The Problem with Manufacturing Conveyor Systems
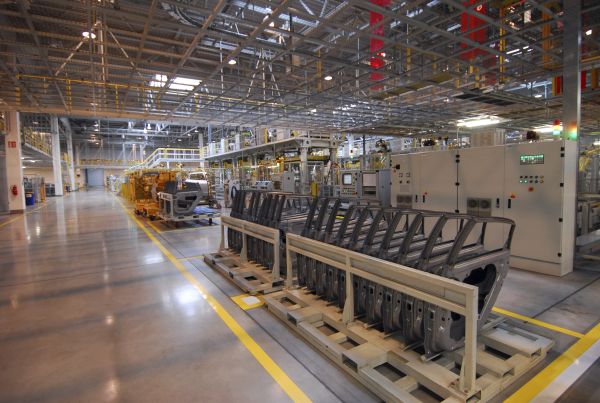
Anyone studying lean knows that the Seven Wastes include the waste of transportation. Even so, in most manufacturing processes, things do have to be moved from one place to another — often by conveyor systems that are too big, too inflexible, and too prone to breakdowns.
Legacy conveyors in your plant are there because engineers determined that they would be the most efficient and least costly way to move parts and finished goods — based on analytical methods of the past. In actual plant operations, however, a large conveyor system may not be very cost-effective or efficient. Conveyors take up space, require maintenance, hide inventory, damage product, and reduce flexibility.
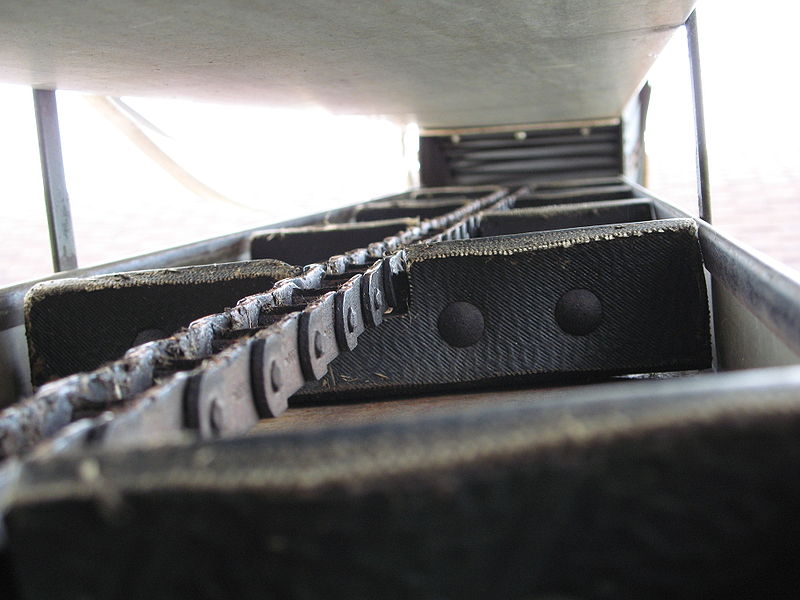
One of the principles of lean is to connect process steps. Often they are located far apart, again, due to what were thought to be the best engineering methods at the time. To make the process more efficient by reducing the time and distance products must travel, you want to move work stations and part supply points closer together. When a large conveyor system separates process operations, making that move becomes difficult or impossible to do.
In a lean manufacturing system, manufacturing multiple products in one line or cell requires flexible systems that can be reconfigured easily. Achieving new product velocity is a competitive advantage so you want manufacturing systems that can adapt quickly to engineering changes and new model introductions. Unfortunately, large legacy conveyor systems can’t be moved around easily.
Conveyors also require maintenance. This includes monitoring, regularly scheduled maintenance tasks, and routine replacement of fluids and parts. When a conveyor goes down, trained technicians must be available, because the costs of downtime and maintenance hours stack up. The longer and more complex the conveyor lines are, the probability of failure increases, and you may be hiring more technicians than engineers expected when they recommended investing in the equipment.
