Building from Within: Domestic Supply Chains to Power U.S. Manufacturing
President Biden recently noted that investing in U.S. supply chains is a top priority for American manufacturing industries. “To build a strong economy, we need a future that’s made in America,” he said. “That means using projects, parts, and materials right here in the United States of America. It means bringing manufacturing back, jobs back, building the supply chain here at home and not outsourcing abroad.”
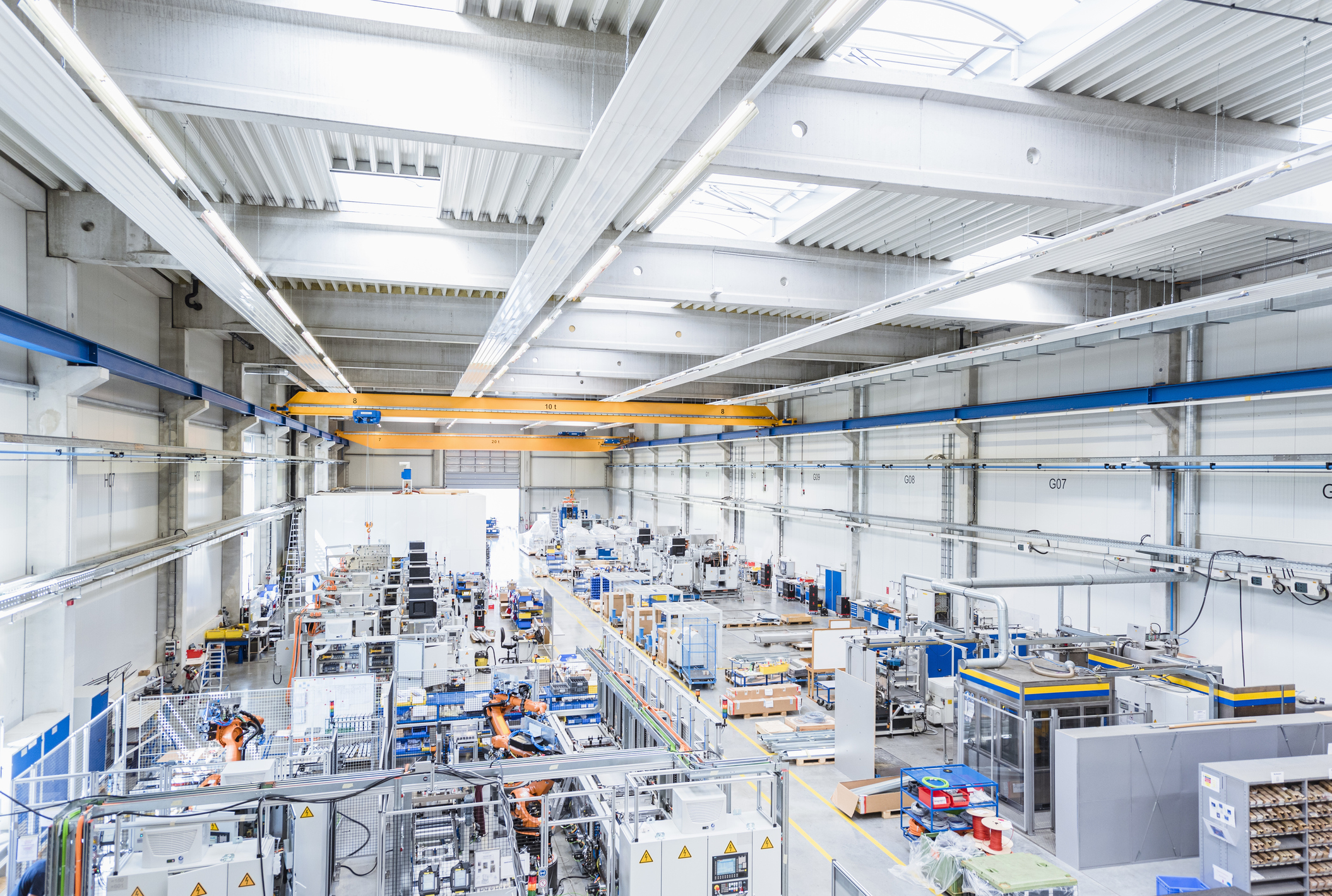
In other words, domestic supply chains for U.S. manufacturers.
It can seem like a daunting (or even impossible) task to totally reshore supply chains to the U.S., relying only on domestic sources. And although there are some major challenges to building a domestic supply chain, these can be tamed (at least in part) with some collaborative innovation, investment, creativity, and redundancy.
