EPMC™: Building on a Foundation of Trust
Engineering, Procurement, Manufacturing, and Construction — otherwise known as EPMC™️ — adds manufacturing of components and equipment to the traditional EPC model of construction projects.
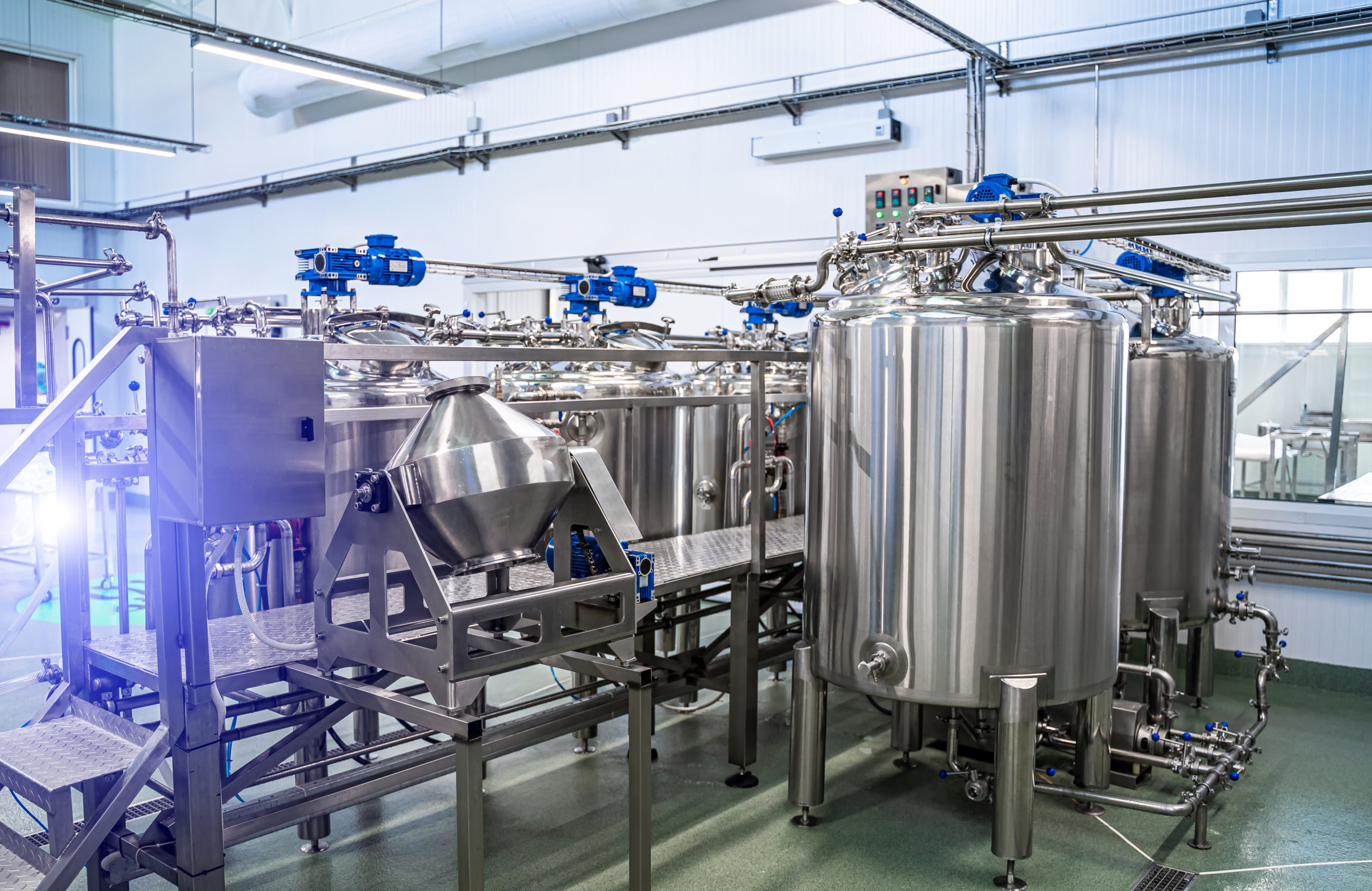
But what does that mean in practice? How does adding manufacturing to the model change expectations, deliverables, and the process of a project? And, perhaps most importantly, is EPMC™️ the right model for every project?
All those questions are significant pieces to the EPMC™️ puzzle. It is a significant departure from the EPC model, even if it only seems like adding one additional step. That additional step changes the calculus in a number of ways, and understanding how EPMC™️ does — and does not — work in practice is critical to deciding when, how, and why it should be used.
“EPMC™️ allows additional freedoms that are not usually seen in a typical EPC project,” says Paul Kornman, senior project manager at Gray. “EPC is a great project delivery method, but there are times that it can inhibit further ‘out of the box thinking’ and keep the design and process within the guardrails of what’s available by vendors.”
EPMC™️ is a flexible project approach where various solutions can be realized depending on the processor’s specific needs. This approach and its flexibility is highly dependent on our ability to provide comprehensive services and equipment products, with our own experts and infrastructure, that are delivered in a variety of ways. A fully integrated, “turnkey” approach might not always be the right fit for a customer, and EPMC™️ can be delivered in a variety of scenarios ranging from fully-integrated to hybrid to an a-la-cart, discrete, service.
The parameters of each project will determine whether EPMC™️ is the right fit, how it can be successfully implemented, and what the “M” piece needs to take into account.
The Process
What variation of EPMC™️ is the right tool for the job starts with a simple step, says Kornman: Listening to the customer. By understanding what their equipment needs are and how they can be met, project managers can then determine whether integrating equipment design and manufacturing into the process is the right decision.
