COVID-19-Driven Supply Chain Uncertainties Will Carry into 2022
In 2020, the COVID-19 pandemic shut down manufacturers and crippled global supply chains. Chinese manufacturing operations were the first to close, soon followed by other manufacturing companies around the world. These closures also greatly impacted the logistics and distribution industry.
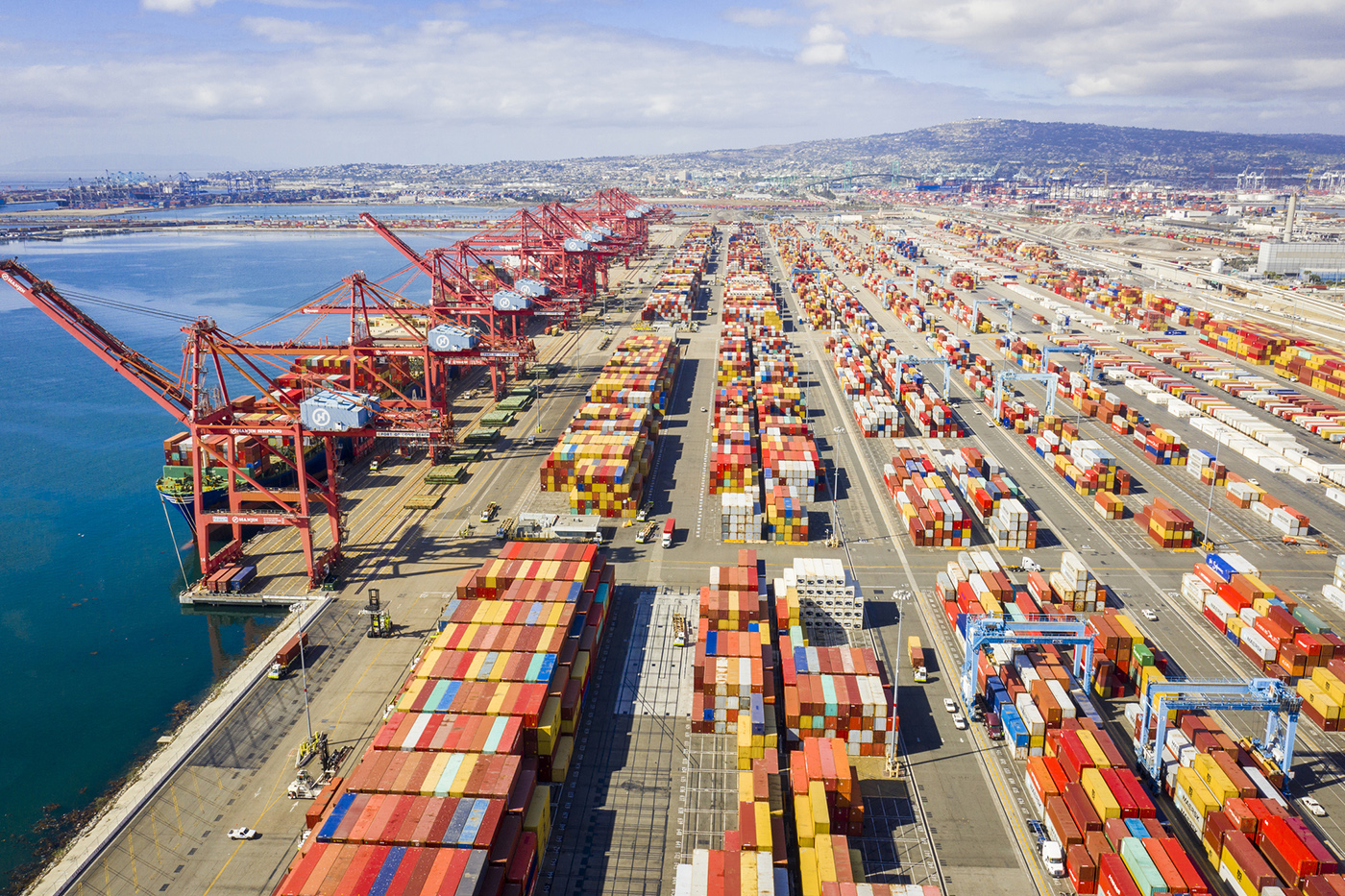
Producers cut back on inventory volumes and orders for materials and parts when consumers stopped spending. After a brief downturn, however, manufacturers were surprised when consumers shifted to online buying, which raised demand for home products, electronics, appliances, and construction materials for home-improvement projects.