Domestic Advantages
Advantages to a domestic supply chain include:
- Reduced supply chain costs. One of the biggest savings for companies that reshore is lower transportation costs, as well as the elimination of extra taxes, currency exchanges, and import fees.
- Greater flexibility. Domestic suppliers can often be more agile compared to foreign sources. Communication is also easier and order changes can be made more quickly.
- Improved quality control. Manufacturing and certification standards are expected for U.S. suppliers and help ensure higher levels of quality control. Working with domestic suppliers also improves efficiency and quality by having fewer language barriers and sharing the similar time zones/operational hours.
- Improved inventory control. An ongoing challenge for many manufacturers is inventory control. Forecasting can be difficult, especially when relying on foreign suppliers. Customers want their orders fulfilled immediately—using local or domestic suppliers makes it easier to maintain just-in-time inventories, which reduces inventory costs.
Developing the Supply Chain Edge
One of the first considerations for building a domestic supply chain is understanding the capabilities of local suppliers, including their ability to expand capacity if and when needed. Although these capabilities may not be everything a manufacturer wants, suppliers may be open to converting their operations to expand business and produce new lines.
If local companies do not have all the capabilities a manufacturer is looking for, they can be developed with the help of the manufacturer, noted Jonathan Webb, director of strategy research for Procurement Leaders, a provider of market intelligence for a variety of industries. “This is known as supplier development,” he said. “There are two options available to manufacturers. First, they can provide technical assistance to suppliers to support their expansion and development of new capabilities. Second, they can encourage suppliers to merge with others in order to increase their ability to produce scale. There is no reason why a company cannot deploy the same approach to bringing together a collection of smaller suppliers to forge a consortium to match the shortfall created by the shortened supply chain.”
Investing in automation is absolutely essential for domestic manufacturers for supply chains to be cost-competitive with global supply chains that operate from lower-cost countries. Domestic suppliers that automate have lower operational costs and get products to market faster relative to those who don’t utilize the power of automation. If a company finds a good domestic supplier that is not automated, another available option is for the manufacturer to share in the cost of automating the necessary equipment.
Another option is to internalize supply chain capabilities directly into the business. “This involves acquiring a supplier,” said Webb. “However, savvy organizations can look to see where local companies, who may not have developed the precise solution to match the need, may be open to direct intervention as part of a new corporate entity.”
Every Domestic Partner Helps
The COVID-19 pandemic proved the importance of redundancy in the supply chain. It takes time to build relationships and understand the needs of domestic partners. Making the decision to reshore is usually not an easy one. A valuable resource for companies looking to reshore is the Reshoring Initative, an organization that helps manufacturers decide whether domestic manufacturing and supply chains can reduce their total cost of ownership enough make the move profitable.
“The decision must be based on total cost of ownership, not price or landed cost,” said president and founder Harry Moser. “Our data show that about 25% of work is reshorable with no impact on profit.”
If it is not feasible to reshore an entire supply chain, bring back as much of it as possible for domestic sourcing. A manufactured component is a good candidate for domestic production if it:
- Comes from China or Taiwan
- Has a high material or freight cost versus labor cost
- Can be easily automated
- Is not tooling intense (for example, machined, not stamped or molded)
Other considerations are type of material (plastic is generally attractive for reshoring because it is globally competitive in cost), energy usage, seasonal demands, or Made-in-America label for brand purposes.
“Domestic sources for finding suppliers are Thomas/Xometry, trade associations, and the Reshoring Initiative,” said Moser. “Also, if you decide to reshore in some capacity, make sure to build up an inventory before shifting—foreign suppliers may cut you off.”
This decision to shift from the more traditional supply chain approach to today’s proposed domestically driven model certainly isn’t an easy one. In most, if not every case, you are leaving behind decades of best practices, relationships, and solid returns on investment for the promise of a better future. But that better future really is a better future. With promised incentives and a structure that is built to facilitate and maintain growth, a framework is in place to propel companies past previous high-water marks. The proper alignment of a local, regional, and national partner networks provide the flexibility and feasibility to excel in today’s evolving markets.
- Category:
- GrayWay
- Manufacturing
Some opinions expressed in this article may be those of a contributing author and not necessarily Gray.
Related News & Insights
Advanced Technology, Automation & Controls
Four Use Cases for AI's Growing Role in Manufacturing
Industry
November 25, 2024Data Centers
Gray Expands Reach with Dallas Office
Corporate News
November 14, 2024Manufacturing, Construction
The Evolving Role of Electric Vehicles in Sustainable Construction & Design
Industry
October 18, 2024