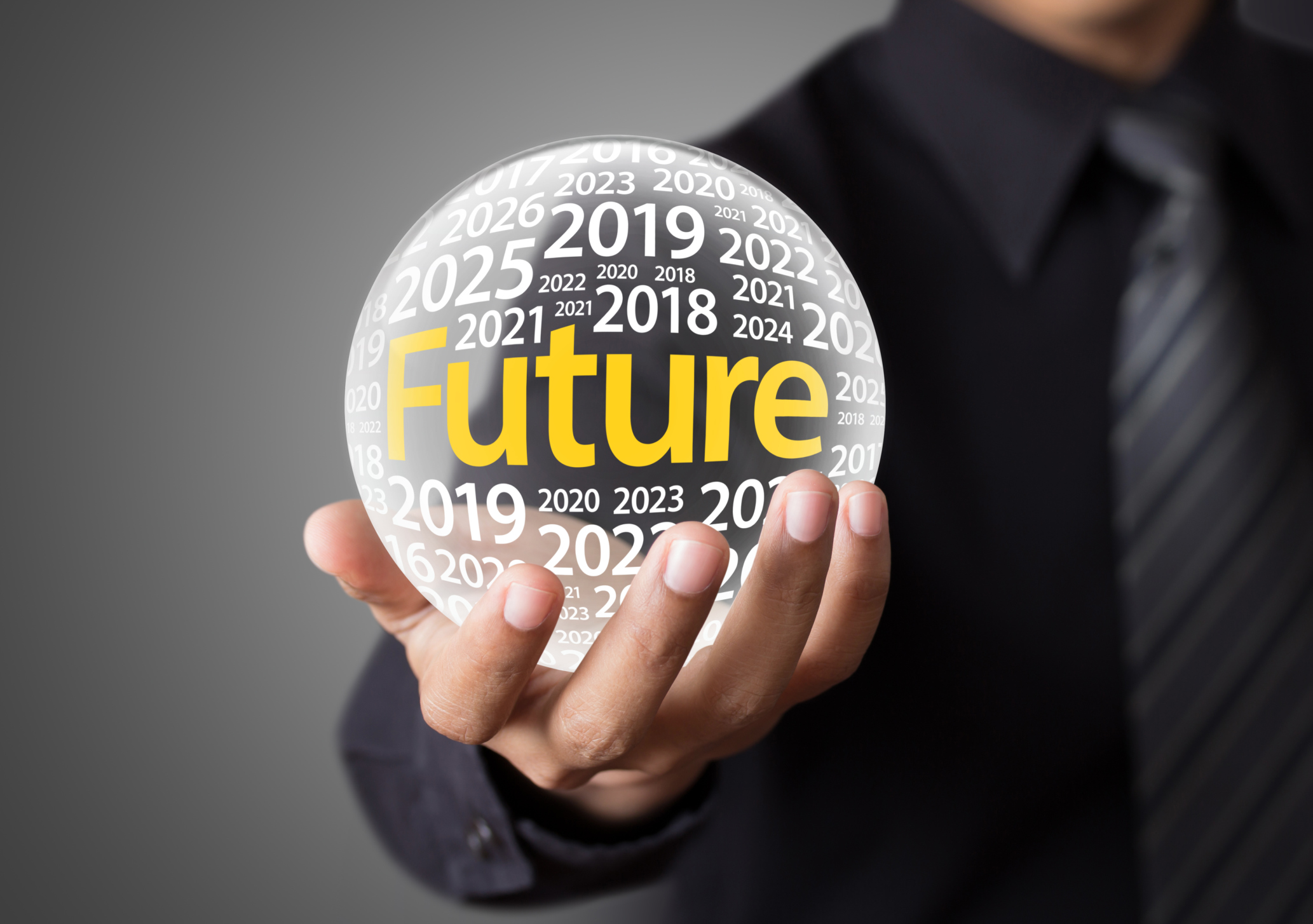
Five interdependent and synergistic trends to watch are:
- Predictive analytics include a growing range of digital methods that manipulate large masses of data to develop mathematical models that can be used to simulate outcomes of complex processes. In manufacturing, they are becoming competitive advantages for continuously improving quality, production scheduling, problem solving and supply chain optimization, among other uses. Working in real time, they are enabling manufacturers to anticipate challenges and initiate actions before they emerge into full-blown problems.
- The Internet-of-Things (IoT) connects objects and machines into a digital network using sensors, vision systems, and advanced software. Smart, connected products, smart factories and smart distribution systems are intelligently linked together, allowing manufacturers to improve efficiency, reduce waste and increase profits. Outside of manufacturing, the IoT promises to transform vehicular traffic and parking management as it also makes cars and trucks safer.
- Advanced materials encompass new metal alloys, advanced ceramics and composites and critical materials. In metals, research is continuously turning out new lightweight and high-strength alloys especially useful in increasing fuel efficiency in vehicles. Other high-performance alloys are helping to develop new turbines for aircraft and power generation. In aircraft and automotive industries, advanced composites are making lighter and stronger structural parts, not to mention better golf clubs and faster bicycles. Advanced ceramics are enabling the IoT by improving sensor technology. They are also being used in high-heat conditions such as automotive engines. Critical materials such as neodymium and platinum are used in magnets, catalytic converters, LEDs, semiconductors and other technologies. New bio-based polymers are replacing petroleum-based materials in many products and industries.
- Digital design, simulation and integration use software and computers to create virtual prototypes and process simulations that can accomplish sophisticated testing and development before physical products or processes are built. The systems can be used for finding potential defects, failure points and manufacturability problems. They also enables “what-if” thinking that can test innovative ideas quickly and early in the design process.
- High performance computing is an enabler of other new technologies. These systems typically function above a teraflop (10 to the 12th power floating-point operations per second). That allows computing with the speed and capacity that allow predictive analytics, the IoT, digital design and simulation to be realized.
Things for Manufacturers to Consider When Adopting New Technologies
When it comes to using new technologies to take your company into the future, Deloitte and the Council on Competitiveness offer some advice:
- Adopt calculated risk-taking strategies. Although they entail high risks of failure, well-considered use of such new technologies may produce transformative innovations. The risk of not taking risk is to lose out to firms that innovate continuously and gain experience from failures.
- Capitalize on short-term innovation but don’t neglect the long term. Companies can adopt technologies such as predictive analytics or digital design relatively quickly for immediate benefits. At the same time, long-term R&D investments can result in transformational gains.
- Combine multiple technologies rather than focusing on a single enabler of innovation.
- Look beyond innovation in product design alone. Apply new technologies and transformational thinking to business and operations processes and systems.
- Be clear about your aims and align your approach, organizational structure, competencies, and incentives to pursue your strategic goals.
- Collaborate in an innovation ecosystem, which could include cross-industry joint ventures with other companies, or universities and national labs.
The pace and intensity of competition is increasing relentlessly. To remain globally competitive, manufacturing leaders must inform themselves of fast-changing opportunities for innovation and strategically employ new technologies.
Karen Wilhelm has worked in the manufacturing industry for 25 years, and blogs at Lean Reflections, which has been named as one of the top ten lean blogs on the web.
- Category:
- Industry
- Manufacturing
Some opinions expressed in this article may be those of a contributing author and not necessarily Gray.