This upturn led to a spending surge that caught manufacturers and their suppliers by surprise. Today, “ports, warehouses, and trucking companies are processing more goods than ever while combating a series of crushing shortages, including workers, equipment, and space,” states BusinessInsider.com. “The national labor shortage has left warehouse companies scrambling for employees and key U.S. ports working with limited manpower. Two of the largest U.S. ports saw a 30% increase in the amount of goods going through them while processing the cargo with 28% fewer workers.”
Supply chains are, in essence, facing an ongoing “perfect storm” of economic blows.
“We might be able to buffer against one type of risk or two types of risk, but it’s the fact that all these challenges are happening at the same time,” says Nicole DeHoratius, an adjunct professor of operations management at the University of Chicago’s Booth School of Business.
Shortages Everywhere
According to Bloomberg, supply indexes show shortages just off a 20-year high in the U.S. Indicators for the UK and EU area are similarly elevated. Supply chain bottlenecks are causing record shortages of various products, ranging from household goods and electronics to cars, food, and raw materials. The motor vehicle industry has been hit especially hard by global semiconductor shortages. Some companies have responded to shortages by ordering extra parts and products, which adds to the strains on the ports and warehouses.
The manufacturing index from the Institute for Supply Management (ISM) slipped 0.3 points to 60.8 in October 2021, the result of an impaired supply chain. The index is a monthly indicator of U.S. manufacturing activity, which “slowed in October, with all industries reporting record-long lead times for raw materials, indicating that stretched supply chains continued to constrain economic activity early in the fourth quarter, Reuters states.
Major global companies have cited concerns about supply chain integrity. For example, Toyota has cut production by about one-third and Apple reports a loss of $6 billion in sales due to inability to meet demand. These uncertainties are increasing prices on products; inflation may also trigger interest-rate hikes, which could be especially damaging to the equity and real-estate markets.
Fixing the Supply Chain
The factors that impact the supply chains are unique because both supply and demand are involved.
“At this point, shortages are guaranteed,” says Jonathan Gold, vice president of supply chain policy at the National Retail Federation (NRF). “We’ve been warning consumers to manage their expectations for the holiday shopping season for months now. The fact of the matter is the supply chain is stretched to its limit from end to end.”
In all likelihood, the solution will be simply riding it out. It could take more than a year for the supply chain to work through its backlog and settle into a relatively normal pattern. Some businesses are unwilling to wait—for example, Walmart is chartering its own ships to move cargo.
President Joe Biden recently revealed plans to help tackle bottlenecks within the U.S. supply chain, including the idea of turning ports into 24/7 operations, where workers will take extra shifts to keep operations open nonstop. “This is the first key step for moving our entire freight transportation and logistical supply chain nationwide to a 24/7 system,” says Biden.
At the company level, being agile is still the key to getting the most out of the supply chain. “Investments in people, processes, and technology that can improve end-to-end visibility within the supply chain must be top of mind for organizations,” advises Hank Canitz, vice president of industry solutions for Nulogy, a provider of agile supply chain software solutions
However, he points out, most industry 4.0 investments in supply chain capabilities have been focused on internal operations—”leaving the external network woefully unprepared for a massive uptick in volumes,” he adds. “To overcome these challenges and ensure they do not have the same issues in the future, manufacturers need to prioritize end-to-end supply chain data visibility and partner collaboration to improve overall agility and resilience. Having more insight into their operations and making more informed decisions for orders and capacity planning is critical to operational success.”
Some opinions expressed in this article may be those of a contributing author and not necessarily Gray.
Related News & Insights
Advanced Technology
The Opportunities and Challenges of a Second Trump Presidency
Opinion
Advanced Technology, Automation & Controls
Four Use Cases for AI's Growing Role in Manufacturing
Industry
November 25, 2024Data Centers
Gray Expands Reach with Dallas Office
Corporate News
November 14, 2024