“There are instances where a particular vendor is preferred and meets every need of the customer,” says Kornman. “Proper vetting of the equipment vendor’s capabilities, paired with the schedule milestones the customer requires, will quickly expose if another delivery method is needed. However, if cost or schedule become a constraint, having the EMPC™️ delivery method available keeps the conversation going and brings solutions to the customer otherwise not accessible.”
In some cases, customers have pre-existing equipment vendor relationships, and those vendors are the preferred choice for various equipment needs. In those scenarios our project managers and engineers work collaboratively with those vendors and the customer to appropriately procure and implement those systems. However, we will also identify the needs where a preferred vendor relationship may not already exist, and we will assess the equipment needs wholistically utilizing outside vendors as well as our own equipment manufacturing resources where applicable.
But if there is not a preferred vendor or the vendor cannot deliver what is needed for the project for some reason, then a more robust version EMPC™️ becomes a viable option. Especially on a tight schedule, EMPC™️ can help ensure equipment is specified, manufactured, and installed to the customer’s satisfaction, and integrating it into the overall design-build process helps keep the project on track and the lines of communication open.
“The advantage to M in the EMPC™️ model is better communication and coordination earlier in the project,” says Zach Becks, manager, AE Integration, food & beverage, Gray AE. “Better communication and coordination will result in improved quality, increased creativity and problem solving, and better opportunities to positively impact project schedule and cost.”
As Becks says, the key to a successful EMPC™️ project is that it allows for a more streamlined communications process. While project managers have plenty of experience working with outside vendors for equipment, communication breakdowns happen, especially when you have multiple companies all communicating with each other. If manufacturing is done by a company under the same umbrella as the design-build team, it helps avoid some of those breakdowns and ensures that the whole team is on the same page.
“One struggle project teams face is when the holistic team is not engaged or is brought too late in the project,” says Becks.
While EMPC™️ won’t magically solve that challenge by itself, it helps break down silos and ensure that the entire team is on the same page in each step of the process instead of having to chase down key contacts or have multiple points of contact for each separate piece of a production line.
Laying the Groundwork
As Becks says, engaging the holistic team early on is key to successful project completion. That means additional planning up front to ensure that each team is informed on what is needed when, as well as how the workflow should be sequenced to ensure each stage of the project is completed when it needs to be.
Consider the challenge of designing a food & beverage plant. The building itself is one aspect of the design, but then it also needs infrastructure to support process equipment. It also needs power, water, pipe runs, maintenance access, cleaning access, material flow paths, and countless other elements to work in unison efficiently and effectively. If the critical aspect of specialty equipment manufacturing is is considered inthe EPC or design-build process as an afterthought, then it’s either going to slow down the overall process or could cause manufacturing to get out of sequence with design and construction. This can lead to a longer process for getting the plant up and running, which ultimately leads to cost overruns.
So, if the fully integrated version of EMPC™️ is going to be used, it has to be used from the start. Building the manufacturing piece into the process from the beginning allows for the full potential of EMPC™️ to be realized.
“A true EMPC™️, where it is fully in-house, results in a smooth transition between phases of design and construction,” says Kornman. “Moreover, you’re able to capture the scope gaps that often add costs to a project during execution.”
The Benefits of EPMC™️
When EPMC™️ is considered, food manufacturers will see an outcome-based approach that is fully comprehensive, fully flexible, and deliberately programmed for each level of integration that maximizes critical abilities.
The first is the ability to custom-build equipment to meet exact needs. While some processors have relationships with equipment vendors that allow for specialized equipment, many do not, especially if they are a small or mid-size processor. Their options for equipment may be limited to off-the-shelf offerings from equipment manufacturers, which may meet most of their needs, but not all.
“There are times where being shoe-horned into a piece of equipment because there isn’t a model between sizes, or into a building because a series of tanks wouldn’t fit into a smaller footprint, can be the determining factor of growth or settling for another year of flat returns while losing valuable market share,” says Kornman.
EPMC™️ meets those challenges by allowing for the customer to specify exactly what it needs, then building to meet all those specifications instead of 90% of them.
Another advantage is reduced risk for customers. As previously mentioned, multiple points of contact can mean multiple points of failure, and that can slow down projects or lead to costly overruns. By having a single point of contact for all aspects of a construction process, customers gain better and faster communication, a closer working relationship and the ability to manage the process more closely to ensure needs will be met.
The introduction of Industry 4.0 technologies to the equipment design process is a hot topic in the food & beverage industry. The one-partner/one-team advantage puts EPMC™️ at the cutting edge where physical fabrication meets the digital world. Our digital and automation team of nearly 350 team-members collaborates with our more than 300 team-members in equipment manufacturing to solve the challenges of tomorrow. This cohesive team leverages the latest automation applications and manufacturing knowhow to deliver “smart” equipment possibilities to the industry.
EPMC™️ can have an application for any project with low to high levels of integration, and implementing it adds in more up-front work to ensure it is used to its full potential. When it is used, the advantages it offers are substantial, and it provides better outcomes for customers throughout the entire process.
Some opinions expressed in this article may be those of a contributing author and not necessarily Gray.
Related News & Insights
Food & Beverage, Engineering
How EPMC™ is Changing the Food & Beverage Industry
Industry
Food & Beverage
Gray and Maruchan Celebrate Groundbreaking for New Facility
Corporate News
December 18, 2024Food & Beverage
Gray Project Receives Manufacturing Innovation Award
Corporate News, Industry
December 04, 2024