Digital Technologies Expected to Dominate Manufacturing Trends in 2020
Although most manufacturers are cautiously optimistic about 2020, concerns linger about the potential impacts of trade volatility, tariffs and the global manufacturing slowdown. Other factors that could impact profits next year are rising material costs, price-reduction pressures as well as labor availability and labor costs.
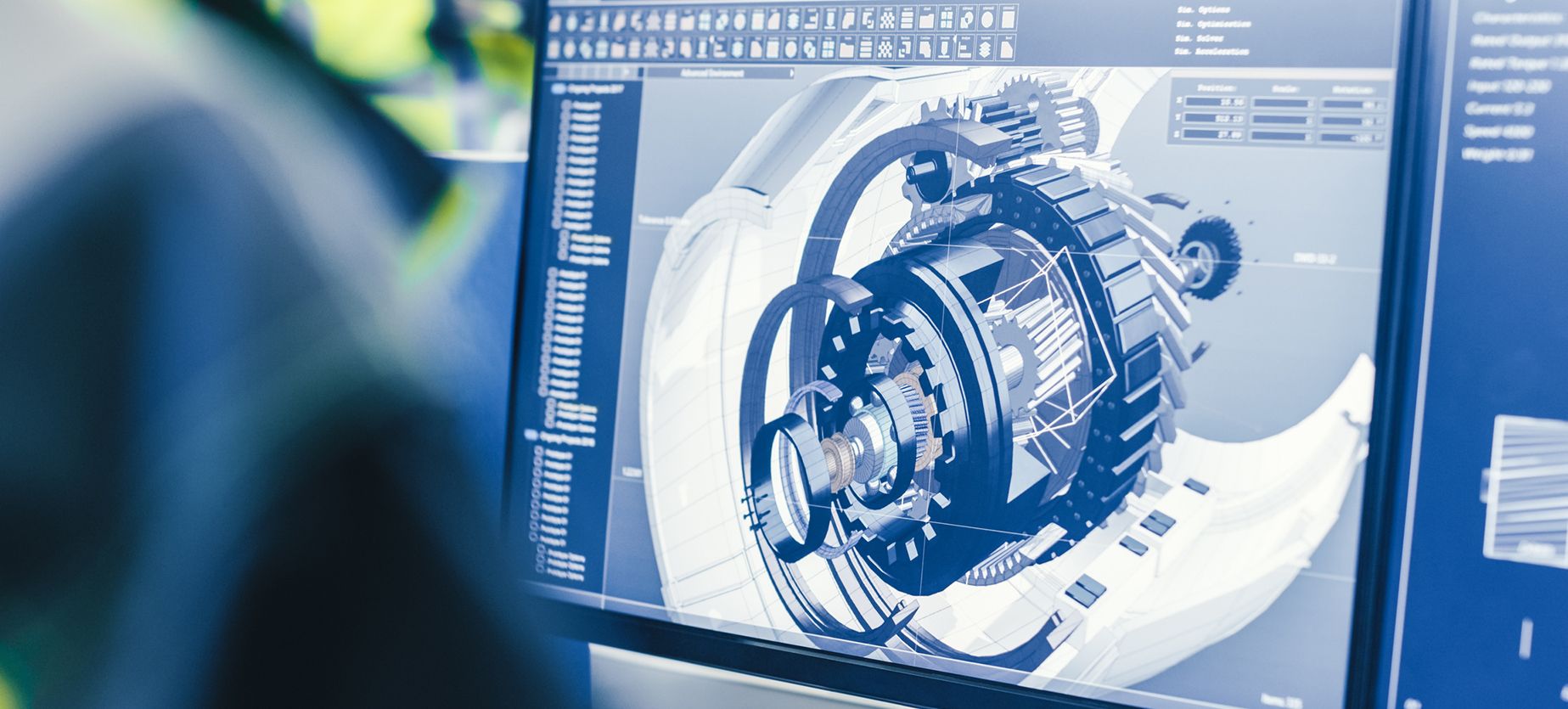
The best way to prepare for these potential threats is to optimize the manufacturing process by increasing efficiencies, reducing operational costs and speeding up time to market. Strengthening customer relationships is also critical for growing businesses and building loyalty, through methods such as customized products, especially if economic hardships strike. Therefore, more manufacturers are investing in Industry 4.0 technologies to better manage product lifecycles, streamline operations and provide superior customer support.
The following seven areas are ways manufacturers can use technology to optimize their operations in 2020.