That’s not to say that you should never have a conveyor system. A conveyor may be perfect for moving parts or ingredients through a timed cleaning, heating, or cooling period. And not all conveyor systems are large and complex. Smaller, more modular units that can be easily reconfigured may be right for today and adaptable for tomorrow.
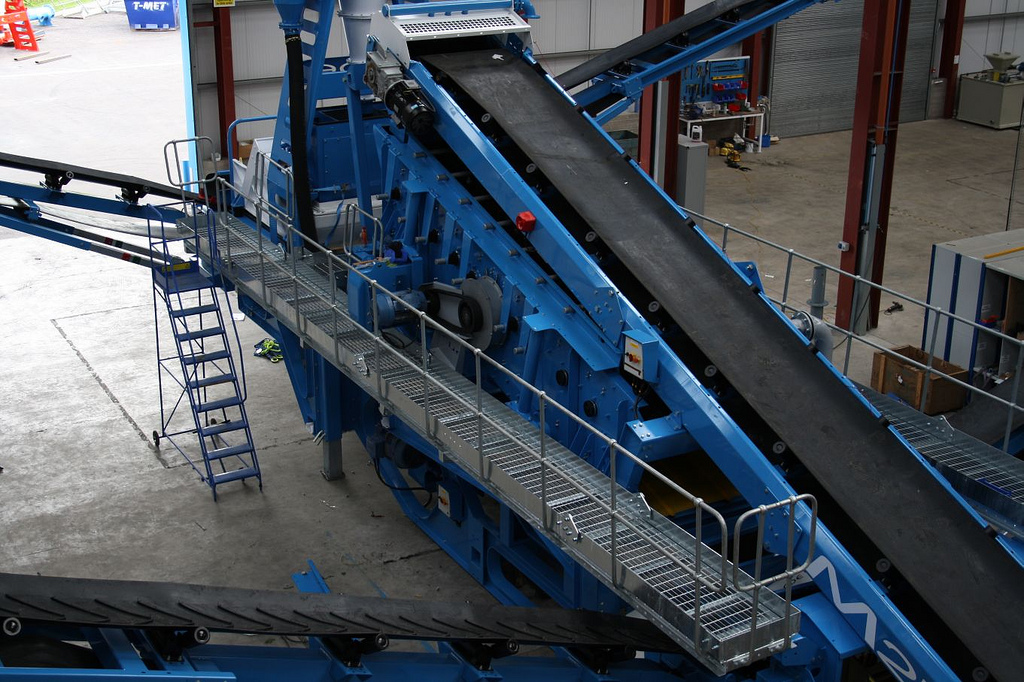
So, the next time you are out in the plant, stand back and look at your overall conveyor installation from a more skeptical point of view. How much visual space does the system take up? How is process visibility obscured? What do you guess their total length is? Ask your maintenance manager how much time technicians spent working on conveyor problems and routine upkeep last month.
If you start seeing disadvantages, you may want your engineers and production teams to think about change — for the better. They can see alternatives by visiting plants known for being lean. They should be asking vendors about how their equipment line has changed for a lean world, and be prepared to walk away if they don’t have a good answer. Think small. Visit trade shows with a different set of goals, and avoid those dazzling grand constructions.
Moving goods through the plant can be accomplished in many ways. Sometimes conveyor systems add up to too much automation. A year from now, how will they fit into the leaner plant your team is envisioning?
Karen Wilhelm has worked in the manufacturing industry for 25 years, and blogs at Lean Reflections, which has been named as one of the top ten lean blogs on the web.
Image Credit: Second image courtesy of Creative Commons: Attribution – Share Alike 3.0
- Category:
- Industry
- Manufacturing
Some opinions expressed in this article may be those of a contributing author and not necessarily Gray.
Related News & Insights
Advanced Technology
The Opportunities and Challenges of a Second Trump Presidency
Opinion
Advanced Technology, Automation & Controls
Four Use Cases for AI's Growing Role in Manufacturing
Industry
November 25, 2024Data Centers
Gray Expands Reach with Dallas Office
Corporate News
November 14, 2024