1. Customer-centric manufacturing
Knowing what customers like and don’t like is essential for a thriving business. Seeking customer feedback can improve product development and build customer loyalty. Price Waterhouse Coopers recommends that manufacturers use analytics and Industry 4.0 technologies to deepen relationships with customers, including adding value through customization. The automobile company Mini Cooper capitalizes on this tactic by using customer studies to add high-demand features and provide more than 800 varieties of its vehicles that can be configured and ordered online.
2. Artificial intelligence and machine learning
Artificial intelligence (AI) continues to play an expanding role in manufacturing. A greater variety of performance data can be used to create smarter systems and models for all aspects of an operation, including supply chain management. AI and machine learning are vital for optimizing speed, scale and convenience—for example, eliminating the need to assign entire groups of workers to designated tasks. “With these systems, it is possible to reduce significantly the time needed to learn manual operation skills, reducing the time invested in jobs that could last up to several years to a mere fraction,” states Kitmondo, a seller of manufacturing equipment.
3. 5G and smart manufacturing
Fifth-generation (5G) technology will provide manufacturing companies with faster connections that enhance both business-to-business and customer relationships. 5G will improve latency, bandwidth and reliable real-time communication. “With 5G, manufacturers can begin to increase their use of senor, cloud, centralized tracking, quality inspection and other systems, forming an ‘ecosystem’ of smart manufacturing,” says Kim Figor, director of marketing for the Directive Group, a digital marketing agency that works with manufacturers. Although there may be a growing disparity between 5G haves and have-nots in 2020, she notes, 5G will still have a larger role in smart manufacturing moving forward.
4. Predictive maintenance
With the growing innovations in AI and machine learning, sensor technologies, connectivity and data analytics, it is now possible to monitor equipment in real time and analyze key performance metrics. This makes it easier for manufacturers to understand in greater detail how their systems and processes work. When even the slightest variances are observed, adjustments can be made that help prevent untimely equipment breakdowns, saving valuable time, resources and money. According to Information Technology Intelligence Consulting, 98% of organizations say a single hour of downtime costs more than $100,000.
5. More robotics
Automation and robotics are a cornerstone for Industry 4.0 and the Internet of Things. With AI, robots can evolve on the job, constantly learning how to do their tasks better. Robot manufacturers are making robots of different sizes that are more functional and can be customized for specific jobs—these include “cobots” that can work safely beside human workers. Many robots are designed for material handling, not only to speed up the process but also protect workers from injury. Some heavy-duty robotic arms can lift more than two tons of weight.
6. Additive manufacturing and 3D printing
There is no doubt that additive manufacturing/3D printing (AM/3DP) is already having a disruptive impact on the manufacturing industry. This new technology allows engineers to design innovative products that cannot be made with traditional machining methods. Highly customized products can also be manufactured with AM/3DP. Many of today’s medical implants and prosthetics are made with specific patient needs in mind using medical imaging scans. AM/3DP is also used during the design process to make prototypes in a matter of minutes, greatly accelerating product development. These technologies are also used to manufacture parts in-house for the manufacturing and machining equipment, such as fixtures and tools.
7. Industrial wearables
IndustryWeek predicts that the most effective workers of the next decade will utilize wearable tools and equipment such as smart glasses and biometric sensors that connect them to not only work instructions or critical data, but to each other to create the, “Industrial Internet of People.” The report specifically sites two new wearables already being utilized within the industry to help streamline workflows and increase productivity. “For example, a Microsoft HoloLens can dial up a remote expert for a repair job and Google Glass can record assembly procedure videos and then play them back for new trainees.” On a larger scale, robotic exoskeletons that people wear for extra strength or support continue to advance. Sarcos Robotics has developed an exoskeleton that give wearers a 20-to-1 strength amplification—to a person wearing this robot and lifting 100 pounds, the load should only feel like five pounds.
Industry 4.0 and the Internet of Things continue to transform how manufacturing companies and their supply chains do business. As these trends and technology continue to evolve, processes will become faster, more accurate and less costly. Product quality will be higher, with greater output and less rework. New products will be more customer-centric, thereby increasing customer loyalty and market share.
2020 is set to be a year full of changes and transitions, but by using new technologies to optimize operations, maximize quality and reduce costs, manufacturers will be well-positioned to face whatever comes their way, and still add value for customers in new and innovative ways.
Some opinions expressed in this article may be those of a contributing author and not necessarily Gray.